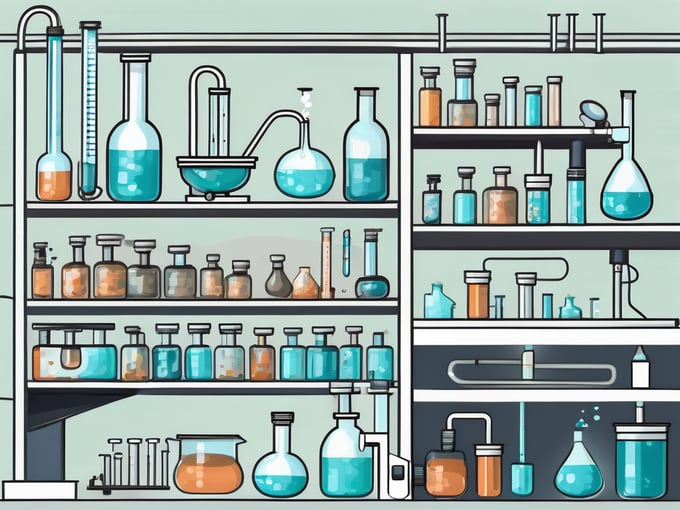
The Ultimate Guide to Preventative Maintenance for Lab Analysts in the Wastewater Industry
In the fast-paced and demanding field of wastewater analysis, lab analysts play a crucial role in ensuring the quality and safety of our water supply. With constantly evolving regulations and increasing demands for efficiency, it is essential for lab analysts to prioritize preventative maintenance to keep their equipment running smoothly and their laboratories operating at peak performance. This comprehensive guide will walk you through the key aspects of preventative maintenance in the wastewater industry, from understanding its importance to implementing effective strategies and ensuring safety. Whether you are a seasoned lab analyst or just starting your career in the field, this guide will equip you with the knowledge and tools to establish a successful preventative maintenance program.
Understanding Preventative Maintenance
The Importance of Preventative Maintenance in the Wastewater Industry
Preventative maintenance is more than just a routine task. It is a proactive approach to equipment upkeep that involves regularly scheduled inspections, cleaning, and repairs to prevent breakdowns and costly downtime. In the wastewater industry, where precision and accuracy are paramount, preventative maintenance is crucial to ensure the reliability of lab equipment and the validity of test results.
By conducting regular maintenance, lab analysts can identify and address potential issues before they escalate into major problems, minimizing the risk of equipment failure and the subsequent impact on laboratory operations. Additionally, effective preventative maintenance can extend the lifespan of equipment, reducing the need for premature replacements and reducing overall costs.
When it comes to preventative maintenance in the wastewater industry, there are several key components that work together to ensure the smooth operation of lab equipment:
Key Components of Preventative Maintenance
Preventative maintenance comprises several key components that work together to ensure the smooth operation of lab equipment:
- Inspections: Regular visual inspections of equipment are essential to identify any signs of wear and tear, leaks, or other potential issues.
During inspections, lab analysts carefully examine the equipment for any visible signs of damage or deterioration. They check for loose connections, leaks, or any abnormalities that could affect the equipment's performance. By catching these issues early on, lab analysts can take immediate action to prevent further damage and ensure the equipment's continued reliability.
- Cleaning and Lubrication: Keeping equipment clean and properly lubricated not only promotes optimal functioning but also prevents the accumulation of debris or contaminants that could compromise test results.
Cleaning and lubrication are crucial maintenance tasks that help maintain the accuracy and precision of lab equipment. Lab analysts meticulously clean the equipment, removing any dirt, residue, or contaminants that may have accumulated during use. They also ensure that all moving parts are properly lubricated to minimize friction and wear, allowing the equipment to operate smoothly and efficiently.
- Calibration: Regular calibration of instruments is necessary to maintain accuracy and precision. This involves comparing the measurements obtained by the equipment against known standards and adjusting accordingly.
Calibration is a critical aspect of preventative maintenance in the wastewater industry. Lab analysts carefully calibrate the equipment, ensuring that it provides accurate and reliable measurements. They compare the readings obtained by the equipment against known standards, making any necessary adjustments to ensure optimal performance. This meticulous calibration process guarantees the validity and integrity of the test results obtained from the equipment.
- Testing and Validation: Periodic testing and validation of equipment help ensure their continued accuracy and reliability. This may involve running control samples, performing performance checks, or verifying measurements against known samples.
Regular testing and validation are essential to verify the accuracy and reliability of lab equipment. Lab analysts conduct various tests and validations to ensure that the equipment consistently produces accurate results. This may involve running control samples to verify the equipment's performance, performing performance checks to assess its functionality, or comparing measurements obtained from known samples to confirm its precision. These rigorous testing and validation procedures guarantee the equipment's reliability and the validity of the test results it produces.
