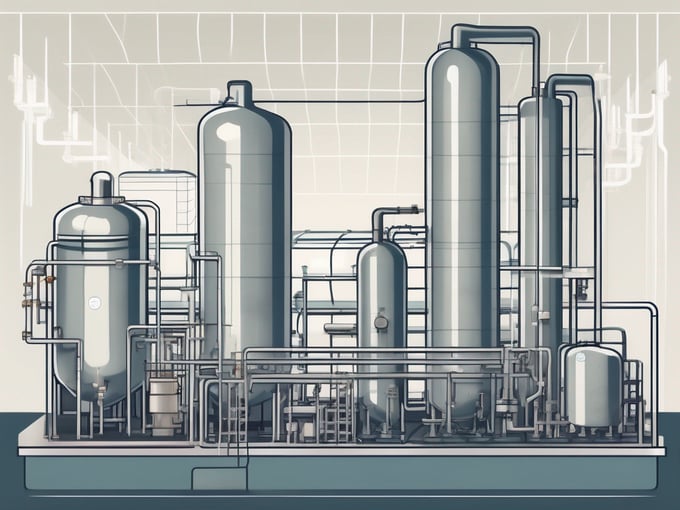
Basics of Preventative Maintenance for Plant Operators in the Wastewater Industry
The wastewater industry plays a critical role in maintaining public health and protecting the environment. To ensure the efficient and safe operation of wastewater treatment plants, plant operators must prioritize preventative maintenance. Understanding the importance of preventative maintenance and implementing essential maintenance tasks is key to optimizing plant efficiency and reducing costly repair work. This comprehensive guide will outline the key aspects of preventative maintenance for plant operators in the wastewater industry and provide valuable insights into safety measures, tools, training, and overcoming common maintenance challenges.
Understanding the Importance of Preventative Maintenance
Preventative maintenance is the proactive approach to plant maintenance that involves regularly inspecting, testing, and servicing equipment to identify and address potential issues before they escalate into major problems. In the wastewater industry, where continuous operation is crucial, preventative maintenance helps minimize downtime, improve plant performance, and extend the lifespan of equipment. By implementing preventative maintenance strategies, plant operators can reduce the risk of equipment failure, optimize energy consumption, and enhance overall plant efficiency.
One of the key aspects of preventative maintenance is regular inspections. Plant operators meticulously examine each piece of equipment, from pumps to valves, to ensure they are in optimal condition. During these inspections, they check for signs of wear and tear, corrosion, leaks, and any other potential issues that may impact the equipment's performance. By identifying these issues early on, operators can take immediate action to address them, preventing further damage and potential failures.
Another important component of preventative maintenance is testing. Plant operators conduct various tests to assess the performance and functionality of equipment. For example, they may measure the flow rate of pumps, test the accuracy of sensors, or analyze the efficiency of motors. These tests provide valuable data that helps operators identify any deviations from normal operating conditions and take corrective measures accordingly. By regularly testing equipment, operators can detect problems before they become critical, ensuring the smooth operation of the wastewater treatment plant.
The Role of Preventative Maintenance in the Wastewater Industry
Preventative maintenance plays a vital role in the wastewater industry as it helps to ensure the reliable and uninterrupted treatment of wastewater. By regularly inspecting and servicing equipment, plant operators can identify and address issues such as pump wear and tear, belt misalignment, valve malfunctions, and motor issues. Addressing these problems promptly not only prevents costly repairs but also maintains the plant's capacity to meet regulatory requirements and protect public health.
Moreover, preventative maintenance helps wastewater treatment plants maintain compliance with environmental regulations. Regular inspections and maintenance activities ensure that equipment is operating within the specified parameters and that the treatment process is meeting the required standards. By adhering to these regulations, wastewater treatment plants can avoid penalties and maintain a positive reputation within the community.
Furthermore, preventative maintenance contributes to the overall efficiency of wastewater treatment plants. Well-maintained equipment operates more efficiently, consuming less energy and reducing operational costs. By optimizing energy consumption, plant operators can minimize their environmental impact and contribute to sustainable wastewater management.
Key Benefits of Regular Maintenance
Regular preventative maintenance offers several key benefits to wastewater plant operators. Firstly, it helps to detect and resolve minor equipment issues early, preventing them from turning into more significant and costly problems. By addressing these issues promptly, operators can avoid unexpected breakdowns and the associated downtime, ensuring uninterrupted wastewater treatment.
