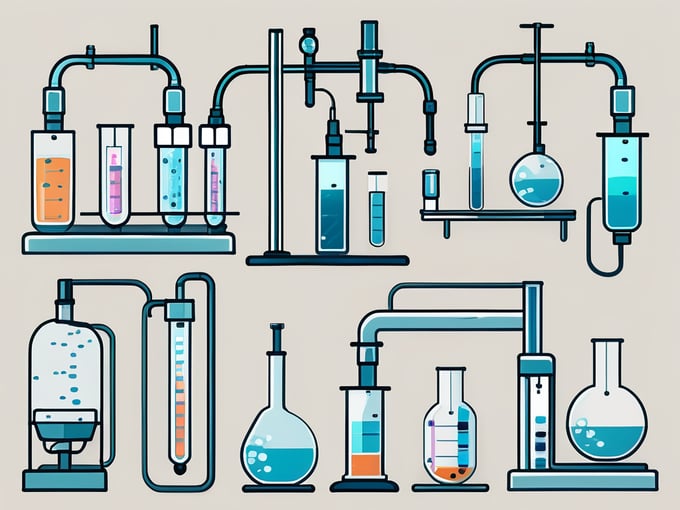
The Ultimate Guide to Preventative Maintenance for Lab Analysts in the Water Industry
In the water industry, lab analysts play a critical role in ensuring the safety and quality of our drinking water. They are responsible for conducting tests and analyzing samples to detect any contaminants or abnormalities. However, to perform their duties effectively and efficiently, lab analysts must also prioritize preventative maintenance. This comprehensive guide will delve into the importance of preventative maintenance for lab analysts in the water industry, outline essential tools and equipment, discuss how to develop a maintenance schedule, highlight maintenance procedures and protocols, explore training requirements, and provide insights into evaluating the effectiveness of a maintenance program.
Understanding the Importance of Preventative Maintenance
Preventative maintenance is the proactive approach to identifying and addressing potential issues before they escalate into costly problems. For lab analysts, this means regularly inspecting, cleaning, and calibrating equipment to ensure accurate and reliable test results. By investing time and effort in preventative maintenance, lab analysts can avoid unexpected breakdowns, reduce downtime, and enhance laboratory productivity.
One of the key reasons why preventative maintenance is crucial in the field of lab analysis is the impact it has on the overall efficiency of the laboratory. When equipment is well-maintained, it operates at its optimal level, allowing lab analysts to perform their tasks with precision and accuracy. This, in turn, leads to faster turnaround times for test results, enabling timely decision-making and action.
Moreover, preventative maintenance plays a vital role in ensuring the safety of lab analysts. By regularly inspecting equipment, potential hazards can be identified and addressed promptly. For example, faulty electrical connections or leaking chemicals can pose serious risks to the health and well-being of lab analysts. By proactively addressing these issues, lab analysts can create a safer working environment and minimize the chances of accidents or injuries.
The Role of Lab Analysts in the Water Industry
As the guardians of water quality, lab analysts play a crucial role in monitoring the safety of our drinking water. They analyze samples for various parameters, such as pH levels, chemical contaminants, and microbiological organisms. Accurate test results are essential for ensuring compliance with regulatory standards and protecting public health. By performing preventative maintenance on their equipment, lab analysts can minimize the risk of test errors and maintain the integrity of their analyses.
In the water industry, where the quality of drinking water directly impacts the health and well-being of individuals, the role of lab analysts becomes even more significant. Through their meticulous analysis and preventative maintenance practices, lab analysts help to safeguard the public from potential waterborne diseases and contaminants. Their dedication to maintaining accurate and reliable test results is crucial in ensuring that water treatment processes are effective and that the water we consume is safe.
Key Benefits of Regular Maintenance
Regular maintenance offers numerous benefits for lab analysts in the water industry. Firstly, it helps extend the lifespan of equipment, reducing the need for frequent replacements and saving costs in the long run. By regularly inspecting and cleaning equipment, lab analysts can identify and address minor issues before they escalate into major problems, thereby prolonging the lifespan of valuable equipment.
