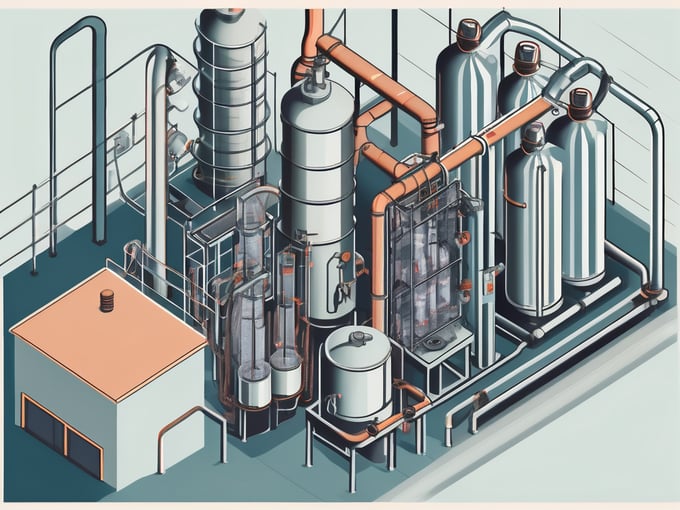
The Ultimate Guide to Preventative Maintenance for Plant Operators in the Water Industry
In the water industry, maintaining the smooth operation of water treatment plants is paramount. Preventative maintenance plays a crucial role in preserving the efficiency and reliability of these facilities. This comprehensive guide aims to provide plant operators with the knowledge and tools they need to implement and optimize an effective preventative maintenance plan. By understanding the importance of preventative maintenance, learning about its key components, and exploring practical implementation strategies, plant operators will be equipped to overcome common challenges and ensure water quality and regulatory compliance.
Understanding Preventative Maintenance
Preventative maintenance is not just a buzzword; it is a critical aspect of ensuring the smooth operation of water treatment plants. By proactively identifying and addressing potential issues before they escalate, plant operators can avoid unplanned downtime, reduce repair costs, and extend the lifespan of equipment and infrastructure. Furthermore, regular maintenance significantly contributes to maintaining water quality and the long-term sustainability of water treatment facilities.
Water treatment plants play a crucial role in providing clean and safe drinking water to communities. Without proper maintenance, these facilities can face various challenges that can impact their efficiency and effectiveness. Preventative maintenance acts as a safeguard against these challenges, ensuring that the treatment process runs smoothly and consistently.
One of the key components of preventative maintenance is regular inspection of equipment and infrastructure. This involves conducting thorough checks to identify any signs of wear and tear, corrosion, or malfunctioning components. By detecting these issues early on, plant operators can take immediate action to rectify them, preventing further damage and potential breakdowns.
In addition to inspections, lubrication and calibration of machinery are essential maintenance tasks. Proper lubrication ensures that moving parts operate smoothly, reducing friction and minimizing the risk of premature wear. Calibration, on the other hand, ensures that equipment is functioning within specified parameters, guaranteeing accurate and reliable performance.
Scheduled replacements of worn-out parts are another crucial aspect of preventative maintenance. Over time, components can become worn or damaged due to continuous use or exposure to harsh conditions. By proactively replacing these parts, plant operators can prevent equipment failures and maintain optimal performance.
Proactive monitoring of performance indicators is also a vital part of preventative maintenance. By regularly monitoring key metrics such as flow rates, pressure levels, and water quality parameters, operators can identify any deviations from normal operating conditions. This early detection allows for prompt troubleshooting and corrective actions, preventing potential issues from escalating into major problems.
Comprehensive record-keeping and documentation of maintenance activities play a significant role in effective preventative maintenance. By maintaining detailed records of inspections, repairs, and replacements, plant operators can track trends and identify recurring issues. This data-driven approach enables them to optimize maintenance schedules, allocate resources efficiently, and make informed decisions regarding equipment upgrades or replacements.
In conclusion, preventative maintenance is a critical practice in the water industry. It ensures the smooth operation of water treatment plants, reduces downtime and repair costs, and extends the lifespan of equipment and infrastructure. By implementing regular inspections, lubrication and calibration, scheduled replacements, and proactive monitoring, plant operators can maintain water quality and ensure the long-term sustainability of water treatment facilities.
