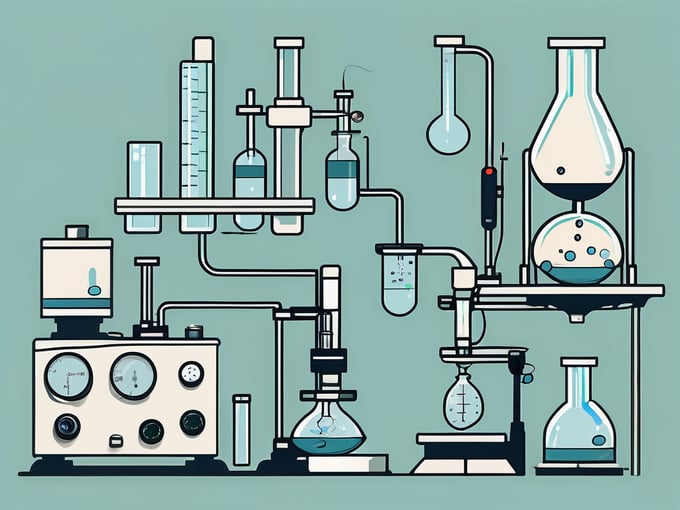
Preventative Maintenance for Lab Analysts in the Groundwater Management Industry
In the field of groundwater management, lab analysts play a crucial role in ensuring the quality and safety of our water sources. They analyze samples, perform tests, and provide vital data that helps in making informed decisions about water treatment and resource management. To fulfill this important task, lab analysts must not only possess exceptional analytical skills but also ensure that their laboratory equipment is in optimal condition at all times. This is where preventative maintenance comes into play.
Understanding the Importance of Preventative Maintenance
Preventative maintenance refers to the proactive measures taken to prevent equipment failure, minimize downtime, and extend the lifespan of laboratory instruments. In the groundwater management industry, where accuracy and reliability are paramount, preventative maintenance is not just a necessity; it is an essential component of lab operations.
Groundwater management is a critical field that involves monitoring and analyzing the quality of groundwater resources. This information is crucial for ensuring the safety and sustainability of water supplies for communities and industries. Lab analysts play a vital role in this process, as they are responsible for conducting various tests and experiments to analyze the quality, composition, and contamination levels of groundwater samples.
The Role of Lab Analysts in Groundwater Management
Lab analysts work with complex instruments and equipment to measure parameters such as pH, dissolved solids, metals, and organic compounds. These instruments are highly sensitive and require regular maintenance to ensure accurate and reliable results. Lab analysts must be proficient in maintaining and calibrating their instruments to ensure accurate and consistent readings.
Lab analysts are trained professionals who possess a deep understanding of the scientific principles behind groundwater analysis. They follow strict protocols and guidelines to ensure the integrity of their results. However, even the most skilled analysts can encounter challenges if their instruments are not properly maintained.
Key Benefits of Regular Maintenance in Labs
Regular preventative maintenance offers several key benefits to lab analysts in the groundwater management industry. Firstly, it reduces the risk of equipment failure, minimizing the chances of inaccurate readings or erroneous data. By regularly inspecting and servicing the instruments, lab analysts can identify and address any potential issues before they impact the accuracy of their results.
Furthermore, regular maintenance helps in identifying and resolving potential issues before they escalate into major problems. This proactive approach saves time and resources that would otherwise be spent on troubleshooting and repairing faulty instruments. It also minimizes the risk of unexpected breakdowns, which can lead to delays in sample analysis and reporting.
Additionally, regular maintenance extends the lifespan of lab instruments, reducing the overall cost of equipment replacement. By taking care of the instruments and ensuring their optimal performance, lab analysts can maximize the return on investment and minimize the need for frequent replacements.
Moreover, preventative maintenance contributes to a safer working environment. Well-maintained instruments are less likely to malfunction or cause accidents, ensuring the safety of lab analysts and other personnel working in the laboratory.
In conclusion, preventative maintenance is a critical aspect of lab operations in the groundwater management industry. Lab analysts must prioritize regular maintenance to ensure accurate and reliable results, minimize downtime, and extend the lifespan of their instruments. By doing so, they can contribute to the overall success and effectiveness of groundwater management efforts.
Essential Preventative Maintenance Practices
To effectively maintain lab instruments, lab analysts should incorporate the following essential preventative maintenance practices into their routine.