Secondly, regular maintenance prolongs the lifespan of equipment. By keeping equipment in optimal condition, plant operators can avoid premature failures and the need for frequent replacements. This not only saves costs but also reduces the environmental impact of equipment disposal and replacement.
Thirdly, preventative maintenance improves energy efficiency. Properly maintained equipment operates more efficiently, consuming less energy compared to poorly maintained or faulty equipment. This energy optimization not only reduces operational costs but also contributes to sustainable wastewater management by minimizing the plant's carbon footprint.
In conclusion, preventative maintenance is an essential practice in the wastewater industry. By regularly inspecting, testing, and servicing equipment, plant operators can ensure the reliable and uninterrupted treatment of wastewater, comply with environmental regulations, and optimize overall plant efficiency. The benefits of preventative maintenance include early detection and resolution of equipment issues, reduced downtime, prolonged equipment lifespan, and improved energy efficiency. By prioritizing preventative maintenance, wastewater treatment plants can operate effectively, protect public health, and contribute to a more sustainable future.
Essential Maintenance Tasks for Wastewater Plant Operators
Wastewater plant operators play a crucial role in maintaining the smooth operation of wastewater treatment facilities. To ensure the efficient and effective treatment of wastewater, operators must perform a variety of maintenance tasks on a regular basis. These tasks can be categorized into daily, weekly, and monthly activities, each serving a specific purpose in maintaining the overall functionality of the plant.
Daily Maintenance Tasks
Every day, wastewater plant operators diligently carry out a range of maintenance tasks to keep the facility in optimal condition. One of the key responsibilities is to inspect and clean screens, filters, and grinders. By doing so, operators prevent clogging and ensure the uninterrupted flow of wastewater through the treatment process.
In addition, operators check and record the levels of chemicals used in the treatment processes. This helps maintain the proper balance of chemicals, ensuring effective treatment and preventing any adverse effects on the environment.
Lubricating the moving parts of equipment, such as pumps, motors, and conveyors, is another crucial task. By reducing friction and wear, operators extend the lifespan of the equipment and minimize the risk of breakdowns or malfunctions.
Furthermore, operators pay close attention to the sealing of equipment and conduct regular inspections for leaks or abnormal vibrations. Identifying and addressing these issues promptly helps maintain the integrity of the system and prevents any potential hazards.
Weekly Maintenance Tasks
On a weekly basis, wastewater plant operators perform additional maintenance tasks to ensure the smooth operation of the facility. One of these tasks involves inspecting and cleaning clarifiers, settling tanks, and other sedimentation equipment. By removing accumulated solids, operators maintain the efficiency of these components and prevent any potential blockages.
Cleaning and calibrating sensors and meters used for monitoring water quality is another important weekly task. Accurate readings are essential for gauging the effectiveness of the treatment process and ensuring compliance with regulatory standards.
Testing emergency backup systems and alarms is also a critical weekly task. By verifying the proper functioning of these systems, operators ensure that the facility is prepared to handle any unforeseen circumstances or power outages, minimizing the risk of disruptions to the treatment process.
Inspecting and cleaning sludge dewatering equipment is yet another crucial weekly maintenance task. This process helps maintain the efficiency of the dewatering process, ensuring the proper removal of solids from the wastewater.
Monthly Maintenance Tasks
On a monthly basis, wastewater plant operators carry out a series of maintenance tasks to address specific areas of the facility. Inspecting and cleaning aeration systems, diffusers, and blowers is one such task. These components play a vital role in providing the necessary oxygenation for the treatment process. By ensuring their proper functioning, operators optimize the treatment efficiency and maintain the desired water quality.
Checking and adjusting chemical dosing systems is another important monthly task. Accurate dosing of treatment chemicals is crucial for achieving the desired treatment outcomes. By regularly monitoring and adjusting the dosing systems, operators ensure the proper dosage of chemicals, maximizing the effectiveness of the treatment process.
Inspecting and cleaning UV disinfection systems is also a monthly maintenance task. UV disinfection is a key step in eliminating harmful microorganisms from the wastewater. By keeping the UV systems clean and well-maintained, operators ensure the continued effectiveness of this disinfection method.
