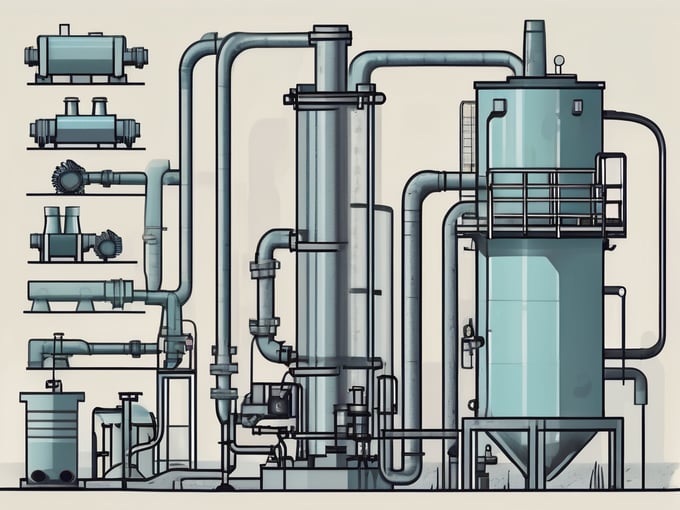
Basics of Preventative Maintenance for Technicians in the Wastewater Industry
Preventative maintenance plays a crucial role in the wastewater industry by ensuring the reliability and longevity of equipment and systems. It involves regular inspections, scheduled servicing, and the use of predictive maintenance techniques to identify and address potential issues before they become major problems. In this comprehensive guide, we will explore the definition and importance of preventative maintenance in the wastewater industry, discuss key components of a preventative maintenance program, examine tools and technologies that can enhance its effectiveness, highlight safety considerations, and delve into the training and skills required for effective maintenance. Additionally, we will analyze the cost-benefit of preventative maintenance, provide practical steps for implementing a maintenance plan, and explore the future trends and innovations shaping the industry. Let's dive in!
Understanding Preventative Maintenance
Definition and Importance of Preventative Maintenance
Preventative maintenance refers to the proactive approach of regular inspections, servicing, and predictive techniques to prevent equipment failure and downtime. It involves a systematic process designed to increase equipment reliability, decrease maintenance costs, and ensure optimal performance. By implementing a preventative maintenance program, wastewater industry technicians can prevent sudden breakdowns, costly repairs, and potential environmental hazards.
Effective preventative maintenance enhances the lifespan of assets, reduces the risk of emergencies, improves operational efficiency, and minimizes unplanned downtime. It allows technicians to identify and address minor issues before they escalate into major problems, saving both time and money in the long run. Furthermore, it plays a critical role in ensuring compliance with regulatory frameworks governing the wastewater industry, promoting safety, and protecting the environment.
One of the key aspects of preventative maintenance is regular inspections. Technicians conduct thorough examinations of equipment, looking for signs of wear and tear, loose connections, or any other potential issues. These inspections involve visual checks, measurements, and tests to assess the condition of the equipment and identify any areas that require attention.
Another important component of preventative maintenance is servicing. This involves performing routine maintenance tasks such as lubrication, cleaning, and calibration. By regularly servicing equipment, technicians can ensure that it operates at its optimal level, reducing the risk of breakdowns and improving overall performance.
Predictive techniques are also utilized in preventative maintenance. These techniques involve the use of advanced technologies and tools to monitor the condition of equipment and predict potential failures. By analyzing data and trends, technicians can identify patterns that indicate the need for maintenance or replacement, allowing them to take proactive measures before any issues arise.
The Role of Preventative Maintenance in the Wastewater Industry
In the wastewater industry, preventative maintenance is essential to maintain the smooth functioning of various equipment and systems. Key components such as pumps, motors, valves, filters, and control systems need regular attention to ensure uninterrupted operation. By conducting routine inspections and servicing, technicians can identify signs of wear and tear, corrosion, leaks, or any other potential issues that may impact the efficiency of the overall wastewater treatment process.
Moreover, preventative maintenance helps prevent the accumulation of solids, grease, and other debris, which can lead to clogs, blockages, and costly repairs. By implementing preventive measures, technicians can safeguard the integrity of pipes, tanks, and other infrastructure components, reducing the risk of leaks, spills, and contamination.