Lab instruments are crucial tools in scientific research and analysis, and their accuracy and reliability are of utmost importance. By implementing these preventative maintenance practices, lab analysts can ensure that their instruments perform optimally, producing precise and consistent results.
Equipment Calibration and Its Necessity
Calibration is a critical aspect of maintaining accuracy in lab measurements. Lab analysts must regularly calibrate their instruments using certified reference standards to ensure that results are precise and reliable. Calibration involves comparing the measurements obtained from the instrument to known values and making necessary adjustments to eliminate any deviations.
Regular calibration is necessary because various factors can affect the accuracy of lab instruments over time. Environmental conditions, such as temperature and humidity, can impact instrument performance. Additionally, wear and tear, aging components, and changes in the instrument's internal settings can also affect measurement accuracy.
Lab analysts should establish a calibration schedule based on the instrument's usage and manufacturer's recommendations. Calibration should be performed at predetermined intervals or whenever there are changes in environmental conditions or instrument performance. By adhering to a regular calibration routine, lab analysts can ensure that their instruments provide accurate and reliable measurements.
Regular Cleaning and Sterilization Procedures
Proper cleaning and sterilization of lab equipment play a vital role in preventing cross-contamination, ensuring the integrity of samples, and maintaining instrument performance. Lab analysts should follow manufacturer guidelines and develop standard operating procedures for cleaning, disinfecting, and decontaminating their instruments.
Regular cleaning of lab instruments is essential to remove any residue, contaminants, or debris that may accumulate during use. This includes cleaning the exterior surfaces, as well as internal components such as sample holders, cuvettes, or probes. Lab analysts should use appropriate cleaning agents and techniques to ensure thorough cleaning without damaging the instrument.
Sterilization is particularly important for instruments used in sensitive applications or when working with biological samples. Sterilization methods may include autoclaving, chemical sterilization, or heat treatment. Lab analysts should carefully follow the recommended sterilization procedures to eliminate any potential sources of contamination.
By maintaining a strict cleaning and sterilization routine, lab analysts can minimize the risk of sample contamination, ensure the accuracy of results, and prolong the lifespan of their instruments.
Routine Inspection and Maintenance of Lab Instruments
Regular visual inspections are essential for detecting signs of wear, damage, or malfunction in lab instruments. Lab analysts should inspect equipment for loose connections, leaks, corrosion, or any other abnormalities. Early detection of these issues can prevent further damage and costly repairs.
In addition to visual inspections, lab analysts should also perform routine maintenance tasks as recommended by the manufacturer. This may include lubrication of moving parts, replacement of filters or consumables, and calibration of sensors. Following the manufacturer's guidelines ensures that the instruments are maintained according to their specifications.
Lab analysts should keep detailed records of inspections, maintenance activities, and any repairs performed. These records can help identify patterns or recurring issues, allowing for proactive measures to be taken to prevent future problems.
By conducting regular inspections and maintenance, lab analysts can identify and address potential issues before they impact instrument performance or compromise the accuracy of results. This proactive approach to maintenance ensures that lab instruments remain in optimal condition, providing reliable data for scientific research and analysis.
Developing a Preventative Maintenance Schedule
Having a well-defined preventative maintenance schedule is crucial for efficient lab operations. Lab analysts should consider the following factors when developing their maintenance plan.
Regular maintenance is essential to ensure that laboratory equipment functions optimally and produces accurate results. By implementing a preventative maintenance schedule, lab analysts can minimize the risk of equipment failure, reduce downtime, and maintain the quality of their analyses.
Determining the Frequency of Maintenance Tasks
The frequency of maintenance tasks should be based on the instrument's usage, environmental conditions, and manufacturer recommendations. Lab analysts should create a schedule that allows for regular maintenance without disrupting daily operations or compromising sample analysis.
When determining the frequency of maintenance tasks, lab analysts should consider the workload of the instrument. Instruments that are used frequently or for extended periods may require more frequent maintenance to ensure optimal performance. Additionally, environmental conditions, such as temperature and humidity, can impact the performance of laboratory equipment. Instruments operating in harsh environments may require more frequent maintenance to prevent damage or malfunctions.
Manufacturer recommendations should also be taken into account when developing a maintenance schedule. Manufacturers often provide guidelines on the frequency of maintenance tasks based on their knowledge and expertise. Following these recommendations can help extend the lifespan of the equipment and maintain its accuracy.
