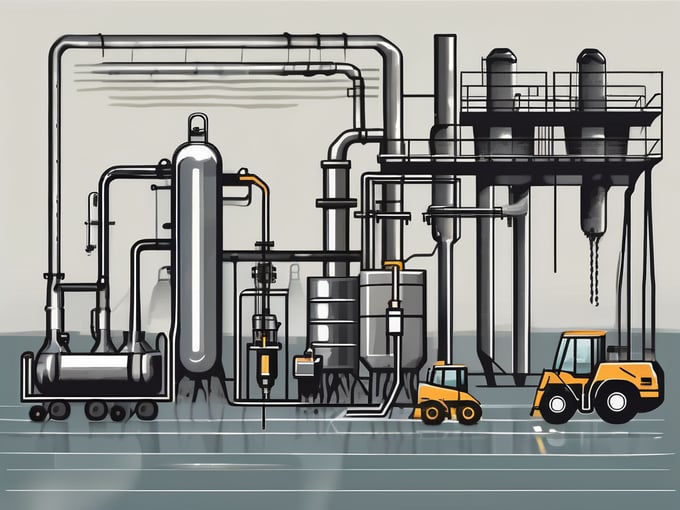
Guide to Preventative Maintenance for Safety Officers in the Sludge Management Industry
As a safety officer in the sludge management industry, it is crucial to understand the importance of preventative maintenance. This guide aims to provide you with a comprehensive understanding of preventative maintenance, its key elements, the process of implementing a preventative maintenance plan, evaluating the effectiveness of the program, challenges faced, and solutions to overcome them. We will also touch upon the future of preventative maintenance in the sludge management industry, including technological advancements and sustainability.
Understanding the Importance of Preventative Maintenance
Preventative maintenance plays a vital role in ensuring the smooth operation of sludge management facilities while ensuring the safety of personnel and protecting the environment. By carrying out regular inspections, calibrations, and maintenance tasks, safety officers can identify and address potential equipment failures and safety hazards before they escalate.
Sludge management facilities are complex systems that require careful monitoring and maintenance to function optimally. These facilities are responsible for handling and treating wastewater sludge, which contains various contaminants and pollutants. Without proper preventative maintenance, these facilities can experience equipment malfunctions, leaks, and other issues that can lead to environmental contamination and pose risks to human health.
One of the key aspects of preventative maintenance in sludge management is conducting routine inspections. Safety officers meticulously examine the equipment, pipelines, and storage tanks to identify any signs of wear and tear, corrosion, or leaks. They also check the functioning of valves, pumps, and other critical components to ensure they are operating within the specified parameters.
Defining Preventative Maintenance in Sludge Management
In the context of sludge management, preventative maintenance refers to a proactive approach aimed at preventing equipment failures, minimizing operational downtime, and maximizing equipment lifespan. It involves routine inspections, testing, lubrication, adjustments, and repairs performed according to manufacturer's recommendations, industry standards, and regulatory requirements.
Regular testing is another essential aspect of preventative maintenance in sludge management. Safety officers conduct various tests to assess the quality of the sludge, such as pH levels, chemical composition, and biological activity. These tests help in determining if any adjustments or treatments are required to maintain the desired sludge characteristics and prevent any adverse effects on the environment.
Lubrication is also a critical part of preventative maintenance. Safety officers ensure that all moving parts, such as pumps, motors, and conveyors, are properly lubricated to minimize friction and reduce the risk of premature wear and tear. They follow the manufacturer's guidelines to select the appropriate lubricants and schedule regular lubrication tasks to keep the equipment running smoothly.
The Role of Safety Officers in Preventative Maintenance
Safety officers play a crucial role in ensuring the effective implementation of preventative maintenance programs. They are responsible for developing, implementing, and managing the maintenance plan, conducting inspections, coordinating repairs, and ensuring compliance with safety regulations. Through their expertise, safety officers help identify potential risks, implement control measures, and continuously improve maintenance practices.
Effective preventative maintenance requires a comprehensive understanding of the sludge management facility's operations and the associated risks. Safety officers undergo specialized training to gain the necessary knowledge and skills to carry out their responsibilities effectively. They stay updated with the latest industry standards, technological advancements, and regulatory requirements to ensure that the maintenance practices align with the best practices and comply with the applicable regulations.