Implementing a Preventative Maintenance Plan
Preventative maintenance is a crucial aspect of managing a plant's assets and ensuring their optimal performance. By following a systematic approach, plant operators can develop an effective plan that helps prevent equipment failures, reduces downtime, and extends the lifespan of critical assets.
Steps to Develop a Preventative Maintenance Plan
Developing a preventative maintenance plan requires careful consideration and thorough assessment of the plant's assets. By following these steps, plant operators can create a comprehensive plan:
- Conduct a thorough assessment: Before developing a maintenance plan, it is crucial to assess the plant's assets and determine their criticality. This assessment helps prioritize maintenance activities and allocate resources efficiently. By identifying the most critical equipment, plant operators can focus their efforts on ensuring their proper functioning.
- Develop a detailed schedule: Once the critical assets are identified, plant operators must develop a detailed schedule for routine maintenance tasks. This schedule should consider equipment specifications, manufacturers' recommendations, and industry best practices. By following a well-structured schedule, operators can ensure that maintenance tasks are performed at the right time, reducing the risk of unexpected failures.
- Implement regular inspections: In addition to routine maintenance tasks, regular inspections are essential for identifying potential issues before they escalate. Plant operators should establish a comprehensive inspection program that includes visual inspections, equipment testing, and data analysis. By detecting early warning signs, operators can take proactive measures to prevent equipment failures.
- Train and educate personnel: A preventative maintenance plan is only as effective as the people implementing it. Plant operators should invest in training and educating personnel on proper maintenance procedures, safety protocols, and equipment handling. By equipping the workforce with the necessary knowledge and skills, operators can ensure that maintenance tasks are performed accurately and efficiently.
- Continuously evaluate and adjust: A preventative maintenance plan should not be static. Ongoing evaluation and adjustment based on feedback from operators and performance data are crucial for continuous improvement. By analyzing maintenance records, identifying recurring issues, and implementing corrective actions, plant operators can refine their maintenance plan and optimize asset performance.
Tools and Equipment Needed for Preventative Maintenance
Implementing a preventative maintenance plan requires the use of specific tools and equipment. These tools aid in measuring, diagnosing, and maintaining equipment. Some essential tools and equipment include:
- Instruments for measuring parameters: To monitor equipment performance, plant operators need instruments for measuring various parameters such as flow rate, pressure, and water quality. These instruments help identify deviations from normal operating conditions and enable operators to take appropriate corrective actions.
- Diagnostic tools: Diagnostic tools, such as vibration analyzers and thermal cameras, play a crucial role in preventative maintenance. Vibration analyzers help detect potential faults in rotating machinery by analyzing vibration patterns, while thermal cameras detect abnormal heat signatures that indicate equipment malfunctions. These tools enable operators to identify issues before they lead to costly failures.
- Maintenance tools: A range of maintenance tools, including wrenches, lubrication equipment, and alignment devices, are essential for conducting routine maintenance tasks. These tools facilitate tasks such as tightening bolts, lubricating moving parts, and ensuring proper alignment, all of which contribute to equipment reliability and longevity.
It is essential for plant operators to have access to these tools and ensure they are properly maintained. Regular calibration, inspection, and replacement of worn-out tools are necessary to maintain their accuracy and effectiveness.
The Role of Plant Operators in Preventative Maintenance
Plant operators play a vital role in carrying out daily preventative maintenance tasks. This includes conducting regular inspections, monitoring equipment performance, and promptly addressing minor issues. They are responsible for cleaning filters, lubricating moving parts, and ensuring proper calibration of instruments. By closely observing the operational status of the plant, operators can detect any abnormalities or signs of potential failure, thereby preventing expensive breakdowns or interruptions in supply.
However, the responsibilities of plant operators go beyond just the daily tasks of maintenance. They also play a crucial role in developing and implementing preventative maintenance strategies. This involves analyzing historical data and trends to identify potential areas of improvement. By proactively addressing these areas, operators can minimize the risk of unexpected failures and optimize the overall performance of the plant.
Furthermore, plant operators are often involved in conducting risk assessments and developing maintenance schedules. They collaborate with other team members, such as maintenance engineers and technicians, to ensure that all maintenance activities are carried out efficiently and effectively. This requires strong organizational skills and the ability to prioritize tasks based on the criticality of equipment and systems.