Secondly, regular maintenance enhances the accuracy and reliability of test results, enabling lab analysts to make informed decisions based on reliable data. When equipment is properly calibrated and functioning optimally, lab analysts can trust the results they obtain, ensuring that their analyses are accurate and dependable. This is particularly crucial in the water industry, where even the slightest deviation in test results can have significant consequences for public health and regulatory compliance.
Thirdly, preventative maintenance reduces the likelihood of equipment failures during critical analysis, which can lead to delays and compromise water safety. Imagine a scenario where a lab analyst is conducting an urgent test to determine the presence of a harmful chemical in the water supply. If the equipment malfunctions due to lack of maintenance, the entire analysis could be delayed, potentially putting public health at risk. By regularly maintaining equipment, lab analysts can minimize such risks and ensure that they can carry out critical analyses without any unforeseen interruptions.
Lastly, regular maintenance fosters a culture of responsibility, ensuring that lab analysts take ownership of their equipment and prioritize its upkeep. By instilling a sense of accountability, lab analysts become more proactive in identifying and addressing maintenance needs. This not only benefits the individual lab analyst but also contributes to the overall efficiency and effectiveness of the laboratory as a whole.
Essential Tools and Equipment for Preventative Maintenance
Maintaining the condition of tools and equipment is paramount for a lab analyst's success. In the water industry, two key areas require regular attention: water testing equipment and safety equipment.
Maintenance of Water Testing Equipment
Water testing equipment, such as spectrophotometers, pH meters, and turbidity meters, should be properly maintained to ensure accurate readings. Regular calibration and verification of instruments are essential to guarantee their precision. Lab analysts should follow manufacturer guidelines for maintenance and consult the user manual for specific procedures.
When it comes to spectrophotometers, it is crucial to clean the cuvettes after each use to prevent any residue from affecting subsequent readings. Regularly checking the light source and adjusting the wavelength calibration is also important to ensure accurate measurements. pH meters, on the other hand, require regular electrode calibration and cleaning to maintain their accuracy. Lab analysts should also check the condition of the probe and replace it if necessary.
Turbidity meters, used to measure the cloudiness or haziness of a liquid, should be regularly calibrated using a standard reference solution. Additionally, the sample chamber should be cleaned thoroughly after each use to prevent any residue from affecting future measurements. It is also important to check the light source and ensure it is functioning properly.
Furthermore, ensuring that spare parts and consumables are readily available will minimize disruptions caused by equipment breakdowns. Having extra cuvettes, electrodes, and calibration solutions on hand will ensure that lab analysts can quickly replace any faulty components and continue their work without delay.
Safety Equipment Maintenance
Lab safety is paramount, and the maintenance of safety equipment should never be overlooked. Personal protective equipment (PPE), such as safety goggles and gloves, should be regularly inspected for any signs of wear and tear. Lab analysts should ensure that the goggles have a proper seal and that the gloves are free from any punctures or tears.
Emergency eyewash stations and safety showers should be tested periodically to ensure they are functioning correctly. Lab analysts should activate the eyewash station and shower to check if there is a steady flow of water and that the water pressure is sufficient. It is also important to ensure that the drains are clear and unobstructed.
Additionally, fire extinguishers and fire alarm systems should be serviced and tested according to fire safety regulations. Lab analysts should inspect fire extinguishers to ensure they are fully charged and that the safety seals are intact. Fire alarm systems should be tested regularly to ensure they are functioning properly and that all smoke detectors and alarm bells are operational.
Regular training sessions should also be conducted to educate lab analysts on the proper use and maintenance of safety equipment. This will ensure that they are well-prepared in case of emergencies and can respond effectively to any hazardous situations that may arise.