Furthermore, safety officers collaborate with other stakeholders, such as engineers, operators, and environmental experts, to develop a holistic approach to preventative maintenance. They actively participate in risk assessments, incident investigations, and improvement initiatives to enhance the overall safety and reliability of the sludge management facility.
Key Elements of a Preventative Maintenance Program
A preventative maintenance program is essential for ensuring the longevity and optimal performance of equipment. By implementing regular inspections, equipment maintenance, safety protocols, and procedures, organizations can minimize downtime, reduce repair costs, and enhance workplace safety.
Equipment Inspection and Maintenance
An essential aspect of preventative maintenance is performing regular equipment inspections to assess its condition and identify any signs of wear, damage, or malfunction. Safety officers should utilize checklists and standardized procedures to ensure consistent inspections and maintain accurate records.
During inspections, safety officers should thoroughly examine all components of the equipment, including mechanical, electrical, and structural parts. They should pay close attention to any signs of corrosion, leaks, loose connections, or abnormal noises. In addition, they should inspect the equipment's safety features, such as emergency stop buttons and safety guards, to ensure they are functioning properly.
Regular cleaning is also crucial to prevent the buildup of dirt, dust, and debris, which can affect the equipment's performance. Safety officers should use appropriate cleaning agents and techniques to remove contaminants without causing damage. Lubrication of moving parts should be performed according to the manufacturer's recommendations to reduce friction and prevent premature wear.
Calibration is another important aspect of equipment maintenance. Safety officers should periodically calibrate the equipment to ensure accurate measurements and reliable performance. This involves comparing the equipment's readings to a known standard and making any necessary adjustments.
Safety Protocols and Procedures
Integrating safety protocols and procedures into the preventative maintenance program is crucial to safeguarding personnel and mitigating risks. Safety officers should establish clear guidelines for lockout/tagout procedures, personal protective equipment (PPE) requirements, and safe work practices.
Lockout/tagout procedures are used to control hazardous energy sources during equipment maintenance or repair. Safety officers should develop detailed procedures that outline the steps for isolating and de-energizing the equipment, as well as the proper use of lockout/tagout devices. These procedures should be communicated to all personnel involved in maintenance activities.
Personal protective equipment (PPE) requirements should be clearly defined based on the potential hazards associated with the equipment and maintenance tasks. Safety officers should identify the appropriate PPE, such as safety glasses, gloves, and protective clothing, and ensure that it is readily available to personnel. Regular inspections of PPE should also be conducted to ensure its effectiveness and replace any damaged or worn-out items.
Safe work practices should be emphasized to prevent accidents and injuries during equipment maintenance. Safety officers should provide training sessions to educate personnel on the proper techniques for handling equipment, using tools, and following established procedures. Regular refresher training should be conducted to reinforce these practices and address any new safety concerns.
By integrating safety protocols and procedures into the preventative maintenance program, organizations can create a culture of safety and ensure that personnel are well-prepared to handle maintenance tasks in a secure manner.
The Process of Implementing a Preventative Maintenance Plan
Implementing a preventative maintenance plan is a crucial step in ensuring the smooth operation and longevity of equipment and facilities. By proactively addressing potential issues and conducting regular inspections and repairs, organizations can minimize downtime, reduce costs, and enhance safety. Let's explore the various stages involved in the implementation of a preventative maintenance plan.
Planning and Preparation
Before diving into the implementation process, it is essential to conduct a comprehensive assessment of the equipment and facility. This assessment helps identify critical assets, determine maintenance intervals, and establish priorities. Safety officers, in collaboration with maintenance teams, should thoroughly inspect each piece of equipment, noting any signs of wear and tear, potential vulnerabilities, or areas that require immediate attention.
Once the assessment is complete, the next step is to develop a detailed work schedule. This schedule should outline the frequency and duration of maintenance activities, ensuring that all equipment receives the necessary attention. Assigning responsibilities to qualified individuals is also crucial to ensure that each task is performed efficiently and effectively.
Furthermore, proper planning involves ensuring the availability of necessary resources, such as spare parts and tools. Safety officers should work closely with procurement teams to ensure that all required materials are in stock and easily accessible. This proactive approach eliminates delays and minimizes disruptions during the maintenance process.
