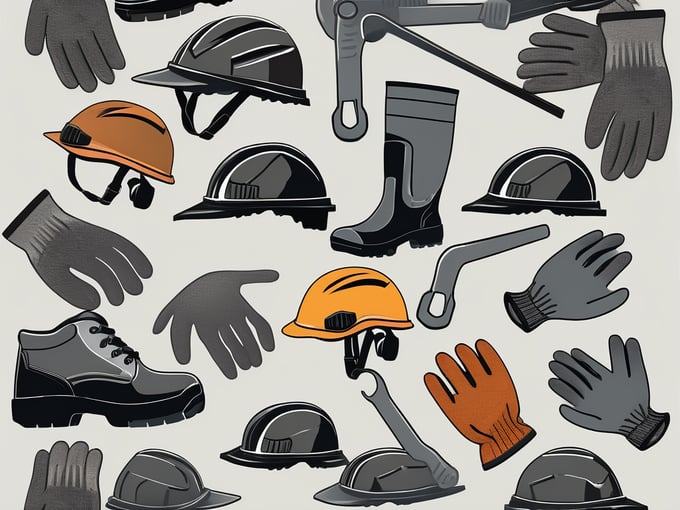
In the sludge management industry, asset management is a crucial aspect that safety officers need to fully understand and implement. It plays a vital role in ensuring the safety and efficiency of operations, as well as maximizing the lifespan of assets. This comprehensive guide aims to provide safety officers in the sludge management industry with the knowledge and tools necessary to effectively manage assets and enhance safety protocols.
Understanding the Importance of Asset Management in the Sludge Management Industry
Defining Asset Management and Its Role
Asset management refers to the systematic process of planning, monitoring, and maintaining assets throughout their lifecycle. In the sludge management industry, assets encompass a wide range of equipment and infrastructure, from treatment plants and pipelines to vehicles and machinery. Effective asset management involves identifying and cataloging these assets, establishing maintenance and repair strategies, and ensuring compliance with safety regulations and standards.
Asset management is crucial in the sludge management industry due to the complex nature of the operations involved. Sludge, which is the byproduct of wastewater treatment, requires careful handling and disposal to prevent environmental contamination and health hazards. Therefore, managing assets effectively becomes essential to ensure the smooth operation of treatment plants, the transportation of sludge, and the maintenance of equipment.
One aspect of asset management is the identification and cataloging of assets. This involves creating a comprehensive inventory of all the equipment and infrastructure used in sludge management. Each asset is assigned a unique identifier and categorized based on its type, location, and criticality. This information is crucial for maintenance planning, as it helps prioritize assets that require immediate attention and ensures that the right resources are allocated.
Another important aspect of asset management is establishing maintenance and repair strategies. Regular inspections, preventive maintenance, and timely repairs are essential to keep assets in optimal condition and minimize downtime. By implementing a proactive approach to maintenance, sludge management companies can avoid costly breakdowns and extend the lifespan of their assets.
The Connection Between Asset Management and Safety
Asset management and safety go hand in hand. By properly managing assets, safety officers can mitigate risks, prevent accidents, and protect workers and the environment. Well-maintained equipment and infrastructure reduce the likelihood of failures and minimize the potential impact on safety. Implementing safety measures throughout the asset lifecycle, from procurement to retirement, enhances operational efficiency and safeguards against hazardous situations.
One of the key ways asset management contributes to safety is through the implementation of regular inspections and maintenance. By conducting routine inspections, potential issues can be identified and addressed before they escalate into safety hazards. For example, pipelines used in sludge transportation may develop leaks over time, which can lead to spills and environmental contamination. By regularly inspecting these pipelines and repairing any damages, the risk of leaks and subsequent accidents can be significantly reduced.
Furthermore, effective asset management ensures compliance with safety regulations and standards. The sludge management industry is subject to various safety guidelines and environmental regulations, which aim to protect both workers and the surrounding communities. By maintaining accurate records of asset inspections, repairs, and safety measures, companies can demonstrate their commitment to safety and regulatory compliance.