Developing a Preventative Maintenance Schedule
Establishing a preventative maintenance schedule is crucial for lab analysts to stay on top of maintenance tasks. By scheduling routine inspections and calibrations, lab analysts can proactively address any issues that arise. However, determining the frequency of maintenance tasks and prioritizing them can be challenging.
When it comes to the frequency of maintenance tasks, there is no one-size-fits-all approach. The frequency can vary depending on the equipment and the manufacturer's recommendations. Some instruments may require monthly calibration, while others may require quarterly or annual maintenance. It is important for lab analysts to consult the equipment manuals and take into account the volume of testing performed to determine an appropriate maintenance schedule.
For high-throughput laboratories that handle a large volume of tests, it may be necessary to perform maintenance tasks more frequently to ensure the accuracy and reliability of the results. On the other hand, smaller laboratories with lower testing volumes may be able to space out maintenance tasks without compromising the quality of their work.
Striking a balance between regular maintenance and minimizing disruptions to laboratory operations is crucial. Lab analysts need to consider the impact of maintenance tasks on the availability of equipment for testing. It may be necessary to schedule maintenance during periods of low demand or plan for backup equipment to minimize any potential downtime.
Prioritizing Maintenance Tasks
Prioritizing maintenance tasks is essential to ensure that critical equipment receives the attention it deserves. Lab analysts should categorize maintenance tasks based on their impact on the accuracy of test results and the overall laboratory workflow.
High-priority tasks, such as temperature-controlled instrument calibration or routine cleaning of sample collection equipment, should be scheduled more frequently. These tasks directly affect the accuracy and reliability of test results, and any deviations can have significant consequences. By giving these tasks higher priority, lab analysts can ensure that the necessary checks and calibrations are performed regularly to maintain the integrity of the testing process.
On the other hand, there are maintenance tasks that have a lesser impact on test results and laboratory workflow. These tasks, such as checking power cords or verifying inventory levels, can be scheduled less frequently. While they are still important for the overall maintenance of the laboratory, they can be performed on a less frequent basis without compromising the quality of the work.
Lab analysts should also consider the availability of resources when prioritizing maintenance tasks. If there are limited resources, it may be necessary to prioritize tasks that require specialized tools or expertise. By allocating resources efficiently, lab analysts can ensure that critical equipment is properly maintained while optimizing the use of available resources.
In conclusion, developing a preventative maintenance schedule requires careful consideration of the frequency of maintenance tasks and prioritizing them based on their impact on test results and laboratory workflow. By striking the right balance and allocating resources effectively, lab analysts can ensure the smooth operation of the laboratory and the accuracy of test results.
Maintenance Procedures and Protocols
Having well-defined maintenance procedures and protocols is crucial for consistency and efficiency. It ensures that laboratory equipment is properly maintained, reducing the risk of errors and ensuring accurate test results. Standard operating procedures (SOPs) for maintenance tasks should be developed to guide lab analysts through the process, providing them with clear instructions and guidelines to follow.
When creating SOPs for maintenance, it is important to include step-by-step instructions that outline the specific tasks to be performed. This includes routine inspections, cleaning, calibrations, and verifications. Each step should be clearly defined, ensuring that analysts know exactly what needs to be done and in what order.
Safety precautions should also be incorporated into the SOPs to protect lab analysts from potential hazards. This includes wearing appropriate personal protective equipment (PPE), following proper handling procedures, and understanding the risks associated with specific maintenance tasks.
In addition to step-by-step instructions and safety precautions, SOPs should also include any specific requirements outlined by equipment manufacturers. This could include recommended maintenance schedules, specific cleaning agents to use, or calibration procedures. By following these manufacturer guidelines, lab analysts can ensure that the equipment is properly maintained and functions optimally.
Standard Operating Procedures for Maintenance
Standard operating procedures for maintenance should cover all necessary steps to be followed when performing routine inspections, cleaning, calibrations, and verifications. These procedures provide a standardized approach to maintenance tasks, ensuring consistency across different analysts and reducing the risk of errors.