Prioritizing Maintenance Tasks for Critical Equipment
Lab analysts must identify critical equipment that is essential for accurate and timely analysis. These instruments should be given higher priority and receive more frequent maintenance to minimize the risk of downtime or compromised results.
When prioritizing maintenance tasks, lab analysts should consider the impact of equipment failure on their laboratory operations. Critical equipment, such as mass spectrometers or high-performance liquid chromatography systems, play a crucial role in generating reliable data. Failure or malfunction of these instruments can lead to delays in analysis, compromised results, and potential financial losses.
Lab analysts should develop a maintenance plan that ensures critical equipment receives the necessary attention and care. This may include more frequent calibration, routine inspections, and proactive replacement of worn-out parts. By prioritizing maintenance tasks for critical equipment, lab analysts can minimize the risk of unexpected breakdowns and ensure uninterrupted operations.
In conclusion, developing a preventative maintenance schedule is essential for efficient lab operations. By determining the frequency of maintenance tasks and prioritizing critical equipment, lab analysts can ensure that their instruments function optimally, produce accurate results, and minimize the risk of downtime. Implementing a comprehensive maintenance plan not only extends the lifespan of laboratory equipment but also enhances the overall productivity and reliability of the laboratory.
Implementing Preventative Maintenance Procedures
Once the preventative maintenance plan is established, lab analysts must ensure proper implementation of procedures throughout the lab. This involves a series of steps and considerations to ensure the smooth execution of maintenance tasks and the overall efficiency of the lab.
Training Lab Analysts for Maintenance Tasks
Lab analysts should receive comprehensive training on maintenance procedures, best practices, and safety protocols. This training not only equips them with the necessary knowledge and skills but also instills a sense of confidence and capability in performing routine maintenance tasks. By investing in proper training, labs can ensure that their analysts are well-prepared to handle any maintenance-related challenges that may arise.
During the training process, lab analysts learn about different maintenance procedures specific to their lab equipment. They are taught how to conduct regular inspections, calibrations, and cleaning tasks to keep the equipment in optimal condition. Additionally, they are educated on the importance of adhering to safety protocols to prevent accidents and ensure a safe working environment.
Moreover, training lab analysts for maintenance tasks also helps in fostering a culture of preventative maintenance within the lab. By emphasizing the significance of regular maintenance and its positive impact on the lab's overall productivity and efficiency, analysts become more proactive in identifying potential issues and taking necessary actions to prevent equipment breakdowns.
Documentation and Record Keeping for Maintenance
Accurate and detailed documentation is essential for effective maintenance management. Lab analysts should maintain records of all maintenance activities, including calibration logs, cleaning schedules, inspection reports, and any repairs or replacements performed. This documentation serves as a reference for future maintenance and supports regulatory compliance requirements.
When it comes to calibration logs, lab analysts meticulously record the dates and results of equipment calibration. This information helps in tracking the performance of the equipment over time and ensures that it remains within the required specifications. By maintaining accurate calibration logs, labs can easily identify any deviations or trends that may indicate the need for further maintenance or adjustments.
Cleaning schedules are another crucial aspect of maintenance documentation. Lab analysts document the frequency and methods used for cleaning different equipment and work areas. This helps in maintaining a clean and hygienic environment, which is essential for accurate and reliable test results. Additionally, proper cleaning schedules contribute to the longevity of the equipment by preventing the buildup of contaminants or debris that could potentially affect its performance.
Inspection reports play a vital role in identifying potential issues before they escalate into major problems. Lab analysts document their observations during routine inspections, noting any signs of wear and tear, loose connections, or other abnormalities. This information allows for timely repairs or replacements, minimizing downtime and ensuring the uninterrupted operation of the lab.
Furthermore, any repairs or replacements performed on lab equipment should be thoroughly documented. This includes details such as the date, the nature of the issue, the actions taken, and the outcome. By keeping a record of these maintenance activities, lab analysts can track the history of each piece of equipment, identify recurring issues, and make informed decisions regarding future maintenance or equipment upgrades.
In conclusion, implementing preventative maintenance procedures in a lab requires not only the establishment of a maintenance plan but also the proper training of lab analysts and meticulous documentation of maintenance activities. By investing time and effort into these aspects, labs can ensure the longevity and optimal performance of their equipment, ultimately contributing to the success of their scientific endeavors.