Additionally, asset management plays a crucial role in emergency preparedness. In the event of a natural disaster or unforeseen circumstances, having a well-maintained and properly managed asset base allows for a more efficient response. Quick access to necessary equipment and infrastructure can help minimize the impact of such events and facilitate the recovery process.
In conclusion, asset management is of utmost importance in the sludge management industry. It ensures the smooth operation of treatment plants, minimizes safety risks, and promotes environmental sustainability. By effectively managing assets, sludge management companies can optimize their operations, reduce costs, and uphold their commitment to safety and regulatory compliance.
Key Components of Effective Asset Management
Asset management is a crucial aspect of any organization's operations. It involves the systematic and strategic handling of assets to ensure their optimal performance, longevity, and value. Effective asset management requires the implementation of various key components, including:
Inventory Management and Control
Accurate inventory management is pivotal in asset management. Safety officers must maintain an up-to-date inventory of all assets, including detailed information such as location, condition, and maintenance history. This comprehensive inventory serves as a foundation for effective asset management practices.
Utilizing digital tools and asset tracking software facilitates real-time monitoring, simplifies data management, and enables efficient inventory control. These technologies provide safety officers with the ability to track assets, monitor their usage, and identify any potential issues or discrepancies in a timely manner.
Moreover, with the help of asset tracking software, safety officers can generate reports and analytics that provide valuable insights into asset utilization, maintenance costs, and overall asset performance. This data-driven approach allows for informed decision-making and the optimization of asset management strategies.
Maintenance and Repair Strategies
To ensure the longevity and optimal performance of assets, safety officers need to establish maintenance and repair strategies. This involves implementing preventive maintenance schedules, conducting regular inspections, and promptly addressing any issues identified.
Efficient maintenance planning not only minimizes the risk of asset failures but also decreases downtime and extends the lifespan of equipment. By adhering to a proactive maintenance approach, safety officers can identify and resolve potential problems before they escalate, thereby reducing the overall maintenance costs and ensuring uninterrupted operations.
Additionally, safety officers should prioritize training and equipping their maintenance teams with the necessary skills and tools to carry out effective repairs. Regular training sessions and workshops can enhance the technical knowledge and capabilities of the maintenance staff, enabling them to handle complex repairs and optimize asset performance.
Asset Lifecycle Management
Managing assets throughout their lifecycle is essential for safety officers. This comprehensive approach involves planning asset acquisition, monitoring asset performance, and making informed decisions about asset decommissioning or replacement.
By strategically evaluating assets over time, safety officers can optimize resource allocation, improve operational efficiency, and proactively address safety concerns. Regular performance assessments and data analysis help identify assets that are no longer cost-effective or fail to meet operational requirements.
Furthermore, safety officers should consider factors such as technological advancements, industry standards, and regulatory compliance when making decisions about asset replacement or decommissioning. Upgrading to newer and more efficient assets can result in improved productivity, reduced maintenance costs, and enhanced safety measures.
Overall, effective asset management requires a comprehensive understanding of an organization's assets, their lifecycle, and the implementation of proactive strategies to ensure their optimal performance and value.
The Role of Safety Officers in Asset Management
Safety officers play a vital role in ensuring the safe and efficient operation of asset management in the sludge management industry. Their responsibilities go beyond simply overseeing safety regulations and standards; they are the guardians of worker well-being, environmental protection, and the organization's reputation.
Overseeing Safety Regulations and Standards
One of the primary responsibilities of safety officers is to ensure compliance with safety regulations and standards governing the sludge management industry. This involves staying up-to-date on the latest legislation, conducting regular safety audits, and implementing necessary corrective actions. By diligently incorporating safety requirements into asset management practices, safety officers safeguard workers, protect the environment, and uphold the reputation of the organization.
Moreover, safety officers act as the bridge between regulatory bodies and the organization, ensuring that all safety-related documentation and permits are in order. They work closely with government agencies and industry associations to stay informed about any changes in safety regulations and standards, and then communicate these updates to relevant stakeholders within the organization.
