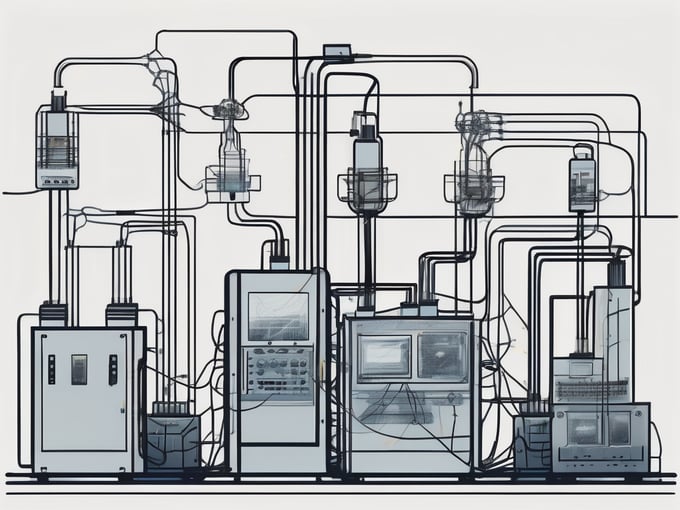
Fundamentals of Interbus
In the realm of industrial automation, the term 'protocol' carries significant weight. It is the language that devices use to communicate with each other, ensuring seamless integration and efficient operations. Among the myriad of protocols available, Interbus stands out as a robust and reliable choice. This article delves into the fundamentals of Interbus, exploring its origins, functionality, and benefits in the industrial landscape.
Understanding Interbus
Interbus, also known as Interbus-S or simply IBS, is a prominent industrial network protocol. It was developed in the late 1980s by Phoenix Contact, a German-based company renowned for its innovative solutions in the field of electrical engineering and automation. The primary goal of Interbus is to facilitate communication between industrial devices, such as sensors and actuators, and control systems like programmable logic controllers (PLCs).
Interbus operates on a master-slave configuration, where the master device (typically a PLC) initiates communication and the slave devices respond accordingly. This protocol is distinguished by its cyclic data transfer method, which enables rapid and reliable data exchange, making it an ideal choice for time-critical applications.
The Architecture of Interbus
Interbus architecture is characterized by its simplicity and flexibility. The system comprises a controller, also known as the Interbus Master, and a series of slave devices connected in a line topology. The master device manages the data exchange, while the slave devices perform specific tasks based on the received instructions.
The Interbus protocol supports a wide range of devices, including digital and analog I/O modules, drives, and visualization devices. This versatility allows for the creation of comprehensive automation systems that can cater to a variety of industrial needs.
Benefits of Using Interbus
The adoption of Interbus in industrial automation comes with a host of benefits. Its unique features and capabilities make it a preferred choice for many industries, including manufacturing, automotive, and food and beverage.
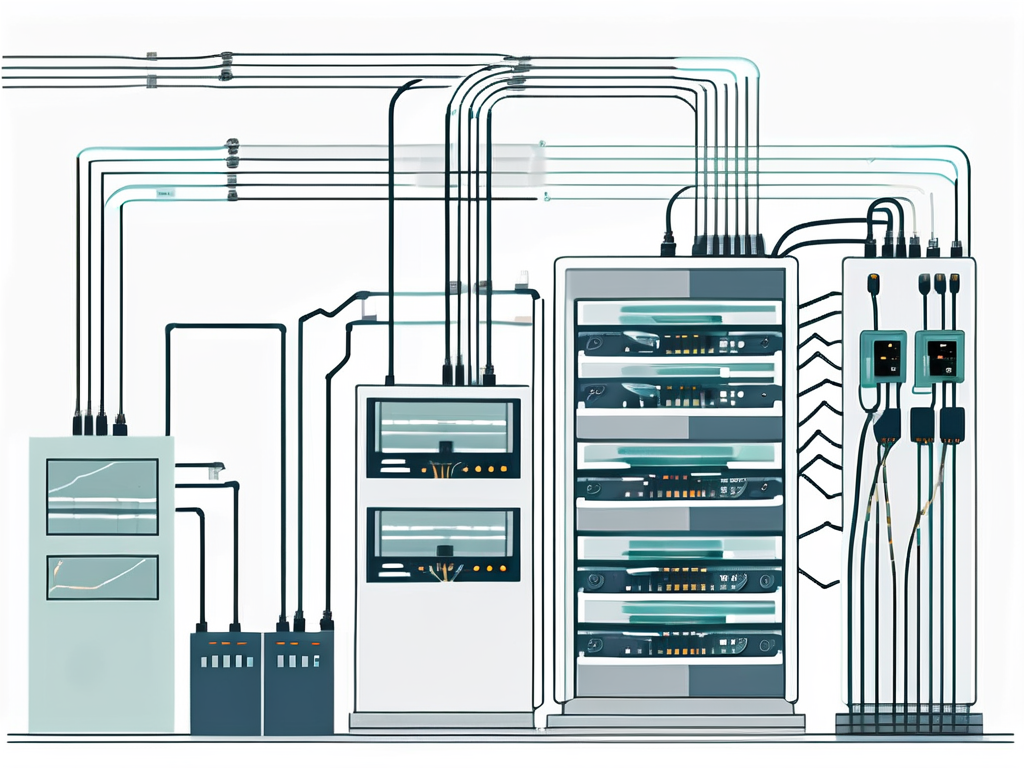
One of the key advantages of Interbus is its speed. With a data transmission rate of up to 2 Mbps, Interbus ensures quick and efficient communication between devices. This high-speed data transfer is particularly beneficial in applications where real-time control is essential.