Training and Education for Safety Officers
Effective implementation of a preventative maintenance plan relies heavily on the knowledge and skills of safety officers. These individuals play a critical role in performing inspections, conducting repairs, and adhering to established protocols. Therefore, providing them with adequate training and education is of utmost importance.
Training programs should cover a wide range of topics, including equipment-specific maintenance procedures, safety protocols, and troubleshooting techniques. Safety officers should be well-versed in identifying potential hazards, understanding the intricacies of each piece of equipment, and following industry best practices.
Continuous professional development is also essential for safety officers to stay up-to-date with the latest advancements in maintenance practices. Attending workshops, conferences, and seminars can provide valuable insights into emerging technologies and innovative approaches to preventative maintenance. By constantly expanding their knowledge base, safety officers can optimize the effectiveness of the maintenance program and adapt to evolving industry standards.
In conclusion, the process of implementing a preventative maintenance plan involves careful planning, thorough preparation, and continuous education. By investing time and resources into these stages, organizations can ensure the seamless operation of their equipment and facilities, ultimately leading to increased productivity, reduced costs, and enhanced safety.
Evaluating the Effectiveness of a Preventative Maintenance Program
A well-executed preventative maintenance program is crucial for ensuring the smooth operation and longevity of equipment and machinery. By proactively addressing potential issues before they escalate into major problems, organizations can reduce downtime, improve safety, and save on costly repairs. However, simply implementing a preventative maintenance program is not enough; it is essential to regularly evaluate its effectiveness and make necessary adjustments to optimize its performance.
Regular Audits and Reviews
Conducting regular audits and reviews of the preventative maintenance program allows safety officers to assess its effectiveness and identify areas for improvement. These audits can involve a comprehensive evaluation of various aspects, including adherence to maintenance schedules, analysis of equipment performance data, and review of incident reports. By scrutinizing these key areas, safety officers can gain valuable insights into the program's strengths and weaknesses.
For instance, evaluating the adherence to maintenance schedules can reveal whether tasks are being completed on time and if any bottlenecks or delays are occurring. Analyzing equipment performance data can provide a deeper understanding of how well the maintenance program is preventing breakdowns and reducing the risk of equipment failure. Reviewing incident reports can shed light on any recurring issues or patterns that need to be addressed.
Based on the audit findings, safety officers can make necessary adjustments to the maintenance plan and update procedures as needed. For example, if the audit reveals that certain maintenance tasks are consistently being overlooked or delayed, safety officers can revise the schedule to ensure timely completion. If equipment performance data indicates a specific component is prone to failure, safety officers can modify the maintenance plan to include more frequent inspections or replacements.
Continuous Improvement in Preventative Maintenance
Preventative maintenance programs should not remain static but evolve over time. Safety officers should actively seek ways to improve maintenance practices, staying abreast of technological advancements and industry best practices. By embracing a culture of continuous improvement, safety officers can enhance the efficiency and effectiveness of the maintenance program.
One way to drive continuous improvement is by implementing condition monitoring technologies. These technologies enable real-time monitoring of equipment performance, allowing safety officers to detect early warning signs of potential issues. By leveraging advanced sensors and data analytics, safety officers can identify anomalies or deviations from normal operating conditions, enabling them to take proactive measures before a breakdown occurs.
Another strategy for continuous improvement is adopting predictive maintenance strategies. Rather than relying solely on predetermined maintenance schedules, predictive maintenance uses data analysis and machine learning algorithms to predict when equipment is likely to fail. By identifying potential failures in advance, safety officers can plan maintenance activities more efficiently, minimizing downtime and reducing costs associated with reactive repairs.
Furthermore, leveraging data analytics can provide valuable insights into equipment performance trends, enabling safety officers to optimize maintenance intervals and identify opportunities for process optimization. By analyzing historical data, safety officers can identify patterns and correlations between maintenance activities and equipment performance, allowing them to fine-tune the maintenance program for maximum efficiency.
In conclusion, evaluating the effectiveness of a preventative maintenance program is crucial for its success. Regular audits and reviews provide valuable feedback and enable safety officers to make necessary adjustments. By embracing a culture of continuous improvement and leveraging advanced technologies, organizations can enhance the efficiency and effectiveness of their maintenance programs, ultimately leading to improved equipment reliability, reduced downtime, and increased operational efficiency.