Implementing Safety Measures in Asset Management
While overseeing safety regulations is crucial, safety officers also play a proactive role in developing and implementing safety measures throughout the asset management process. They conduct comprehensive risk assessments to identify potential hazards and vulnerabilities, and then devise strategies to mitigate them.
Creating a strong safety culture is another essential aspect of the safety officer's role. They promote safety awareness among employees, encouraging them to prioritize safe work practices and report any safety concerns promptly. By fostering a culture of safety, safety officers empower employees to take ownership of their own well-being and contribute to a safer working environment.
Furthermore, safety officers provide training and guidance to employees at all levels. They ensure that everyone understands the proper use of safety equipment, follows established safety protocols, and knows how to respond in emergency situations. Regular safety drills and exercises are conducted to test the effectiveness of these measures and identify areas for improvement.
Effective communication is also a key responsibility of safety officers. They facilitate open lines of communication between various stakeholders, including management, employees, contractors, and external safety experts. By promoting transparent and effective communication, safety officers ensure that safety-related information is disseminated efficiently and that all parties are aware of their roles and responsibilities in maintaining a safe working environment.
In conclusion, safety officers are integral to asset management in the sludge management industry. Their role extends beyond overseeing safety regulations and standards; they actively contribute to the development and implementation of safety measures. By prioritizing safety, safety officers create a secure and efficient working environment that benefits workers, the environment, and the organization as a whole.
Technology and Tools for Asset Management
Asset management practices in the sludge management industry have undergone a remarkable transformation, thanks to advancements in technology. Today, various software solutions offer comprehensive asset tracking capabilities, empowering safety officers with the ability to monitor asset location, maintenance schedules, and performance indicators.
These modern software solutions have revolutionized data management in asset tracking. Safety officers can now easily access and analyze asset-related information, facilitating informed decision-making. With just a few clicks, they can generate reports, track asset performance trends, and identify areas for improvement.
Furthermore, these software tools have significantly enhanced overall asset management efficiency. By automating manual processes, such as data entry and report generation, safety officers can allocate their time and resources more effectively. This allows them to focus on critical tasks, such as identifying potential risks, implementing preventive measures, and ensuring regulatory compliance.
Modern Software Solutions for Asset Tracking
One of the key features of modern asset tracking software solutions is their ability to provide real-time asset location tracking. Through the integration of GPS technology, safety officers can pinpoint the exact location of each asset, whether it is in the field or in a storage facility. This feature not only improves asset visibility but also helps prevent loss or theft.
In addition to location tracking, these software solutions also enable safety officers to schedule and track asset maintenance. By setting up automated reminders and notifications, they can ensure that assets are maintained regularly and in a timely manner. This proactive approach to maintenance helps prevent unexpected breakdowns and extends the lifespan of assets, ultimately reducing operational costs.
Moreover, modern asset tracking software solutions offer performance indicators that provide valuable insights into asset utilization and efficiency. Safety officers can monitor key metrics, such as asset downtime, utilization rates, and energy consumption, to identify areas for improvement. Armed with this information, they can make data-driven decisions to optimize asset utilization and reduce unnecessary expenses.
The Impact of Automation and AI in Asset Management
While software solutions have already transformed asset management practices, the potential of automation and artificial intelligence (AI) in this field is even more promising. The emergence of the Internet of Things (IoT) sensors and predictive analytics algorithms has opened up new possibilities for proactive asset management.
IoT sensors can collect real-time data on asset performance, such as temperature, pressure, and vibration. This data is then analyzed using predictive analytics algorithms, which can identify patterns and anomalies. By detecting early signs of asset performance issues, safety officers can take preventive measures, such as scheduling maintenance or replacing components, before a breakdown occurs.
