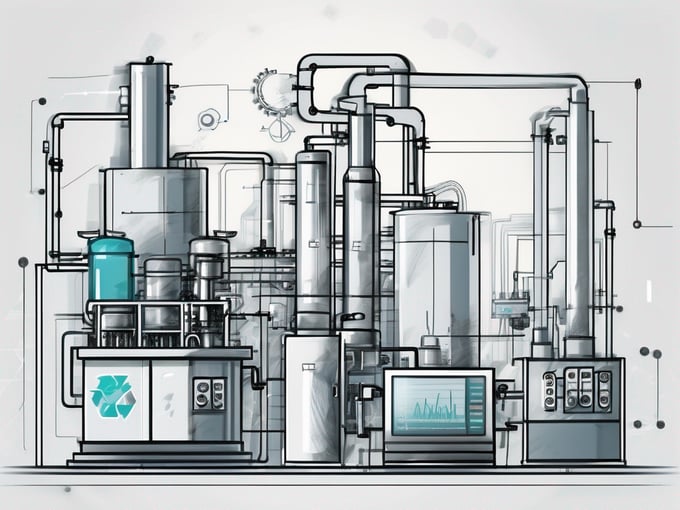
Fundamentals of OPC
In the world of industrial automation, communication protocols play a crucial role in ensuring seamless interaction between devices and systems. One such protocol that has gained significant traction over the years is OLE for Process Control (OPC). This article aims to provide a comprehensive understanding of OPC, its fundamentals, and its importance in industrial automation.
Understanding OPC
OPC, an acronym for OLE (Object Linking and Embedding) for Process Control, is a series of standards and specifications. It's a universal data exchange protocol for industrial automation, developed by the OPC Foundation. It enables reliable, real-time, and secure data transfer between different devices and applications, irrespective of the manufacturer.
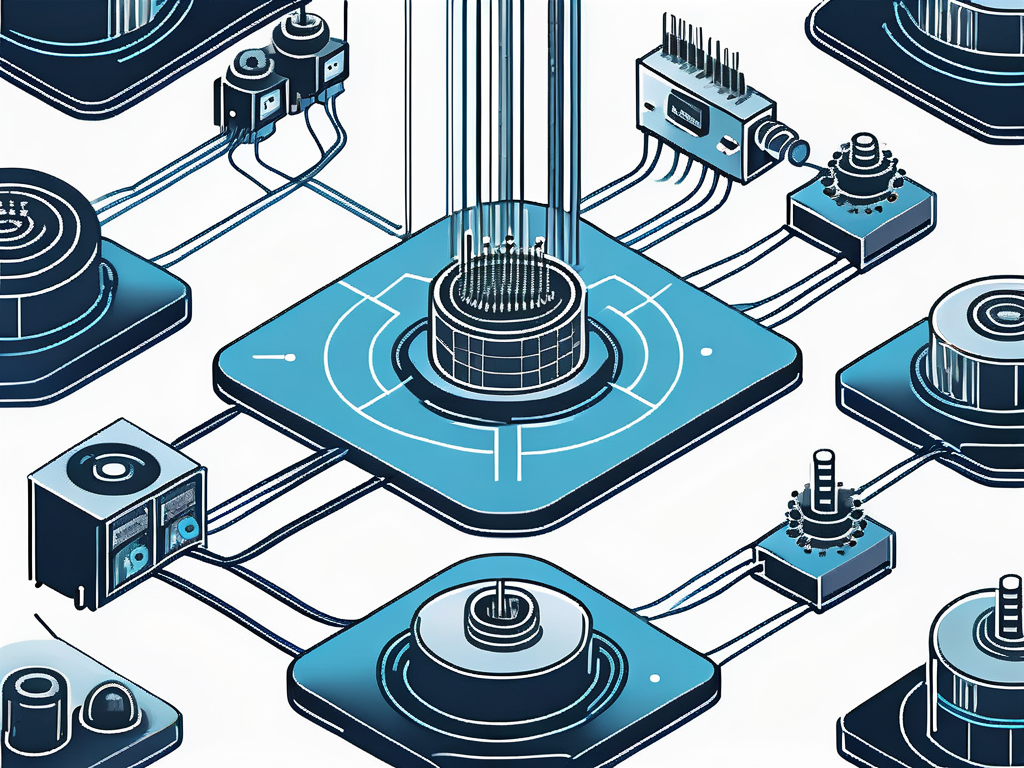
OPC protocols are designed to bridge the gap between different automation devices and software applications. They provide a common language for these components, allowing them to communicate and share data effectively. This interoperability is a significant advantage in an industrial setting, where devices from various manufacturers often need to work in harmony.
Key Components of OPC
OPC Server
The OPC Server is a software application that acts as an interface between the hardware and client applications. It translates the device-specific protocol into OPC protocol so that the data can be easily understood and accessed by the client applications.
