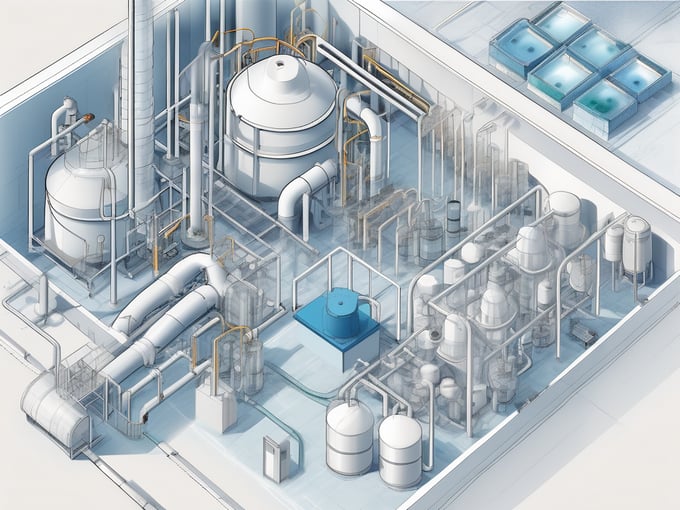
The Ultimate Guide to Alarm Management for Maintenance Technicians in the Water Industry
In the challenging environment of the water industry, alarm management plays a critical role in ensuring the safety and efficiency of operations. As a maintenance technician, it is essential to have a comprehensive understanding of alarm management principles and best practices. This ultimate guide aims to equip you with the knowledge and skills necessary to excel in alarm management in the water industry.
Understanding Alarm Management
Alarm management is a systematic approach to handling alarms in industrial systems, particularly those related to the water industry. It involves the effective management of alarm systems, including the design, implementation, and ongoing maintenance of alarm systems.
Alarm management is a critical aspect of ensuring the safe and reliable operation of water treatment plants, distribution systems, and wastewater facilities in the water industry. It plays a crucial role in identifying and responding to abnormal situations promptly, preventing potential hazards, and minimizing any adverse impacts on the environment and human health.
Effective alarm management in the water industry is closely related to regulatory compliance. Regulatory bodies, such as the Environmental Protection Agency (EPA), impose stringent requirements on alarm systems to ensure the protection of public health and the environment. By adhering to alarm management best practices, maintenance technicians contribute to meeting these regulatory standards and avoiding penalties.
The Importance of Alarm Management in the Water Industry
In the water industry, alarm management plays a crucial role in ensuring the safe and reliable operation of water treatment plants, distribution systems, and wastewater facilities. Effective alarm management helps identify and respond to abnormal situations promptly, preventing potential hazards and minimizing any adverse impacts on the environment and human health.
Furthermore, alarm management in the water industry is closely related to regulatory compliance. Regulatory bodies, such as the Environmental Protection Agency (EPA), impose stringent requirements on alarm systems to ensure the protection of public health and the environment. By adhering to alarm management best practices, maintenance technicians contribute to meeting these regulatory standards and avoiding penalties.
Alarm management also helps in optimizing operational efficiency and reducing downtime. By promptly addressing alarm conditions, maintenance technicians can minimize the duration of equipment failures and prevent cascading failures that can lead to extensive damage and costly repairs. This proactive approach to alarm management ensures that water treatment processes and distribution systems operate smoothly, providing clean and safe water to consumers.
Moreover, effective alarm management enhances the overall situational awareness of operators and maintenance technicians. By providing accurate and timely information about abnormal conditions, alarm systems enable operators to make informed decisions and take appropriate actions. This helps in preventing accidents, reducing response time, and improving the overall efficiency of the water industry.
Key Concepts in Alarm Management
Before delving into the responsibilities and duties of maintenance technicians in alarm management, it is crucial to understand some key concepts inherent to the field.
Firstly, alarm prioritization and classification. Not all alarms have the same level of criticality. Maintenance technicians should understand how to prioritize alarms based on their significance and potential consequences. This ensures that the most critical alarms receive immediate attention, enhancing the overall effectiveness of the alarm system.
Secondly, alarm response procedures. Proper alarm response procedures are vital for quick and accurate diagnosis and resolution of alarm conditions. Maintenance technicians must be trained on how to respond to alarms effectively, ensuring optimal decision-making and appropriate corrective actions.