Furthermore, AI-powered asset management systems can optimize asset utilization by analyzing historical data and predicting future demand. By considering factors such as production schedules, maintenance requirements, and market trends, these systems can recommend the most efficient allocation of assets. This not only maximizes productivity but also minimizes downtime and reduces unnecessary asset purchases.
However, it is crucial for safety officers to stay informed about emerging technologies and assess their feasibility and potential benefits in their specific operational contexts. Implementing automation and AI in asset management requires careful planning, considering factors such as cost, compatibility with existing systems, and training requirements. Nonetheless, the potential benefits in terms of improved asset performance, reduced costs, and enhanced operational efficiency make it a worthwhile investment for many organizations.
Developing an Asset Management Plan
Identifying Goals and Objectives
Developing a clear asset management plan starts with identifying goals and objectives. Safety officers should establish specific targets, such as reducing equipment downtime, improving asset reliability, or increasing overall safety performance. Goals should be measurable, attainable, relevant, and time-bound to ensure effective planning and monitoring.
Risk Assessment and Mitigation
Risk assessment is a crucial step in developing an asset management plan. Safety officers must systematically identify and evaluate potential risks associated with various assets and their operating conditions. By implementing risk mitigation measures, such as redundancy plans or improved safety protocols, safety officers can safeguard both workers and assets from potential harm.
Continuous Improvement and Review
An effective asset management plan is a continuous process. Safety officers should regularly review and assess the plan's effectiveness and make necessary adjustments. By continuously seeking opportunities for improvement, evaluating asset performance, and learning from past experiences, safety officers can optimize asset management practices and enhance safety protocols.
Training and Skill Development for Safety Officers
Essential Skills for Effective Asset Management
To excel in asset management, safety officers require a diverse skill set. This includes proficiency in data analysis, risk assessment, project management, and regulatory compliance. Additionally, strong communication and leadership skills are essential for effectively collaborating with cross-functional teams and promoting a culture of safety and continuous improvement.
Ongoing Training and Development Opportunities
The sludge management industry is constantly evolving, necessitating continuous learning and skill development for safety officers. Organizations should invest in training programs that cover new technologies, updated safety regulations, and emerging best practices. By providing ongoing training opportunities, organizations ensure that their safety officers remain knowledgeable, adaptable, and up to date with industry advancements.
Overcoming Challenges in Asset Management
Addressing Common Obstacles
Asset management in the sludge management industry comes with its fair share of challenges. Limited budgetary resources, complex regulatory frameworks, and the need for cross-organizational collaboration are just a few examples. Safety officers must proactively identify and address these challenges through effective communication, data-driven decision-making, and a proactive approach towards problem-solving.
Strategies for Effective Problem-Solving
Problem-solving is a critical skill for safety officers involved in asset management. By adopting a systematic approach, breaking down complex issues, and involving relevant stakeholders, safety officers can effectively resolve challenges. Encouraging an open and collaborative work environment enables collective problem-solving, fosters knowledge sharing, and enhances overall asset management effectiveness.
The Future of Asset Management in the Sludge Management Industry
Emerging Trends and Innovations
The sludge management industry is witnessing various emerging trends and innovations that will shape the future of asset management. Internet of Things (IoT) devices, big data analytics, and machine learning are increasingly utilized to optimize asset performance, predict maintenance needs, and boost overall operational efficiency. Safety officers need to embrace these advancements to stay ahead of the curve and ensure a sustainable future for their organizations.
Preparing for Future Changes and Challenges
As the sludge management industry evolves, safety officers must proactively prepare for future changes and challenges. This includes staying updated on industry developments, actively participating in industry associations and conferences, and networking with professionals in related fields. By consistently seeking knowledge and engaging in forward-thinking practices, safety officers can position themselves and their organizations for future success.
By understanding the importance of asset management, leveraging technology and tools, and addressing challenges head-on, safety officers in the sludge management industry can fulfill their crucial role in maintaining the safety and efficiency of operations. With continuous learning, proactive planning, and a commitment to safety, safety officers can navigate the complexities of asset management and contribute to a sustainable and secure working environment.