Evaluating the Effectiveness of Preventative Maintenance
To continually improve maintenance practices, lab analysts should regularly evaluate the effectiveness of their preventative maintenance efforts. This evaluation process involves analyzing various key performance indicators (KPIs) and implementing continuous improvement strategies.
Key Performance Indicators for Maintenance
Monitoring key performance indicators (KPIs) is crucial in assessing the success of maintenance activities. These KPIs provide valuable insights into the overall performance and efficiency of the lab's preventative maintenance program.
One important KPI is equipment uptime, which measures the amount of time lab instruments are operational. High equipment uptime indicates that preventative maintenance efforts are effective in minimizing unplanned downtime and maximizing productivity.
Another KPI to consider is the cost of maintenance per instrument. By tracking the expenses associated with maintenance activities, lab analysts can identify any inefficiencies or areas where cost-saving measures can be implemented.
The percentage of scheduled maintenance tasks completed on time is also a significant KPI. This metric reflects the lab's ability to adhere to maintenance schedules and ensure that necessary preventive measures are taken promptly. A high percentage indicates a well-organized maintenance program that minimizes the risk of equipment failure.
By analyzing these metrics, lab analysts can identify areas of improvement and implement necessary adjustments. For example, if equipment uptime is consistently low, it may indicate a need for more frequent or comprehensive maintenance procedures. On the other hand, if the cost of maintenance per instrument is high, it may prompt the exploration of alternative maintenance strategies or the evaluation of equipment replacement options.
Continuous Improvement in Maintenance Practices
Preventative maintenance should never stagnate. Lab analysts should actively seek feedback from staff, monitor emerging technologies, and stay updated with industry best practices. Continuous improvement ensures that lab instruments remain in optimal condition and helps in adapting maintenance strategies to evolving needs.
Regularly seeking feedback from lab staff is essential in understanding their experiences and perspectives regarding the effectiveness of preventative maintenance. This feedback can provide valuable insights into potential areas for improvement or identify any recurring issues that need to be addressed.
Monitoring emerging technologies is another crucial aspect of continuous improvement. As new technologies and methodologies emerge in the field of maintenance, lab analysts should stay informed and evaluate their potential benefits. Adopting innovative maintenance practices can lead to improved efficiency, reduced costs, and enhanced equipment performance.
Keeping up with industry best practices is equally important. Attending conferences, workshops, and webinars related to maintenance can provide lab analysts with valuable knowledge and insights from industry experts. This exposure to the latest trends and techniques allows for the identification of new approaches that can be applied to the lab's preventative maintenance program.
In conclusion, regularly evaluating the effectiveness of preventative maintenance efforts is essential for continuous improvement in maintenance practices. By monitoring key performance indicators and implementing necessary adjustments, lab analysts can ensure that lab instruments remain in optimal condition, minimize downtime, and maximize productivity.
Overcoming Common Challenges in Preventative Maintenance
While preventative maintenance provides numerous benefits, lab analysts may encounter certain challenges that need to be addressed proactively.
Dealing with Equipment Downtime
Unexpected equipment downtime can be disruptive to lab operations and delay critical analyses. To mitigate this challenge, lab analysts should have backup instruments available or establish relationships with service providers for prompt repairs. Additionally, developing contingency plans for alternate testing methods can help minimize the impact of equipment malfunctions.
Ensuring Compliance with Safety Standards
Lab analysts must prioritize safety during maintenance activities. They should strictly adhere to safety protocols, use appropriate personal protective equipment, and ensure proper disposal of hazardous materials. Regular safety training and audits are essential to maintain a safe working environment.
Managing Maintenance Costs and Budgeting
Maintaining lab instruments involves costs associated with calibration standards, spare parts, service contracts, and labor. Lab analysts should collaborate with management to establish a maintenance budget and explore cost-saving initiatives such as in-house calibration or preventive maintenance agreements with vendors.
Conclusion
In summary, preventative maintenance is a critical component of lab operations for lab analysts in the groundwater management industry. By understanding the importance of preventative maintenance, implementing essential practices, developing a comprehensive maintenance schedule, and continuously evaluating effectiveness, lab analysts can optimize instrument performance, reduce downtime, and ensure accurate and reliable data. Overcoming common challenges and prioritizing safety and cost management further enhance the success of preventative maintenance efforts. With an unwavering commitment to preventative maintenance, lab analysts play a vital role in safeguarding the quality and sustainability of our groundwater resources.+