- Documentation: Proper documentation of maintenance activities, including dates, procedures, and any issues uncovered, is essential for tracking equipment performance and compliance with regulatory requirements.
Accurate and detailed documentation is a crucial aspect of preventative maintenance in the wastewater industry. Lab analysts meticulously record all maintenance activities, including the dates of inspections, cleaning, calibration, testing, and validation. They also document any issues uncovered during these activities and the steps taken to address them. This comprehensive documentation serves as a valuable reference for tracking equipment performance, identifying trends or patterns, and ensuring compliance with regulatory requirements.
Implementing a Preventative Maintenance Program
Implementing a preventative maintenance program requires careful planning and execution. By establishing an effective routine, you can ensure the longevity and optimal performance of your lab equipment. Follow these steps to create a comprehensive preventative maintenance program:
- Identify Equipment and Prioritize: Begin by creating a comprehensive inventory of all lab equipment, including its criticality to your operations. This step involves not only listing the equipment but also evaluating its importance. Consider factors such as the impact on test results, safety considerations, and frequency of use. By prioritizing equipment, you can allocate resources and time accordingly.
- Set Maintenance Intervals: Determine the appropriate maintenance intervals for each equipment category. This step involves considering various factors, such as manufacturer recommendations, regulatory requirements, and the specific needs of your lab. By establishing maintenance intervals, you can ensure that equipment is serviced regularly, reducing the risk of breakdowns and improving overall reliability.
- Create Standard Operating Procedures (SOPs): Develop detailed SOPs for each maintenance task. These procedures should outline the specific steps, tools, and safety considerations involved in performing maintenance. By having well-defined SOPs, you can ensure consistency and accuracy in maintenance activities.
- Assign Responsibilities: Clearly define roles and responsibilities for each maintenance task. It is essential to ensure that personnel are properly trained and equipped to perform their assigned duties. By assigning responsibilities, you can streamline the maintenance process and avoid confusion.
- Procure Necessary Tools and Spare Parts: Ensure that you have the required tools, lubricants, cleaning agents, and spare parts readily available to facilitate maintenance tasks. This step involves assessing the specific needs of your equipment and procuring the necessary resources. By having everything on hand, you can minimize downtime and efficiently carry out maintenance activities.
- Establish Record-Keeping System: Set up a dedicated system for documenting all maintenance activities. This system should include details such as dates, personnel involved, findings, and any corrective actions taken. By maintaining comprehensive records, you can track the history of equipment maintenance, identify patterns, and make informed decisions.
Tools and Equipment Necessary for Preventative Maintenance
Performing preventative maintenance effectively requires the use of appropriate tools and equipment. Lab analysts should have access to the following essential tools and equipment:
- Screwdrivers and wrenches: These basic hand tools are necessary for disassembling equipment and performing minor repairs or adjustments. Lab analysts should have a variety of screwdrivers and wrenches to accommodate different equipment types.
- Multimeter: A multimeter is an essential tool for measuring voltage, current, and resistance. Lab analysts can use it to troubleshoot electrical issues and ensure proper functioning of equipment. Having a reliable multimeter is crucial for accurate diagnostics.
- Cleaning agents and lubricants: Selecting the right cleaning agents and lubricants is crucial to prevent contamination and maintain optimum performance. Lab analysts should have access to a range of cleaning agents suitable for different equipment surfaces. Similarly, appropriate lubricants should be available to ensure smooth operation.
- Calibration standards: To ensure accurate calibration, lab analysts require traceable calibration standards that are regularly certified for accuracy. These standards serve as reference points for calibration and help maintain the reliability of measurement instruments.
- Personal protective equipment (PPE): Safety should always be a priority during maintenance work. Lab analysts should use proper PPE, including gloves, goggles, lab coats, and respiratory protection, as necessary. By wearing the appropriate protective equipment, analysts can minimize the risk of injury or exposure to hazardous substances.
By following these steps and utilizing the necessary tools and equipment, you can establish a preventative maintenance program that ensures the longevity and reliability of your lab equipment. Regular maintenance not only reduces the risk of equipment failure but also contributes to accurate test results and a safe working environment.
Maintenance Strategies for Lab Analysts
As lab analysts, it is crucial to implement effective maintenance strategies to ensure the smooth operation of laboratory equipment. Routine checks and maintenance tasks play a vital role in preventing equipment failures and maintaining optimal performance.