Regular maintenance of pumps is crucial in the wastewater industry. Pumps play a vital role in the movement of wastewater throughout the treatment process. They are responsible for transferring wastewater from one stage to another, ensuring that it undergoes the necessary treatment processes. Without proper maintenance, pumps can experience issues such as decreased efficiency, reduced flow rates, or even complete failure. This can disrupt the entire wastewater treatment process, leading to delays, increased costs, and potential environmental hazards.
Valves are another critical component that requires regular maintenance. Valves control the flow of wastewater and other fluids within the treatment system. They ensure that the right amount of wastewater is directed to each stage, maintaining the balance and efficiency of the process. Regular inspections and servicing of valves help identify any leaks, blockages, or malfunctions that may hinder their proper operation. By addressing these issues promptly, technicians can prevent disruptions and ensure the smooth flow of wastewater through the treatment system.
Furthermore, filters play a crucial role in removing solid particles and contaminants from wastewater. Over time, filters can become clogged with debris, reducing their effectiveness and potentially causing damage to downstream equipment. Regular maintenance of filters involves cleaning or replacing them as needed, ensuring that they continue to function optimally and prevent any blockages or damage to the wastewater treatment process.
Overall, preventative maintenance is a fundamental practice in the wastewater industry. It not only helps maintain the efficiency and reliability of equipment but also contributes to the protection of the environment and public health. By implementing a comprehensive preventative maintenance program, wastewater industry technicians can ensure the smooth operation of wastewater treatment systems, minimize the risk of emergencies, and uphold regulatory compliance.
Key Components of Preventative Maintenance
Preventative maintenance is a crucial aspect of ensuring the longevity and reliability of equipment and systems. By implementing a comprehensive maintenance program, organizations can minimize unexpected breakdowns, reduce repair costs, and maximize operational efficiency. The key components of preventative maintenance include regular equipment inspections, scheduled equipment servicing, and the use of predictive maintenance techniques.
Regular Equipment Inspections
One of the fundamental components of preventative maintenance is regular equipment inspections. Technicians should conduct visual inspections to identify any visible signs of damage, leaks, corrosion, or abnormal operating conditions. They should also use specialized tools and instruments to measure performance parameters such as flow rates, pressure levels, temperature, and vibration.
Inspections should encompass all critical equipment and systems, including pumps, motors, valves, filters, and control panels. By thoroughly examining each component, technicians can detect early signs of malfunction or potential issues that may impact performance or safety. Regular inspections also provide an opportunity to assess the effectiveness of previous maintenance actions and make any necessary adjustments.
For example, during an inspection of a pump, technicians may notice a slight decrease in flow rate. This observation prompts them to investigate further and discover a clogged filter, which, if left unaddressed, could have led to a complete pump failure. By catching this issue early on, the technicians can clean the filter and restore the pump's optimal performance.
Scheduled Equipment Servicing
In addition to regular inspections, scheduled equipment servicing is a vital part of preventative maintenance. This involves performing routine maintenance tasks such as lubrication, filter replacements, belt adjustments, and cleaning. Adhering to manufacturer guidelines and industry best practices, technicians should create a maintenance schedule that outlines specific servicing intervals for each piece of equipment.
Servicing tasks should be carried out in accordance with established safety protocols to protect both technicians and the surrounding environment. Technicians should document all service activities, including date, time, performed tasks, and any observations or recommendations for future actions.
For instance, during a scheduled servicing of a motor, technicians may notice that the lubrication levels are lower than recommended. By promptly replenishing the lubricant, they prevent excessive friction and wear, ensuring optimal motor performance and extending its lifespan.
Predictive Maintenance Techniques
While regular inspections and scheduled servicing form the foundation of preventative maintenance, the use of predictive maintenance techniques can further enhance the effectiveness of the program. Predictive maintenance relies on data analysis and condition monitoring to identify patterns and indicators of potential equipment failure or degradation.
Technicians can utilize various techniques, such as vibration analysis, thermography, oil analysis, and ultrasonic testing, to assess the condition and performance of critical equipment. By analyzing trends and deviations from normal operating parameters, technicians can predict potential failures and plan maintenance activities accordingly. Predictive maintenance minimizes unplanned downtime, avoids unnecessary servicing, and optimizes maintenance resources.
For example, through vibration analysis, technicians may notice an increasing trend in vibration levels of a rotating equipment. This trend indicates a potential misalignment issue, which, if left unaddressed, could lead to severe damage and costly repairs. By identifying this issue early on, technicians can schedule a maintenance intervention to realign the equipment and prevent further damage.