Reliability and Robustness
Interbus is renowned for its reliability and robustness. Its cyclic data transfer method ensures consistent and error-free communication, reducing the risk of system failures. Moreover, the protocol's line topology provides inherent redundancy, further enhancing its reliability.
Additionally, Interbus devices are designed to withstand harsh industrial environments. They are resistant to electromagnetic interference and can operate in a wide range of temperatures, making them suitable for use in challenging conditions.
Easy Integration and Scalability
Interbus is designed for easy integration with existing systems. It supports a variety of fieldbus interfaces, enabling seamless connection with PLCs and other control systems. This interoperability eliminates the need for extensive hardware modifications, reducing installation time and costs.
Another notable feature of Interbus is its scalability. The protocol can support up to 512 devices per segment, allowing for system expansion without significant hardware changes. This scalability makes Interbus a future-proof solution for industrial automation.
Applications of Interbus
Thanks to its robust features and capabilities, Interbus finds application in a wide range of industries. Its high-speed data transfer and reliability make it particularly suitable for applications that require real-time control and monitoring.
In the manufacturing sector, Interbus is used to control and monitor production lines. It facilitates communication between various devices, such as sensors, actuators, and PLCs, ensuring smooth and efficient operations. Similarly, in the automotive industry, Interbus is used in assembly lines to coordinate the activities of robots and other automated systems.
Interbus in the Food and Beverage Industry
The food and beverage industry also benefits from the use of Interbus. The protocol's speed and reliability are crucial in maintaining the high standards of hygiene and quality control required in this sector. Interbus enables real-time monitoring of production processes, ensuring that any deviations from the set parameters are detected and corrected promptly.
Moreover, the easy integration and scalability of Interbus make it an ideal choice for the food and beverage industry, where production lines often need to be modified or expanded to meet changing market demands.
Conclusion
Interbus is a powerful protocol that has revolutionized industrial automation. Its speed, reliability, and flexibility have made it a preferred choice for a wide range of applications, from manufacturing to food and beverage production. As industries continue to embrace automation, the role of Interbus is set to become even more significant.
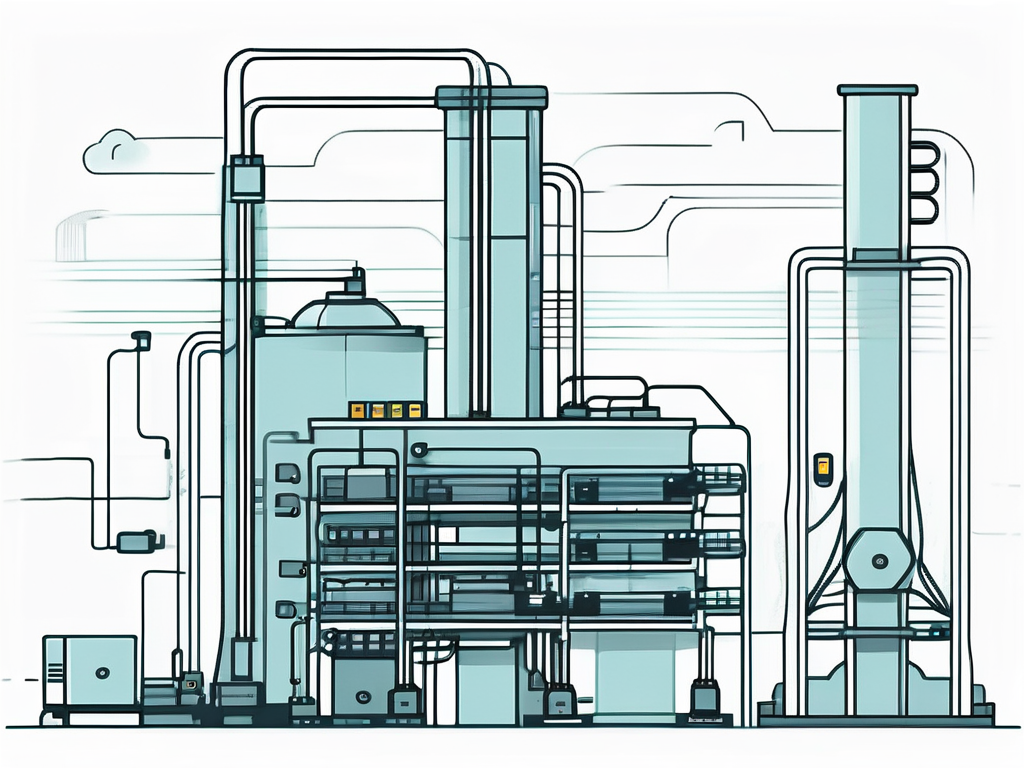
Whether you're looking to improve the efficiency of your operations, enhance system reliability, or future-proof your automation systems, Interbus offers a robust and reliable solution. So, take a step towards smarter automation with Interbus, and experience the difference it can make to your industrial processes.