Lastly, operators conduct vibration analysis and thermal imaging on critical equipment as part of their monthly maintenance routine. These diagnostic techniques help identify any potential issues or abnormalities in the equipment, allowing operators to address them proactively and prevent any unplanned downtime or equipment failures.
In conclusion, wastewater plant operators perform a wide range of maintenance tasks on a daily, weekly, and monthly basis to ensure the smooth and efficient operation of the facility. By diligently carrying out these tasks, operators contribute to the effective treatment of wastewater, protecting the environment and public health.
Safety Measures in Preventative Maintenance
Ensuring the safety of plant operators during maintenance operations is of utmost importance. Implementing proper safety measures and providing appropriate personal protective equipment (PPE) is essential to prevent accidents and injuries.
When it comes to preventative maintenance, safety should always be the top priority. By taking proactive steps to protect plant operators, companies can minimize the risk of accidents and create a safe working environment.
One important aspect of safety in maintenance work is the use of personal protective equipment (PPE). Plant operators should wear safety glasses to shield their eyes from potential hazards such as chemical splashes or flying debris. Gloves are also crucial in protecting the hands from cuts, burns, or exposure to harmful substances. Hard hats are essential to prevent head injuries in case of falling objects, while steel-toed boots provide protection against foot injuries.
However, PPE requirements may vary depending on the nature of the maintenance work. For instance, in areas where harmful gases or fumes are present, respiratory protection in the form of masks or respirators may be necessary. This additional layer of protection ensures that operators are not exposed to hazardous substances that could harm their respiratory system.
Safety Protocols during Maintenance Operations
Plant operators should follow established safety protocols when performing maintenance tasks. These protocols are designed to minimize risks and prevent accidents from occurring. By adhering to these guidelines, operators can carry out their duties in a safe and controlled manner.
One crucial safety protocol is the isolation of equipment. Before any maintenance work begins, operators must ensure that the equipment is properly isolated from any energy sources. This includes shutting off power supplies, closing valves, and locking out machinery to prevent accidental startup. By taking these precautions, operators can significantly reduce the risk of electrical shocks or other accidents caused by unexpected equipment activation.
In addition to isolating equipment, displaying clear warning signs is vital to alert other personnel to the ongoing maintenance work. These signs serve as a visual reminder to exercise caution and avoid entering restricted areas. By clearly communicating potential hazards, companies can create a safer work environment for everyone involved.
Regular safety training and communication are also crucial in maintaining a safe working environment. By providing ongoing training sessions, companies can ensure that plant operators are aware of the latest safety procedures and best practices. Furthermore, open lines of communication between operators and management enable the reporting of any safety concerns or near-miss incidents, allowing for prompt action and continuous improvement.
In conclusion, safety measures in preventative maintenance are essential for protecting plant operators and preventing accidents. By providing appropriate personal protective equipment and following established safety protocols, companies can create a safe working environment that prioritizes the well-being of their personnel.
Tools and Equipment for Preventative Maintenance
A variety of tools and equipment are essential for carrying out maintenance tasks effectively and efficiently. Without the proper tools, maintenance tasks can become time-consuming and less effective, potentially leading to equipment failures and costly repairs.
Essential Tools for Maintenance Tasks
When it comes to routine maintenance, there are several common tools that are necessary to have on hand. Wrenches of various sizes are essential for loosening and tightening bolts and nuts. Screwdrivers, both flathead and Phillips, are indispensable for removing and installing screws. Pliers are versatile tools that can be used for gripping, bending, and cutting wires or small components.
In addition to these basic tools, multimeters are crucial for electrical testing. They allow maintenance technicians to measure voltage, current, and resistance, helping them diagnose and troubleshoot electrical issues. These handheld devices are invaluable for ensuring the safety and proper functioning of electrical systems.
However, maintenance tasks can vary greatly depending on the specific equipment or machinery being serviced. In such cases, specialized tools may be required. For example, pipe cutters are essential for cutting and shaping pipes in plumbing systems. Pressure gauges are necessary for measuring and monitoring pressure levels in hydraulic or pneumatic systems. Flow meters are used to measure and control the flow rate of liquids or gases in pipelines.