In conclusion, preventative maintenance encompasses regular equipment inspections, scheduled equipment servicing, and the use of predictive maintenance techniques. By implementing a comprehensive maintenance program that incorporates these key components, organizations can ensure the reliability, safety, and efficiency of their equipment and systems.
Tools and Technologies for Preventative Maintenance
Modern Maintenance Software
Modern maintenance software solutions offer technicians advanced tools to streamline preventative maintenance activities. These software applications provide features such as equipment tracking, automated work order generation, task scheduling, and inventory management. By centralizing maintenance data, technicians can easily access equipment history, track past performance, and plan future maintenance activities more efficiently.
Maintenance software also facilitates data analysis and trend identification, supporting predictive maintenance efforts. This enables technicians to make data-driven decisions, prioritize maintenance tasks, and optimize resource allocation. Ultimately, modern maintenance software enhances the overall effectiveness and efficiency of preventative maintenance programs.
IoT in Preventative Maintenance
The Internet of Things (IoT) is revolutionizing the wastewater industry by enabling connected devices and sensors to collect and transmit real-time data. IoT can be leveraged to monitor critical equipment remotely, track performance parameters, and detect anomalies or deviations from normal operating conditions. This proactive approach supports preventative maintenance by providing technicians with valuable insights into the health and performance of equipment.
By integrating IoT devices with maintenance software, technicians can receive alerts and notifications regarding potential issues, enabling them to take prompt action. IoT technology also facilitates predictive maintenance techniques by enabling trend analysis, data visualization, and advanced analytics. This empowers technicians to make accurate predictions, optimize maintenance schedules, and prevent unexpected equipment failures.
Safety Considerations in Preventative Maintenance
Importance of Safety Protocols
Safety should be a top priority in the wastewater industry, and preventative maintenance is no exception. Technicians should adhere to established safety protocols, including lock-out/tag-out procedures, confined space entry guidelines, and the use of proper personal protective equipment (PPE).
Safe practices reduce the risk of accidents, injuries, and potential hazards associated with working on or around wastewater equipment. Technicians should receive comprehensive safety training and stay updated on industry-specific regulations and best practices. By prioritizing safety, technicians can perform maintenance tasks with confidence and protect themselves and the surrounding environment.
Personal Protective Equipment (PPE) for Technicians
Personal Protective Equipment (PPE) plays a critical role in safeguarding technicians during preventative maintenance activities. Depending on the specific tasks involved, technicians should wear appropriate PPE, including gloves, safety glasses, respirators, protective clothing, and hearing protection.
PPE should be selected based on the potential hazards associated with the equipment being serviced. Technicians should receive training on proper PPE usage, inspection, and maintenance. Regular checks should be conducted to ensure PPE is in good condition and replaced when necessary. By wearing the right PPE, technicians reduce the risk of injuries and exposure to harmful substances.
Training and Skills for Effective Preventative Maintenance
Essential Skills for Wastewater Technicians
Effective preventative maintenance requires technicians to possess a range of skills and knowledge. Technical expertise in areas such as electrical systems, mechanical systems, automation, and instrumentation is essential. Technicians should be proficient in reading technical drawings, schematics, and equipment manuals.
Additionally, problem-solving and troubleshooting skills are critical for identifying and resolving issues efficiently. They should also have a good understanding of industry-specific regulations, safety protocols, and environmental guidelines. Continuous learning and staying up-to-date with advancements in technology and best practices are crucial for technicians to excel in preventative maintenance.
Training Programs and Certifications
Various training programs and certifications are available to help technicians develop the necessary skills for effective preventative maintenance in the wastewater industry. These programs cover topics such as equipment maintenance, safety procedures, regulatory compliance, and emerging technologies.
Technicians can pursue certifications from industry-recognized organizations to demonstrate their expertise and enhance their professional credibility. Obtaining certifications such as Certified Maintenance & Reliability Technician (CMRT) or Certified Maintenance & Reliability Professional (CMRP) can open doors to career advancement opportunities and establish technicians as competent professionals in the field.
Cost-Benefit Analysis of Preventative Maintenance
Understanding the Financial Implications
When considering the implementation of a preventative maintenance program, it is essential to conduct a cost-benefit analysis. This analysis helps assess the financial implications and potential returns on investment. While preventative maintenance does require initial investment, the long-term benefits far outweigh the costs.