Thirdly, alarm maintenance and testing. Alarm systems require regular maintenance and testing to ensure their reliability and accuracy. Maintenance technicians should be responsible for verifying the functionality of alarm systems, conducting periodic maintenance, and documenting any necessary adjustments or repairs.
Additionally, alarm management involves continuous improvement and optimization. Maintenance technicians should analyze alarm data, identify recurring issues, and implement corrective actions to enhance the performance of the alarm system. This iterative process helps in reducing false alarms, improving alarm response times, and enhancing the overall reliability of the system.
Furthermore, effective communication and collaboration are essential in alarm management. Maintenance technicians should actively communicate with operators, engineers, and other stakeholders to understand the operational context, share relevant information, and coordinate actions. This collaborative approach ensures a holistic understanding of alarm conditions and facilitates effective decision-making.
In conclusion, alarm management is a critical aspect of the water industry, ensuring the safe and reliable operation of water treatment plants, distribution systems, and wastewater facilities. By understanding the importance of alarm management, key concepts, and their responsibilities, maintenance technicians contribute to the overall efficiency, regulatory compliance, and safety of the water industry.
The Role of Maintenance Technicians in Alarm Management
Maintenance technicians play a vital role in ensuring the successful implementation and operation of alarm management systems. Their responsibilities encompass various aspects of alarm management, from daily operations to long-term planning and improvement.
Alarm management is a critical function within the water industry, as it helps prevent and mitigate potential risks, ensuring the safety and efficiency of operations. Maintenance technicians are at the forefront of this function, working diligently to maintain the integrity and reliability of alarm systems.
Responsibilities and Duties of Maintenance Technicians
As a maintenance technician, you are responsible for the monitoring, maintenance, and troubleshooting of alarm systems within the water industry. This includes promptly acknowledging and responding to alarms, identifying the root causes of alarm conditions, and implementing appropriate corrective measures.
However, the role of a maintenance technician goes beyond simply reacting to alarms. It involves proactive measures to prevent alarm conditions from occurring in the first place. This includes conducting routine inspections, testing equipment, and performing preventive maintenance tasks to ensure the optimal performance of alarm systems.
Additionally, maintenance technicians are responsible for documenting alarm-related information, such as alarm descriptions, time stamps, and resolutions. This documentation serves as valuable historical data for trend analysis, system optimization, and compliance reporting. By meticulously recording and analyzing alarm data, maintenance technicians can identify recurring issues, develop strategies for improvement, and enhance the overall alarm management process.
Required Skills for Effective Alarm Management
To excel in alarm management, maintenance technicians must possess a diverse skill set that combines technical expertise with critical thinking and problem-solving abilities. The following skills are essential for effective alarm management:
- Technical knowledge: A solid understanding of the water industry, including the processes, equipment, and safety protocols, is crucial in comprehending and addressing alarm conditions accurately. Maintenance technicians must stay updated with the latest advancements in technology and industry standards to effectively manage alarms.
- Analytical thinking: Maintenance technicians should possess strong analytical skills to diagnose complex alarm situations and determine the appropriate response or corrective action. They must be able to quickly assess alarm data, identify patterns, and make informed decisions to prevent potential hazards or system failures.
- Communication skills: Effective communication is vital when responding to alarms and coordinating with other team members, supervisors, or operators. Clear and concise communication helps mitigate risks and prevent misunderstandings. Maintenance technicians must be able to convey alarm information accurately and collaborate effectively with stakeholders to resolve issues promptly.
- Attention to detail: Alarm systems generate vast amounts of data. Maintaining a keen eye for detail allows technicians to identify critical patterns, anomalies, or trends that can help improve alarm management strategies. By carefully analyzing alarm data, maintenance technicians can identify potential system weaknesses, optimize alarm settings, and enhance overall system performance.
- Adaptability: The water industry continuously evolves, with new technologies, regulations, and operational challenges emerging. Maintenance technicians must remain adaptable to stay updated and effectively address evolving alarm management requirements. They should be open to learning new techniques, attending training programs, and embracing innovative solutions to enhance alarm system performance.
By possessing these essential skills and diligently fulfilling their responsibilities, maintenance technicians contribute significantly to the successful implementation and operation of alarm management systems. Their expertise and dedication ensure the safety, reliability, and efficiency of alarm systems within the water industry.