Innovative Technologies for Maintenance Efficiency
Advancements in technology have revolutionized the field of maintenance, introducing innovative tools and equipment that enhance efficiency and accuracy. These technologies not only streamline maintenance processes but also help prevent unexpected equipment failures.
Predictive maintenance software is one such innovation that has gained popularity in recent years. This software utilizes data analytics and machine learning algorithms to predict equipment failures before they occur. By analyzing historical data and monitoring real-time performance, the software can identify patterns and anomalies that may indicate potential issues. Maintenance tasks can then be scheduled proactively, minimizing downtime and reducing the risk of costly breakdowns.
Remote monitoring systems have also become increasingly prevalent in maintenance operations. These systems allow plant operators to monitor equipment performance and detect issues from a centralized control room. By utilizing sensors and data communication technologies, remote monitoring systems provide real-time data on equipment health, allowing maintenance teams to identify problems early on and take appropriate actions. This not only improves maintenance efficiency but also enhances safety by reducing the need for manual inspections in hazardous environments.
In conclusion, having the right tools and equipment is essential for carrying out preventative maintenance effectively. From basic hand tools to specialized instruments, each tool plays a crucial role in ensuring the smooth operation of equipment. Furthermore, the integration of innovative technologies, such as predictive maintenance software and remote monitoring systems, has revolutionized the maintenance field, enabling proactive and data-driven maintenance practices.
Training and Skills Development for Maintenance Work
Developing and enhancing the necessary skills for effective maintenance work is crucial for plant operators.
Necessary Skills for Effective Maintenance
Plant operators should possess a strong understanding of electromechanical systems, equipment operation, and maintenance techniques. Additionally, they should have good problem-solving skills, the ability to interpret technical manuals and diagrams, and a thorough knowledge of safety procedures.
Training Programs for Wastewater Plant Operators
Plant operators can enhance their maintenance skills through specialized training programs offered by industry organizations and vocational schools. These programs cover topics such as equipment maintenance, troubleshooting, safety protocols, and emerging technologies. Regular training and professional development opportunities ensure that plant operators stay up-to-date with the latest industry practices and advancements.
Developing a Preventative Maintenance Schedule
Creating a well-planned and thoughtful maintenance schedule is crucial for effective preventative maintenance.
Factors to Consider in Creating a Maintenance Schedule
When developing a maintenance schedule, plant operators should consider factors such as equipment manufacturer recommendations, historical data on equipment failures, regulatory requirements, and plant workload. The schedule should be comprehensive, taking into account both routine maintenance tasks and periodic inspections.
Implementing and Adhering to a Maintenance Schedule
Once a maintenance schedule is established, it is essential to implement it consistently. Plant operators should prioritize scheduling downtime for maintenance tasks, ensuring that all necessary resources are available. Regular review and adjustment of the maintenance schedule based on feedback and evaluation of its effectiveness are also vital.
Overcoming Common Maintenance Challenges
Plant operators often face challenges when it comes to maintenance. Identifying potential maintenance issues and finding appropriate solutions is crucial for maintaining operational efficiency.
Identifying Potential Maintenance Issues
A proactive approach to maintenance involves regularly inspecting equipment and monitoring performance indicators to identify potential issues before they escalate. Data analysis can be helpful in detecting trends or patterns that may indicate impending equipment failure.
Solutions to Common Maintenance Problems
Common maintenance problems, such as equipment vibration or excessive energy consumption, may require specific solutions. This can include recalibrating sensors, aligning belts, replacing worn-out parts, or implementing energy-saving measures such as variable frequency drives. Collaboration with specialized technicians and equipment suppliers can provide valuable insights and expertise for addressing complex maintenance challenges. Regular communication and knowledge sharing among plant operators also play a crucial role in problem-solving.
In conclusion, preventative maintenance is an essential aspect of wastewater plant operations. By understanding its importance, implementing essential maintenance tasks, ensuring safety measures, utilizing the right tools, acquiring necessary skills through training, developing a maintenance schedule, and effectively addressing common maintenance challenges, plant operators can optimize plant efficiency, reduce downtime, and maintain compliance with regulatory standards. Prioritizing preventative maintenance not only ensures the efficient and safe operation of wastewater treatment plants but also contributes to the sustainability and environmental protection in the wastewater industry.