The cost-benefit analysis should consider factors such as potential savings from reduced downtime and emergency repairs, increased equipment lifespan, improved operational efficiency, and compliance with regulatory requirements. Additionally, the analysis should take into account the cost of implementing and maintaining the necessary tools, technologies, and training programs.
Long-Term Benefits of Preventative Maintenance
Implementing a well-designed preventative maintenance program yields numerous long-term benefits for the wastewater industry. By preventing unexpected breakdowns and major repairs, organizations can minimize downtime and ensure uninterrupted operation. This translates into increased productivity, cost savings, and a more efficient utilization of maintenance resources.
Furthermore, effective preventative maintenance reduces the risk of environmental incidents, potential fines, and damage to the organization's reputation. It promotes a culture of safety and compliance, fostering a positive work environment for technicians. Additionally, well-maintained equipment consumes less energy, reducing operational costs and contributing to sustainability goals.
Implementing a Preventative Maintenance Program
Steps to Develop a Maintenance Plan
Implementing an effective preventative maintenance program involves several crucial steps. The first step is to assess the current state of equipment and identify potential areas for improvement. This can be done through equipment audits, data analysis, and consultation with technicians.
Next, organizations should develop a comprehensive maintenance plan that includes specific tasks, schedules, responsible parties, and performance metrics. The plan should align with the organization's goals, budgets, and regulatory requirements. It is essential to involve key stakeholders, including technicians, maintenance supervisors, and management personnel, to ensure buy-in and a collaborative approach.
Once the plan is established, it should be communicated to all relevant parties, and necessary resources should be allocated. Regular monitoring and evaluation should be conducted to assess the effectiveness of the program and make any necessary adjustments. Continuous improvement and adaptation to changing circumstances are essential for a successful preventative maintenance program.
Overcoming Common Challenges in Implementation
Implementing a preventative maintenance program may pose various challenges. One common challenge is resistance to change, particularly from technicians who may be accustomed to reactive maintenance practices. Clear communication, training, and active involvement can help overcome this resistance and highlight the benefits of preventative maintenance.
Another challenge is the allocation of sufficient resources, including time, funding, and personnel. Organizations should ensure that technicians have the necessary tools, equipment, and training to carry out their maintenance tasks effectively. Additionally, management's commitment and support are crucial for maintaining momentum and sustaining the program in the long term.
The Future of Preventative Maintenance in the Wastewater Industry
Emerging Trends and Innovations
The wastewater industry is constantly evolving, with emerging trends and innovations shaping the future of preventative maintenance. One significant trend is the integration of artificial intelligence (AI) and machine learning algorithms into maintenance practices. AI-powered systems can analyze vast amounts of data, identify patterns, and predict equipment failures with greater accuracy.
Remote monitoring and diagnostics are also gaining prominence, allowing technicians to assess equipment performance and health without physically being present. The use of drones for inspection purposes and robotics for routine maintenance tasks is increasing efficiency and reducing costs.
Sustainability and Environmental Impact
As sustainability continues to be a global focus, preventative maintenance plays a crucial role in minimizing the environmental impact of the wastewater industry. By ensuring proper equipment functioning and reducing the likelihood of spills, leaks, or contamination, preventative maintenance contributes to a cleaner and more sustainable environment.
Organizations are increasingly exploring renewable energy sources, energy-efficient technologies, and water recycling systems. Preventative maintenance will play a pivotal role in optimizing the performance of these sustainable solutions and maximizing their long-term benefits.
By embracing emerging trends and prioritizing sustainability, the wastewater industry can elevate the effectiveness and impact of preventative maintenance.
Conclusion
In conclusion, preventative maintenance is the key to ensuring the reliability, efficiency, and safety of equipment in the wastewater industry. By prioritizing regular equipment inspections, scheduled servicing, and the adoption of predictive maintenance techniques, technicians can proactively address issues and prevent costly breakdowns. The use of modern tools and technologies, such as maintenance software and IoT devices, enhances the effectiveness of preventative maintenance programs. Safety considerations and continuous training empower technicians to carry out maintenance activities while safeguarding themselves and the environment. By conducting a cost-benefit analysis, organizations can appreciate the long-term benefits of preventative maintenance and make informed decisions. By following the steps outlined in this guide and embracing future trends and innovations, the wastewater industry can pave the way for a sustainable and efficient maintenance approach, ensuring the smooth operation of wastewater treatment systems and protecting the environment.