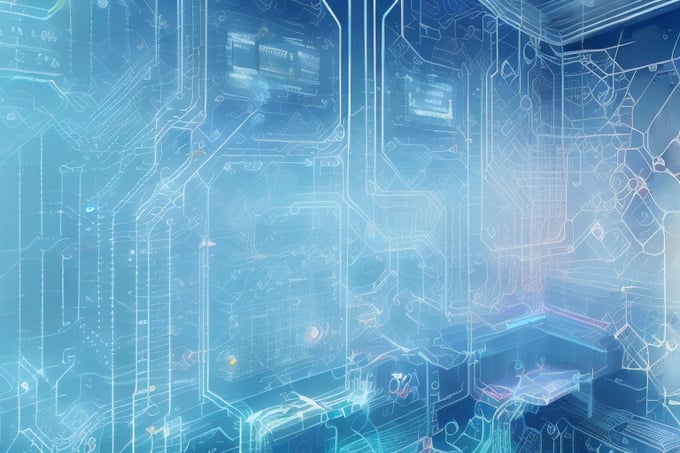
In the ever-evolving landscape of industrial control systems, SCADA (Supervisory Control and Data Acquisition) stands as a crucial pillar. This sophisticated technology has a rich history and continues to shape the way industries operate today. In this article, we will explore the past, present, and future of SCADA, examining its definition, importance, evolution, modern applications, challenges, and impact on different sectors.
Understanding SCADA: An Introduction
Before diving into the intricate details, it is essential to have a clear understanding of what SCADA is. SCADA, which stands for Supervisory Control and Data Acquisition, refers to a system that combines hardware and software components to provide real-time monitoring, control, and data acquisition capabilities in industrial environments. Through its centralized architecture, SCADA enables operators to remotely manage and supervise critical processes, ensuring efficient and secure operations.
SCADA systems have revolutionized the way industries operate by providing a comprehensive solution for monitoring and controlling various industrial processes. These systems are designed to collect data from sensors, remote terminal units (RTUs), and programmable logic controllers (PLCs), and then transmit this data to a central control unit. The central control unit acts as the brain of the SCADA system, processing the data and presenting it to operators in a user-friendly interface.
Defining SCADA
SCADA systems encompass various components, each playing a crucial role in the overall functionality of the system. Sensors, for instance, are responsible for collecting data on parameters such as temperature, pressure, flow rate, and level. These sensors are strategically placed throughout the industrial facility to ensure comprehensive data collection.
Remote terminal units (RTUs) serve as the link between the sensors and the central control unit. They are responsible for collecting data from the sensors and transmitting it to the central control unit via communication infrastructure. RTUs also play a vital role in executing control commands, allowing operators to remotely control industrial processes.
Programmable logic controllers (PLCs) are another integral component of SCADA systems. These devices are responsible for executing control commands based on the data received from the sensors and RTUs. PLCs are highly programmable, allowing operators to define complex control algorithms and logic to ensure precise control over industrial processes.
The Importance of SCADA in Industrial Control Systems
SCADA plays a pivotal role in enhancing the functionality, safety, and efficiency of industrial control systems. By providing real-time data on diverse industrial processes, SCADA empowers operators to monitor parameters, detect trends, and identify potential issues before they escalate. This proactive approach minimizes downtime, optimizes resource allocation, and ultimately saves costs for industries.
One of the key benefits of SCADA is its ability to provide operators with a holistic view of the industrial processes. The centralized control unit collects data from various sensors and presents it in a user-friendly interface, allowing operators to monitor multiple processes simultaneously. This real-time monitoring capability enables operators to make informed decisions and take prompt actions to address any anomalies or emergencies.
Furthermore, SCADA systems often incorporate advanced data analysis and visualization tools, enabling operators to analyze historical data and identify patterns or trends. This analysis can help operators optimize industrial processes, improve efficiency, and reduce energy consumption. By leveraging the power of data, SCADA systems enable industries to stay competitive in today's rapidly evolving market.
In conclusion, SCADA systems are a critical component of modern industrial control systems. They provide real-time monitoring, control, and data acquisition capabilities, allowing operators to remotely manage and supervise critical processes. With its ability to collect and analyze data, SCADA enhances the functionality, safety, and efficiency of industrial operations, ultimately leading to cost savings and improved competitiveness for industries.
Tracing the Roots: The History of SCADA
To truly appreciate the significance of SCADA, we must delve into its intriguing history. The roots of SCADA can be traced back to the early 1960s when oil and gas companies sought effective methods to remotely monitor and control their pipelines. This need paved the way for the emergence of rudimentary SCADA systems, marking the birth of a major technological breakthrough.
During this time, the oil and gas industry faced numerous challenges in managing their vast pipeline networks. The traditional methods of manual monitoring and control were not only time-consuming but also prone to human errors. The need for a more efficient and reliable solution became evident.
In its nascent stages, SCADA primarily relied on telegraph lines to transmit data from remote sites to the central control unit. This allowed operators to monitor critical parameters such as temperature, pressure, and flow rates, revolutionizing the way pipeline operations were managed. With the ability to remotely adjust settings and receive real-time updates, companies experienced significant improvements in operational efficiency and safety.