Challenges and Solutions in Preventative Maintenance
Preventative maintenance programs play a crucial role in ensuring the safety and efficiency of industrial operations. However, implementing these programs can be a challenging task for safety officers. They often face various obstacles that require innovative solutions and effective strategies.
Common Obstacles in Implementing Preventative Maintenance
One of the primary challenges faced by safety officers is limited budgets. Allocating sufficient funds for preventative maintenance activities can be a daunting task, especially when organizations are trying to balance multiple priorities. Inadequate resources also pose a significant obstacle, as safety officers may struggle to find skilled personnel and access the necessary tools and equipment.
Resistance to change is another common obstacle encountered during the implementation of preventative maintenance programs. Employees and stakeholders may be resistant to new processes and procedures, fearing disruptions to their daily routines. Overcoming this resistance requires effective communication and engagement, emphasizing the benefits of preventative maintenance in terms of increased safety, reduced downtime, and improved overall performance.
Additionally, a lack of management support can hinder the successful implementation of preventative maintenance programs. Without the backing of top-level management, safety officers may struggle to secure the necessary resources and support from other departments. Building a strong business case and demonstrating the long-term benefits of preventative maintenance, such as cost savings, safety improvements, and regulatory compliance, can help garner management support.
Innovative Solutions for Effective Maintenance
Advancements in technology have opened up new possibilities for enhancing the effectiveness of preventative maintenance. Safety officers can leverage innovative solutions to streamline their maintenance workflows and improve overall efficiency.
Asset management software systems have become invaluable tools for safety officers. These systems enable the centralized management of maintenance schedules, work orders, and equipment data. By utilizing these software systems, safety officers can optimize their maintenance activities, ensuring that critical assets receive the necessary attention while minimizing downtime and maximizing productivity.
Remote monitoring and diagnostics have also revolutionized preventative maintenance practices. With the ability to remotely monitor equipment and collect real-time data, safety officers can detect potential issues before they escalate into costly failures. This proactive approach allows for timely interventions, reducing downtime and preventing safety hazards.
The Internet of Things (IoT) sensors have emerged as game-changers in the field of preventative maintenance. These sensors can be attached to equipment and machinery, collecting data on various parameters such as temperature, vibration, and energy consumption. By analyzing this data, safety officers can identify patterns and trends, enabling them to predict and prevent failures before they occur.
Predictive analytics is another powerful tool that safety officers can utilize to enhance preventative maintenance. By analyzing historical data and applying advanced algorithms, safety officers can gain insights into the performance and condition of equipment. This data-driven approach allows for optimized maintenance planning, reducing costs, and improving overall reliability.
In conclusion, while implementing preventative maintenance programs may present challenges, safety officers can overcome these obstacles by employing innovative solutions and effective strategies. By addressing limited budgets, inadequate resources, resistance to change, and a lack of management support, safety officers can establish successful preventative maintenance practices. Leveraging asset management software systems, remote monitoring and diagnostics, IoT sensors, and predictive analytics can significantly enhance the effectiveness of maintenance activities, leading to improved safety, reliability, and efficiency.
The Future of Preventative Maintenance in Sludge Management
Technological Advancements and Their Impact
The sludge management industry is witnessing rapid technological advancements that offer immense potential for enhancing preventative maintenance practices. Robotics, artificial intelligence, and machine learning algorithms enable autonomous inspections and predictive maintenance. These technologies can revolutionize the industry by improving safety, optimizing maintenance schedules, and reducing costs associated with reactive repairs.
Sustainability and Preventative Maintenance
In the face of growing environmental concerns, sustainability has become a crucial aspect of sludge management. Preventative maintenance plays a vital role in reducing the ecological impact by minimizing equipment failures, leaks, and spills that can harm the environment. Safety officers should prioritize sustainable practices by integrating energy-efficient equipment, implementing waste management strategies, and promoting a culture of environmental responsibility within the organization.
By following this ultimate guide to preventative maintenance for safety officers in the sludge management industry, you can enhance the reliability, safety, and environmental performance of your facilities. Through proactive and diligent maintenance practices, safety officers become integral in safeguarding personnel, protecting the environment, and maximizing operational efficiency.