Routine Checks and Maintenance Tasks
By regularly performing the following tasks, lab analysts can proactively identify issues and take necessary actions:
- Inspecting equipment: Lab analysts should carefully inspect equipment for signs of damage, wear, or leaks. This includes examining components, connectors, and tubing to ensure they are in good condition.
- Cleaning equipment surfaces: It is essential to clean equipment surfaces regularly to remove debris and prevent the accumulation of contaminants. This helps maintain proper airflow and prevents potential issues caused by blockages.
- Checking and replacing consumables: Lab analysts should regularly check and replace consumables such as filters or cartridges as needed. This ensures that equipment functions optimally and avoids any compromise in data quality.
- Verifying safety features: Ensuring the proper functioning of safety features and emergency shut-offs is crucial for the well-being of lab personnel. Regular checks should be performed to confirm that these features are in working order.
- Calibrating instruments: Regular calibration of instruments is necessary to maintain accuracy and reliability. Lab analysts should follow established calibration procedures to ensure precise measurements and reliable results.
- Performing routine function tests: Regularly conducting function tests helps identify any issues with equipment components. This ensures that all parts are operating as intended and allows for timely repairs or replacements.
Scheduling and Planning for Regular Maintenance
Effective scheduling and planning are critical to ensure that routine maintenance tasks are performed on time and do not disrupt laboratory operations. Consider the following tips:
- Establish a regular maintenance calendar: Lab analysts should create a maintenance calendar that clearly outlines the dates and tasks to be performed. This helps in tracking maintenance activities and ensures that they are not overlooked.
- Coordinate with other lab analysts: Collaboration with other lab analysts is essential to minimize the impact of maintenance activities on ongoing projects. By coordinating schedules, lab analysts can plan maintenance during periods of lower workload or find alternative solutions to avoid disruptions.
- Prioritize and group similar tasks: To maximize efficiency and minimize downtime, lab analysts should prioritize and group similar maintenance tasks. This allows them to complete multiple tasks in one session, reducing the overall time required for maintenance.
- Create contingency plans: Lab analysts should develop contingency plans for unexpected equipment failures or urgent repair needs. This includes identifying backup equipment or alternative testing methods to ensure minimal disruption to laboratory operations.
- Regularly review and adjust the maintenance schedule: It is important to regularly review and adjust the maintenance schedule based on equipment performance and evolving needs. This ensures that maintenance activities remain effective and aligned with the changing requirements of the laboratory.
Safety Considerations in Preventative Maintenance
Safety Guidelines for Maintenance Work
Preventative maintenance involves working with potentially hazardous equipment and substances. To ensure the safety of lab analysts and promote a healthy working environment, adhere to the following safety guidelines:
- Follow all applicable safety regulations and guidelines set forth by relevant authorities.
- Provide comprehensive training to lab analysts on safety procedures and proper equipment handling.
- Encourage the use of personal protective equipment (PPE) and ensure its availability and proper maintenance.
- Prohibit unauthorized personnel from accessing maintenance areas or interfering with equipment.
- Create and enforce protocols for handling hazardous chemicals or materials, including proper storage, disposal, and spill containment measures.
When it comes to preventative maintenance, safety should always be the top priority. Lab analysts must be well-informed and educated on the potential risks and hazards associated with their work. By following the safety guidelines mentioned above, you can minimize the chances of accidents or injuries in the workplace.
One of the most important aspects of safety in preventative maintenance is compliance with safety regulations and guidelines. These regulations are put in place by relevant authorities to ensure the well-being of lab analysts and maintain a safe working environment. It is crucial to stay up-to-date with these regulations and implement them in your maintenance practices.
Comprehensive training is another key element in promoting safety during maintenance work. Lab analysts should receive thorough training on safety procedures and proper equipment handling. This training should cover topics such as identifying potential hazards, using safety equipment, and following protocols for handling hazardous materials. By equipping lab analysts with the necessary knowledge and skills, you can empower them to perform their maintenance tasks safely and efficiently.
Personal protective equipment (PPE) plays a vital role in ensuring the safety of lab analysts. It is essential to encourage the use of PPE and provide proper training on its correct usage and maintenance. Lab analysts should have access to appropriate PPE, such as gloves, goggles, or respirators, depending on the nature of the maintenance work. Regular inspections and replacements of PPE should be conducted to ensure their effectiveness and reliability.
Limiting access to maintenance areas and preventing unauthorized personnel from interfering with equipment is crucial for maintaining a safe work environment. By implementing strict access control measures, you can minimize the risk of accidents caused by unauthorized individuals who may not be aware of the potential hazards. Lab analysts should be aware of the importance of keeping maintenance areas secure and report any suspicious activities or unauthorized access immediately.