OPC Servers are capable of communicating with a multitude of devices, including PLCs, DCS, RTUs, and more. They can handle multiple client requests simultaneously, ensuring that all client applications receive the data they need in a timely manner.
OPC Client
OPC Clients are software applications that retrieve data from the OPC Servers. They request data from the servers and use it for various purposes, such as monitoring, control, analysis, and more.
OPC Clients can be any application that needs to access the data from the devices. This includes SCADA systems, data loggers, HMIs, MES, ERP, and many more. OPC Clients communicate with OPC Servers using the standard OPC protocols, ensuring seamless data exchange.
Types of OPC Specifications
The OPC Foundation has developed several specifications to cater to different needs of industrial automation. These include OPC DA (Data Access), OPC UA (Unified Architecture), OPC HDA (Historical Data Access), OPC A&E (Alarms and Events), and more.
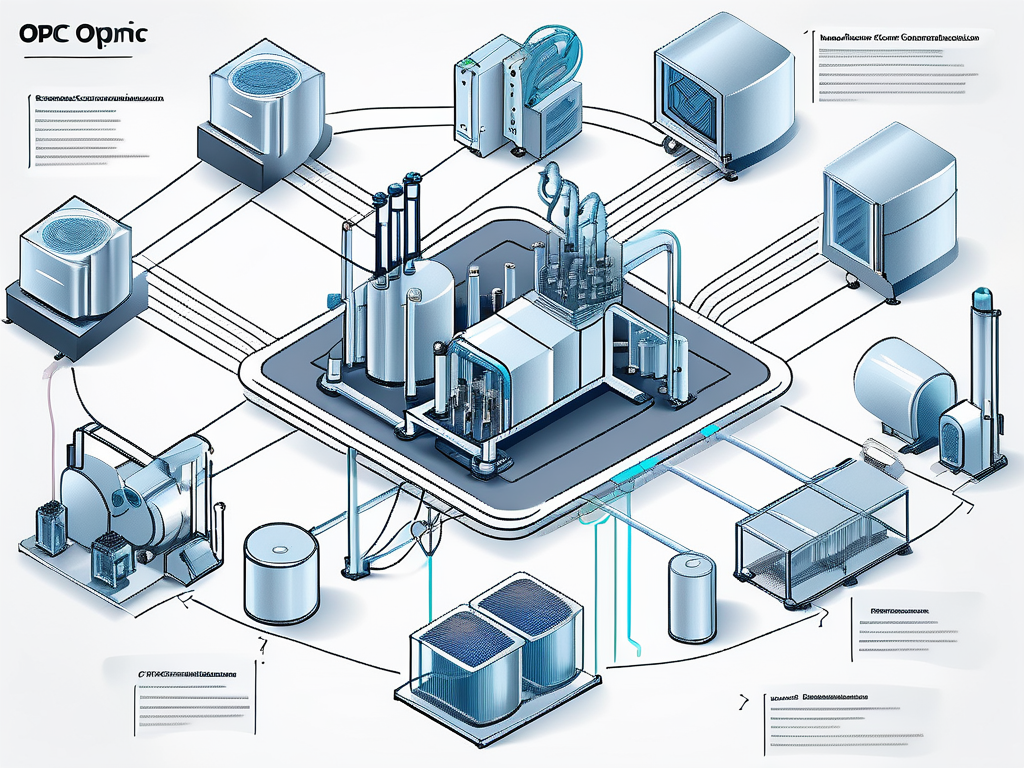
Each specification serves a different purpose and is used in different scenarios. For example, OPC DA is used for real-time data access, OPC HDA is used for accessing historical data, and OPC A&E is used for alarm and event management.
Benefits of OPC in Industrial Automation
OPC has numerous benefits in the realm of industrial automation. Its ability to provide a common language for different devices and applications has revolutionized the way industrial systems communicate.
With OPC, data exchange is no longer a complex task. It eliminates the need for custom interfaces or drivers for each device or software application. This not only reduces the complexity but also saves time and costs associated with developing and maintaining these custom solutions.
OPC also ensures reliable and secure data transfer. It provides mechanisms for error detection and recovery, ensuring that the data is accurately transferred from the devices to the client applications. Additionally, OPC supports security features such as encryption and authentication, protecting the data from unauthorized access and manipulation.
Conclusion
OPC has undoubtedly become a cornerstone in industrial automation, providing a robust, reliable, and efficient means of data exchange. Its ability to bridge the communication gap between different devices and applications has made it a preferred choice for many industries.
Understanding the fundamentals of OPC is essential for anyone involved in industrial automation. It not only helps in designing and implementing efficient systems but also aids in troubleshooting and maintaining these systems. As the world of industrial automation continues to evolve, the importance of OPC is only set to increase.