When developing SOPs, it is important to outline the tools required for each maintenance task. This ensures that lab analysts have the necessary equipment readily available, allowing them to perform the maintenance efficiently. It is also important to include troubleshooting steps in the SOPs to address common issues that may arise during maintenance. This helps analysts identify and resolve problems quickly, minimizing equipment downtime.
Regular review of SOPs is essential to incorporate any updates or improvements to maintenance practices. As technology evolves and new best practices emerge, SOPs should be revised to reflect these changes. This ensures that maintenance procedures remain up-to-date and aligned with industry standards.
Compliance with Industry Standards
Compliance with industry standards is essential for maintaining the integrity of test results and meeting regulatory requirements. Lab analysts should familiarize themselves with relevant standards, such as ISO 17025 for testing laboratories, and ensure their maintenance practices align with these guidelines.
ISO 17025 is an international standard that specifies the general requirements for the competence of testing and calibration laboratories. It outlines the necessary quality management system and technical requirements that laboratories must meet to demonstrate their ability to produce accurate and reliable test results.
Regular audits and internal quality control checks can help identify areas for improvement and ensure ongoing compliance with industry standards. These audits involve reviewing maintenance records, inspecting equipment, and assessing the effectiveness of maintenance procedures. By conducting regular audits, laboratories can identify any deviations from the standard procedures and take corrective actions to maintain compliance.
In conclusion, having well-defined maintenance procedures and protocols is crucial for ensuring consistency, efficiency, and compliance with industry standards. By developing SOPs for maintenance tasks, laboratories can provide clear instructions and guidelines for lab analysts to follow. Compliance with industry standards, such as ISO 17025, ensures the integrity of test results and adherence to regulatory requirements. Regular review of SOPs and conducting audits help identify areas for improvement and ensure ongoing compliance with industry standards.
Training and Skills Required for Effective Maintenance
Training plays a key role in equipping lab analysts with the skills required for effective maintenance. To perform maintenance tasks competently, lab analysts should possess a combination of essential training and advanced skills.
Essential Training for Lab Analysts
Lab analysts should receive training on the specific equipment used in their laboratory. This training should cover basic maintenance procedures, such as cleaning, calibration, and verification. Additionally, lab analysts should understand the importance of documentation and record-keeping to track maintenance activities accurately.
Advanced Skills for Maintenance Efficiency
As lab analysts gain experience, advanced skills can be developed to improve maintenance efficiency. These skills may include troubleshooting common equipment issues, performing minor repairs, and optimizing preventive maintenance schedules. Continuous professional development through workshops, seminars, and online courses can enhance these skills and keep lab analysts up to date with the latest maintenance practices.
Evaluating the Effectiveness of Your Maintenance Program
Continuous evaluation of your maintenance program is crucial to identify areas for improvement and ensure optimal performance. Key performance indicators (KPIs) can help assess the effectiveness of the maintenance program.
Key Performance Indicators for Maintenance
Key performance indicators should be established to measure various aspects of maintenance, such as equipment uptime, response time to maintenance requests, and adherence to maintenance schedules. These KPIs can be tracked using maintenance management systems or spreadsheets. Regular analysis of KPIs will provide insights into the overall effectiveness of the maintenance program and highlight areas that require attention.
Continuous Improvement in Maintenance Practices
Maintenance practices should be continuously improved to adapt to changing technologies, regulations, and laboratory requirements. Feedback from lab analysts and other stakeholders should be encouraged to identify potential areas for improvement. Regular reviews of maintenance procedures and protocols can help streamline processes, enhance efficiency, and promote a culture of continuous improvement.
By prioritizing preventative maintenance, lab analysts in the water industry can ensure the reliability of test results, minimize equipment downtime, and contribute to the overall safety of our drinking water. The implementation of comprehensive maintenance programs, along with the necessary training and evaluation measures, will empower lab analysts to excel in their role as guardians of water quality.