Handling hazardous chemicals or materials requires specific protocols to ensure the safety of lab analysts and prevent environmental contamination. It is essential to establish and enforce protocols for the proper storage, disposal, and spill containment of hazardous substances. Lab analysts should be trained on these protocols and provided with the necessary equipment, such as spill kits, to handle potential accidents or spills effectively.
Dealing with Potential Hazards and Risks
Lab analysts should be aware of the potential hazards and risks associated with maintenance work and take appropriate measures to mitigate them:
- Identify and assess potential hazards, such as electrical shocks, chemical exposure, or equipment malfunction.
- Develop risk mitigation strategies, including implementing lockout/tagout procedures to secure equipment before maintenance work.
- Regularly inspect safety devices, such as emergency shut-offs and alarms, to ensure their proper functioning.
- Maintain proper ventilation systems and control exposure to hazardous substances or fumes during maintenance activities.
- Establish emergency response protocols and provide training to lab analysts on handling potential emergencies or accidents.
Potential hazards and risks are inherent in maintenance work, and lab analysts must be proactive in identifying and mitigating them. Electrical shocks, chemical exposure, and equipment malfunction are just a few examples of the potential hazards that lab analysts may encounter. By conducting thorough hazard assessments, lab analysts can identify potential risks and take appropriate measures to minimize them.
One effective risk mitigation strategy is the implementation of lockout/tagout procedures. These procedures involve isolating and securing equipment before maintenance work to prevent accidental startup or release of stored energy. By following lockout/tagout procedures, lab analysts can protect themselves from potential injuries caused by unexpected equipment activation.
Regular inspections of safety devices are essential to ensure their proper functioning. Emergency shut-offs, alarms, and other safety devices should be inspected and tested regularly to identify any defects or malfunctions. Lab analysts should be trained to recognize the signs of faulty safety devices and report them immediately for prompt repairs or replacements.
Maintaining proper ventilation systems is crucial for controlling exposure to hazardous substances or fumes during maintenance activities. Adequate ventilation helps to remove potentially harmful airborne particles and ensures a safe working environment. Lab analysts should be trained on the importance of proper ventilation and the use of ventilation systems in their maintenance work.
Emergency response protocols are essential for handling potential emergencies or accidents during maintenance work. Lab analysts should be trained on these protocols, including evacuation procedures, first aid techniques, and communication channels for reporting emergencies. Regular drills and exercises should be conducted to test the effectiveness of the emergency response protocols and identify areas for improvement.
In conclusion, safety considerations in preventative maintenance are of utmost importance to protect lab analysts and maintain a healthy working environment. By following the safety guidelines and dealing with potential hazards and risks, you can ensure the well-being of your lab analysts and promote a culture of safety in your maintenance practices.
Evaluating the Effectiveness of Your Maintenance Program
Key Performance Indicators for Maintenance Programs
To ensure the ongoing effectiveness of your preventative maintenance program, monitor key performance indicators (KPIs) that reflect its impact on laboratory operations:
- Mean Time Between Failures (MTBF): This metric measures the average time elapsed between equipment failures, indicating the reliability of your maintenance program.
- Mean Time to Repair (MTTR): MTTR measures the average time required to restore equipment functionality after a failure. Lower MTTR values indicate efficient troubleshooting and repair processes.
- Equipment Availability: This KPI reflects the percentage of time equipment is operational, giving insight into the effectiveness of your maintenance efforts in minimizing downtime.
- Cost of Maintenance: Analyzing the costs associated with preventative maintenance, including labor, spare parts, and outsourced services, helps evaluate its overall efficiency.
Regular Review and Improvement of Maintenance Strategies
Maintenance strategies should not be set in stone. Regularly reviewing and improving your preventative maintenance program is key to staying ahead of emerging challenges and optimizing your laboratory operations:
- Conduct periodic audits of maintenance activities to identify areas for improvement or potential gaps in compliance.
- Solicit feedback from lab analysts regarding the effectiveness of various maintenance tasks and procedures.
- Stay updated with industry best practices, technological advancements, and regulatory changes, and adapt your maintenance strategies accordingly.
- Investigate equipment failures or recurring issues to identify root causes and implement preventive measures.
- Encourage a culture of continuous improvement and learning within your team, fostering innovation and proactivity in maintenance activities.
This ultimate guide to preventative maintenance for lab analysts in the wastewater industry provides a comprehensive roadmap for establishing and maintaining an effective maintenance program. By implementing these strategies, lab analysts can ensure the reliability and accuracy of their equipment, minimize downtime, and contribute to the overall success of their laboratory operations. Remember, preventative maintenance is not just a routine task—it is an investment in the future of your wastewater analysis work.