Types of Alarms in the Water Industry
In the water industry, alarms can be classified into three main categories: process alarms, equipment alarms, and safety alarms. Understanding the distinctions between these alarm types is crucial for identifying their significance and responding appropriately.
Process Alarms
Process alarms are triggered when monitored process variables deviate from their normal or desired range. These alarms typically indicate abnormal conditions or events that require immediate attention. Examples of process alarms in the water industry include high or low flow rates, abnormal pressure levels, or deviations in water quality parameters.
When a process alarm is triggered due to a high flow rate, it could indicate a potential leak in the system. This could lead to water loss and affect the overall efficiency of the water treatment process. On the other hand, a low flow rate alarm might suggest a blockage or a malfunctioning valve, which can cause disruptions in the distribution system.
Abnormal pressure levels in the water industry can be a cause for concern. High pressure can lead to pipe bursts and leaks, while low pressure can result in inadequate water supply to consumers. Process alarms for pressure deviations help operators identify and rectify these issues promptly, ensuring a stable and reliable water supply.
Deviation in water quality parameters, such as pH, turbidity, or chlorine levels, can be a sign of contamination or inadequate treatment. Process alarms for water quality deviations help maintain the integrity of the water supply by alerting operators to potential risks and enabling them to take corrective measures.
Equipment Alarms
Equipment alarms alert maintenance technicians to failures or malfunctions of critical equipment within the water treatment or distribution systems. These alarms can include pump failures, valve malfunctions, or electrical faults. Responding swiftly to equipment alarms is essential to prevent equipment damage and minimize any disruptions to water supply or treatment processes.
When a pump failure alarm is triggered, it indicates that a crucial component of the water treatment system has stopped working. This can lead to a halt in the water supply or inadequate water pressure. Maintenance technicians must quickly identify the cause of the failure and carry out necessary repairs to restore the system's functionality.
Valve malfunctions can cause issues such as water leakage, improper flow control, or even complete system shutdown. Equipment alarms for valve malfunctions help operators identify the affected valves and take immediate action to rectify the problem, ensuring smooth operation of the water distribution system.
Electrical faults in the water industry can pose significant risks, including fire hazards or damage to equipment. Equipment alarms for electrical faults help maintenance technicians identify potential dangers and take appropriate measures to prevent accidents or equipment damage.
Safety Alarms
Safety alarms are initiated in response to potential hazards within the water industry. These alarms prioritize the protection of life and the environment. Examples of safety alarms include gas leaks, fires, or abnormal levels of potentially harmful substances. Maintenance technicians must give utmost priority to safety alarms and initiate appropriate safety protocols to mitigate risks.
Gas leaks in the water industry can be extremely dangerous, as they can lead to explosions or health hazards. Safety alarms for gas leaks help operators quickly identify the affected area and evacuate personnel to ensure their safety. Additionally, prompt action can be taken to repair the leak and prevent further risks.
Fires within water treatment or distribution facilities can cause extensive damage and pose a threat to nearby communities. Safety alarms for fires help operators detect the presence of smoke or heat and activate fire suppression systems. Evacuation procedures can be implemented to ensure the safety of personnel and minimize property damage.
Abnormal levels of potentially harmful substances, such as chemicals or contaminants, can have severe consequences for public health and the environment. Safety alarms for such substances help operators identify the source of the problem and take immediate action to contain the situation. This can involve shutting down affected processes, notifying relevant authorities, and implementing appropriate measures to prevent further contamination.
By understanding the different types of alarms in the water industry and their significance, operators and maintenance technicians can effectively respond to alarms, ensuring the safety, efficiency, and reliability of water treatment and distribution systems.
Alarm Management Strategies
Developing effective alarm management strategies is crucial for maintaining the integrity and efficiency of alarm systems. The following key strategies should be implemented by maintenance technicians:
Alarm Prioritization and Classification
Before responding to alarms, maintenance technicians should be familiar with the prioritization and classification scheme implemented within their alarm system. This ensures that the most critical alarms receive immediate attention and resources, reducing the risk of missed alarms or delayed responses. Regular reviews and updates to the prioritization scheme should be conducted to align with operational changes and evolving industry standards.