The introduction of SCADA systems brought about a paradigm shift in the oil and gas industry. It eliminated the need for manual intervention at remote sites, reducing the risk of accidents and improving overall productivity. The ability to monitor and control pipelines from a centralized location provided operators with unprecedented control and visibility.
The Early Beginnings of SCADA
As SCADA systems gained traction, further advancements were made to enhance their capabilities. The 1970s witnessed the advent of computer-based technologies, which saw the replacement of telegraph lines with more advanced communication protocols such as Modbus and DNP3. These protocols offered enhanced data transmission capabilities, thereby enabling more complex monitoring and control functionalities.
With the introduction of computer-based technologies, SCADA systems became more sophisticated and versatile. Operators could now monitor a wide range of parameters, including not only temperature and pressure but also fluid levels, valve positions, and even environmental conditions. This expanded scope of monitoring allowed for more comprehensive and proactive decision-making, leading to improved operational efficiency and cost savings.
Moreover, the introduction of Human-Machine Interfaces (HMIs) provided operators with user-friendly graphical displays, making data interpretation more intuitive and accessible. These interfaces allowed operators to visualize the pipeline network in real-time, enabling them to identify potential issues and take immediate corrective actions. The combination of advanced communication protocols and intuitive HMIs marked a significant milestone in the evolution of SCADA technology.
As SCADA systems continued to evolve, they found applications beyond the oil and gas industry. Various sectors, including water and wastewater management, power generation, and manufacturing, recognized the potential of SCADA in improving operational efficiency and safety. The versatility and adaptability of SCADA systems made them indispensable tools in managing critical infrastructure and ensuring smooth operations.
The Current State of SCADA
Today, SCADA continues to evolve and adapt to the ever-changing demands of the industrial landscape. Its applications span across diverse sectors, each harnessing the power of SCADA to optimize their unique processes and operations.
Modern Applications of SCADA
The applications of SCADA have expanded beyond the traditional realms of oil and gas. Industries such as water distribution, power generation, manufacturing, and transportation now heavily rely on SCADA systems to ensure uninterrupted operations. SCADA enables water treatment plants to monitor water quality, power plants to optimize energy production, factories to maintain efficient production lines, and transportation networks to ensure smooth traffic flow.
Challenges and Limitations of Current SCADA Systems
Despite its numerous advantages, SCADA is not without its challenges. The increasing interconnectedness of systems and the rise of the Internet of Things (IoT) have exposed SCADA systems to a myriad of cybersecurity threats. Securing SCADA networks and protecting critical infrastructure from malicious attacks has become a paramount concern for industries and cybersecurity professionals. Additionally, the growing complexity of industrial systems presents a challenge in terms of data management and analysis, requiring innovative approaches and scalable solutions.
Looking Ahead: The Future of SCADA
As we venture into the future, several trends are poised to shape the trajectory of SCADA technology.
Emerging Trends in SCADA Technology
One significant trend is the integration of artificial intelligence and machine learning capabilities into SCADA systems. By leveraging these advanced technologies, SCADA can automatically analyze vast amounts of data, identify patterns, and predict potential issues. This proactive approach enables industries to move from reactive maintenance to predictive and preventive maintenance strategies, optimizing operations and reducing downtime.
The Role of SCADA in the Era of Industry 4.0
The advent of the Fourth Industrial Revolution, commonly referred to as Industry 4.0, presents immense opportunities for SCADA. As manufacturing and industrial processes become increasingly interconnected and automated, SCADA systems will play a crucial role in orchestrating and monitoring these processes. SCADA will enable seamless integration between machines, production lines, and business operations, facilitating the efficient realization of Industry 4.0's goals.
The Impact of SCADA on Industries
SCADA's impact extends far beyond its technical capabilities. Industries across different sectors have experienced significant transformations, thanks to the integration of SCADA into their operations.
SCADA in Energy and Utilities
In the energy and utilities sector, SCADA has revolutionized the way power grids and distribution networks are managed. Utilities can now monitor energy consumption, manage load balancing, and respond swiftly to faults or outages. This enables them to optimize energy production, reduce waste, and improve the overall reliability and quality of energy services.
SCADA in Manufacturing and Production
Manufacturing and production industries have also leveraged SCADA to achieve unprecedented levels of efficiency and productivity. SCADA systems enable real-time monitoring of production lines, inventory management, and quality control. By promptly identifying bottlenecks or anomalies, manufacturers can streamline operations, reduce waste, and deliver products that meet the highest standards of quality.
Conclusion: SCADA, a Fixture of Industrial Control Systems
As we reflect on the history and future of SCADA, it is evident that this technology has become an indispensable component of modern industrial control systems. From its humble beginnings to its current applications and future prospects, SCADA continues to empower industries by enhancing operational efficiency, enabling data-driven decision-making, and ensuring the reliable and secure functioning of critical infrastructure. As we embrace the era of Industry 4.0, SCADA will play an increasingly pivotal role in shaping the industries of tomorrow.