Daily Tasks of Plant Operators for Maintenance
In addition to the aforementioned responsibilities, plant operators perform a wide range of daily tasks to ensure the smooth operation of the plant. These tasks may include:
- Inspecting and cleaning equipment, such as pumps, motors, and compressors, to remove any dirt or debris that may hinder their performance.
- Checking fluid levels, such as oil and coolant, and replenishing them as necessary.
- Monitoring and recording equipment readings, such as pressure, temperature, and flow rates, to identify any deviations from normal operating conditions.
- Conducting routine tests and inspections, such as vibration analysis and thermography, to detect any early signs of equipment failure.
- Performing preventive maintenance tasks, such as replacing worn-out parts and adjusting equipment settings, to prevent potential breakdowns.
- Collaborating with maintenance technicians to troubleshoot and resolve any equipment malfunctions or abnormalities.
Training and Skills Required for Plant Operators
Plant operators need to possess a diverse range of skills to effectively carry out preventative maintenance tasks. In addition to technical knowledge about pumps, valves, and other equipment, they should be familiar with safety protocols and emergency procedures. Ongoing training and professional development programs are instrumental in keeping operators up-to-date with the latest advancements in maintenance practices and technological innovations.
Moreover, effective communication skills are essential for plant operators. They need to be able to convey information clearly and concisely to their team members and superiors. This includes reporting any maintenance issues or concerns, as well as providing feedback on the performance of equipment and systems.
The ability to collaborate with other team members is also vital for ensuring streamlined maintenance operations. Plant operators often work closely with maintenance engineers, technicians, and supervisors to plan and execute maintenance activities. They need to be able to work well in a team environment, share knowledge and expertise, and contribute to the overall success of the maintenance department.
In conclusion, plant operators play a critical role in preventative maintenance. Their daily tasks, such as inspections, monitoring, and addressing minor issues, help prevent costly breakdowns and interruptions in supply. Additionally, their involvement in developing maintenance strategies and collaborating with other team members ensures the efficient and effective operation of the plant. With the right training, skills, and mindset, plant operators contribute significantly to the overall success of maintenance operations.
Common Challenges in Preventative Maintenance
Identifying Potential Issues in Water Treatment Plants
The complexity of water treatment plants poses numerous challenges in early issue identification. Subtle changes in equipment performance or water quality may signify underlying problems that require immediate attention. By utilizing technological advancements such as sensors and data analytics, plant operators can monitor and analyze critical parameters to identify issues before they escalate. Additionally, conducting regular audits and collaborating with external experts can provide valuable insights into potential vulnerabilities in the plant's infrastructure.
Water treatment plants are intricate systems that require constant vigilance to ensure efficient operation and the production of clean, safe drinking water. The process involves multiple stages, including coagulation, flocculation, sedimentation, filtration, and disinfection. Each stage requires precise control and monitoring to maintain optimal performance.
One common challenge in preventative maintenance is the identification of potential issues. With the complexity of the equipment and the vast amount of data generated, it can be difficult to pinpoint subtle changes that may indicate underlying problems. However, advancements in technology have provided solutions to this challenge. Sensors placed strategically throughout the plant can continuously monitor critical parameters such as flow rates, pressure levels, and water quality. This real-time data is then analyzed using sophisticated algorithms and data analytics tools to identify any deviations from normal operating conditions.
Another challenge in preventative maintenance is the need for regular audits and collaboration with external experts. Water treatment plants are subject to strict regulations and guidelines to ensure the quality and safety of the water produced. Regular audits conducted by external experts can help identify potential vulnerabilities in the plant's infrastructure and processes. These audits may include inspections of equipment, analysis of operational data, and verification of compliance with regulatory requirements. Collaborating with external experts also provides an opportunity to tap into their knowledge and experience, gaining valuable insights and recommendations for improvement.
Overcoming Obstacles in Preventative Maintenance
Implementing preventative maintenance can be challenging due to various factors. Limited resources, such as budget constraints or shortages of skilled personnel, may hamper maintenance efforts. To overcome these obstacles, plant operators can emphasize the importance of preventative maintenance to stakeholders and secure adequate funding. Leveraging automation and digitalization can also streamline maintenance processes and optimize resource allocation. Continuous communication and collaboration between operators, maintenance staff, and management play a crucial role in ensuring that preventative maintenance activities are prioritized and integrated into the overall plant operations.