Alarm Response Procedures
Alarm response procedures serve as a roadmap for maintenance technicians when an alarm condition is triggered. These procedures outline the necessary steps, such as which equipment to check, which measurements to verify, and which corrective actions to take. Following established response procedures enhances consistency and efficiency, enabling maintenance technicians to identify and resolve alarm conditions effectively.
Alarm Maintenance and Testing
Regular maintenance and testing of alarm systems are essential to ensure their optimal functionality and accuracy. Maintenance technicians should create a maintenance schedule that includes periodic checks, inspections, and calibrations. Testing the alarm system under various scenarios and conditions helps identify potential weaknesses and aids in continuous improvement efforts.
Implementing Alarm Management Systems
Implementing a robust alarm management system requires careful planning, selection, and configuration. Maintenance technicians play a vital role in this process, ensuring the successful installation and smooth operation of alarm management systems.
Choosing the Right Alarm Management System
When selecting an alarm management system, maintenance technicians should consider multiple factors, such as system compatibility with existing infrastructure, scalability, and customizability. Additionally, the system should provide adequate reporting and analysis capabilities to support continuous improvement initiatives.
System Installation and Setup
Proper installation and setup of alarm management systems are critical to their long-term success. Maintenance technicians should work closely with system providers to ensure the correct configuration, integration with existing systems, and thorough testing of the alarm management system.
Training and Education for Technicians
To utilize the alarm management system effectively, maintenance technicians must receive proper training and education. Training programs should cover topics such as system operation, alarm handling procedures, and troubleshooting techniques. Ongoing education helps maintenance technicians stay abreast of technological advancements and adapt to changing industry requirements.
Overcoming Common Alarm Management Challenges
Despite best efforts, alarm management can present various challenges. Maintenance technicians should be aware of these challenges and develop strategies to overcome them.
Alarm Overload and Nuisance Alarms
Alarm overload occurs when maintenance technicians receive an excessive number of simultaneous alarms, resulting in information overload and decreased response effectiveness. To mitigate this challenge, maintenance technicians can implement alarm suppression techniques, such as alarm prioritization and dynamic alarm filtering. By reducing nuisance alarms and focusing on critical alarms, maintenance technicians can effectively address the most relevant alarm conditions.
Alarm System Failures
Alarm system failures, including system malfunctions, false alarms, or incomplete alarm data, can hinder effective alarm management. Maintenance technicians must conduct regular system checks, software updates, and hardware inspections to detect and resolve any potential failures. Thorough testing and validation of the alarm system are essential to confirm its reliability and accuracy.
Regulatory Compliance Issues
Meeting regulatory compliance requirements is imperative in the water industry. Maintenance technicians must ensure that alarm systems comply with relevant regulations and standards, such as the International Society of Automation (ISA) standard for alarm management (ISA-18.2). Regular audits and document reviews can help identify areas of non-compliance and enable the implementation of corrective measures.
The Future of Alarm Management in the Water Industry
The water industry is continuously evolving, driven by technological advancements, sustainability concerns, and emerging challenges. Maintenance technicians must remain proactive in embracing these changes and preparing for the future.
Technological Advancements and Innovations
The ongoing developments in technologies, such as artificial intelligence, Internet of Things (IoT), and advanced data analytics, offer tremendous opportunities for improving alarm management. Maintenance technicians should stay updated on these advancements to harness their potential for optimizing alarm systems, detecting anomalies, and predicting failures.
Sustainability and Efficiency in Alarm Management
The water industry faces increasing pressure to improve sustainability and reduce resource consumption. Maintenance technicians should explore innovative approaches, such as optimizing alarm systems to minimize water loss, energy consumption, and operational costs. Incorporating sustainable practices in alarm management contributes to achieving environmental goals while maintaining operational efficiency.
Preparing for Future Challenges and Opportunities
As the water industry continues to evolve, maintenance technicians must remain adaptable and proactive in enhancing their skills and knowledge. Continuous learning, attending industry conferences, and participating in professional development programs can equip technicians with the tools and insights needed to tackle future challenges and seize opportunities.
By mastering alarm management principles and embracing technological advancements, maintenance technicians in the water industry can contribute significantly to the safety, efficiency, and sustainability of water operations. This guide has provided you with a comprehensive understanding of alarm management, your role in the process, and the potential challenges and opportunities that lie ahead. Armed with this knowledge, you are well on your way to becoming an alarm management expert in the water industry.