Preventative maintenance is essential for the long-term reliability and performance of water treatment plants. It helps identify and address potential issues before they escalate, minimizing downtime, and reducing the risk of costly repairs or system failures. However, implementing preventative maintenance can be challenging, especially in the face of limited resources.
One common obstacle is budget constraints. Water treatment plants often operate on tight budgets, with limited funds allocated for maintenance activities. Plant operators can overcome this challenge by emphasizing the importance of preventative maintenance to stakeholders, including government agencies, utility boards, and the public. Demonstrating the long-term cost savings and benefits of proactive maintenance can help secure adequate funding for necessary maintenance activities.
Another obstacle is the shortage of skilled personnel. Water treatment plants require a diverse range of skills, including mechanical, electrical, and chemical expertise. However, there is often a shortage of qualified personnel in these fields. To address this challenge, plant operators can invest in training and development programs to upskill existing staff. Additionally, they can collaborate with educational institutions and industry organizations to attract and train new talent.
Automation and digitalization are also valuable tools in overcoming obstacles in preventative maintenance. By leveraging technology, plant operators can streamline maintenance processes, optimize resource allocation, and improve overall efficiency. For example, implementing a computerized maintenance management system (CMMS) can help automate scheduling, work order generation, and asset tracking. This reduces the administrative burden on maintenance staff and ensures that maintenance activities are carried out in a timely manner.
Lastly, continuous communication and collaboration between operators, maintenance staff, and management are vital in ensuring that preventative maintenance activities are prioritized and integrated into the overall plant operations. Regular meetings, feedback sessions, and performance reviews can help identify areas for improvement and ensure that maintenance efforts align with the plant's goals and objectives.
The Impact of Preventative Maintenance on Water Quality
How Maintenance Affects Water Safety
Regular preventative maintenance directly contributes to ensuring water safety. By proactively maintaining filters, membranes, and disinfection systems, plant operators minimize the risk of contaminants entering the water supply. Additionally, maintenance activities such as pipe inspection and repair prevent leaks and reduce the potential for cross-contamination. Maintaining optimal operating conditions, such as flow rates and pressure, helps guarantee that treatment processes are functioning at their highest efficacy, thereby preserving water quality and safeguarding public health.
The Role of Maintenance in Ensuring Regulatory Compliance
Meeting regulatory requirements is of utmost importance in the water industry. Preventative maintenance plays a crucial role in maintaining compliance with standards and regulations. Regular maintenance activities enable plant operators to document system performance, measure adherence to prescribed operating parameters, and demonstrate ongoing compliance. By implementing a robust preventative maintenance program, water treatment plants can confidently navigate regulatory audits and avoid costly penalties or reputation damage.
Future Trends in Preventative Maintenance
Technological Innovations in Maintenance
The rapid development of technology offers promising advancements in preventative maintenance. The integration of Internet of Things (IoT) devices and real-time data analytics provides plant operators with insights into equipment health and performance. Predictive maintenance algorithms can forecast equipment failures, enabling proactive interventions before costly breakdowns occur. Additionally, remote monitoring and augmented reality tools facilitate efficient troubleshooting and remote assistance. As technology continues to evolve, plant operators must stay informed about emerging trends and consider their implementation to enhance maintenance practices.
The Role of Sustainability in Preventative Maintenance
Sustainability has become an integral consideration in modern maintenance practices. Implementing energy-efficient equipment, optimizing maintenance schedules to minimize downtime, and employing eco-friendly chemicals are just a few ways in which preventative maintenance can contribute to sustainability efforts. Plant operators should explore opportunities to adopt renewable energy sources and implement environmentally friendly practices within the maintenance routines. By embracing sustainability as a core principle, water treatment plants can ensure long-term environmental stewardship and reduce their carbon footprint.
As plant operators in the water industry, understanding and implementing preventative maintenance practices is essential for optimizing the performance, reliability, and safety of water treatment plants. By following the guidelines outlined in this ultimate guide to preventative maintenance, operators can confidently navigate the challenges, maintain regulatory compliance, and contribute to the sustainable provision of safe and clean water to communities. Embrace the power of preventative maintenance and pave the way for the future of the water industry.