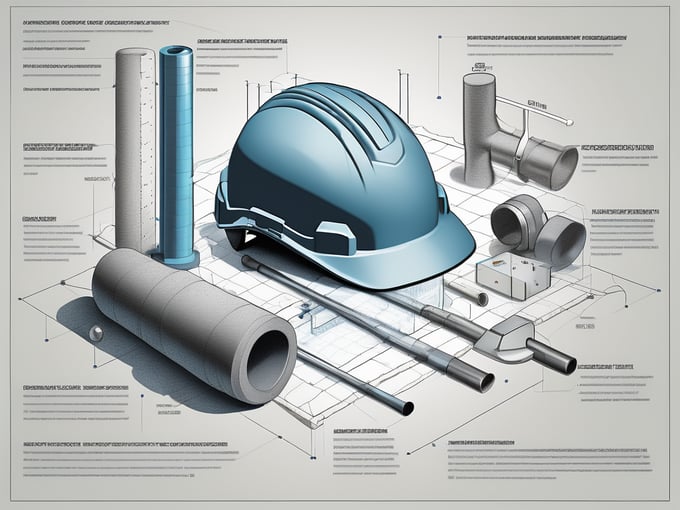
The Ultimate Guide to Preventative Maintenance for Safety Officers in the Groundwater Management Industry
In the groundwater management industry, preventative maintenance plays a crucial role in ensuring the safety and efficiency of operations. Safety officers are at the forefront of this effort, responsible for implementing and overseeing preventative maintenance programs to mitigate risks and prevent accidents. In this comprehensive guide, we will explore the importance of preventative maintenance, essential techniques, program implementation, the role of technology, and evaluating the success of your maintenance efforts.
Understanding the Importance of Preventative Maintenance
Preventative maintenance is a proactive approach to maintenance that focuses on preventing equipment failures and minimizing downtime. In the groundwater management industry, where safety is paramount, preventative maintenance is essential to ensure the continuous operation of wells and related infrastructure.
Groundwater management is a complex and critical process that involves the extraction, treatment, and distribution of water from underground sources. It is crucial to maintain the equipment and infrastructure involved in this process to ensure the safety of workers, protect the environment, and provide a reliable water supply to communities.
The Role of Safety Officers in Groundwater Management
Safety officers play a crucial role in groundwater management by overseeing the safety and maintenance of equipment and infrastructure. They are responsible for implementing preventative maintenance measures to minimize the risk of accidents, injuries, and environmental damage.
These dedicated professionals work closely with engineers, technicians, and other stakeholders to develop comprehensive maintenance plans tailored to the specific needs of groundwater management systems. They conduct regular inspections, monitor equipment performance, and coordinate repairs to ensure the smooth operation of wells, pumps, filtration systems, and other essential components.
Moreover, safety officers are responsible for ensuring compliance with relevant regulations and industry standards. They stay up-to-date with the latest advancements in technology and best practices to continuously improve maintenance strategies and enhance safety protocols.
Key Principles of Preventative Maintenance
To effectively implement preventative maintenance, safety officers must understand and adhere to key principles:
- Regular Inspections: Conduct regular inspections to identify potential issues before they escalate. Safety officers meticulously examine equipment, pipelines, valves, and other critical components to detect signs of wear, corrosion, leaks, or any other abnormalities that may compromise the system's integrity.
- Thorough Monitoring: Monitor equipment performance and environmental conditions to detect anomalies. Safety officers utilize advanced monitoring systems, such as sensors and data loggers, to track variables like pressure, flow rate, temperature, and water quality. By analyzing this data, they can identify deviations from normal operating parameters and take appropriate action.
- Proactive Repairs: Address identified issues promptly to prevent further damage or safety hazards. Safety officers work closely with maintenance teams to ensure that repairs are carried out in a timely manner. They prioritize repairs based on the severity of the issue and its potential impact on the groundwater management system.
- Scheduled Maintenance: Implement a well-defined schedule for routine maintenance tasks, such as lubrication, filter replacement, and calibration. Safety officers develop comprehensive maintenance schedules that outline specific tasks, frequencies, and responsible personnel. This systematic approach helps prevent equipment failures and ensures that essential maintenance activities are not overlooked.
- Data-Driven Decision Making: Utilize data and analytics to make informed decisions about maintenance priorities. Safety officers collect and analyze data from various sources to gain insights into the performance and condition of the groundwater management system. By leveraging this information, they can identify trends, predict potential issues, and allocate resources effectively.
By adhering to these principles, safety officers can establish a robust preventative maintenance program that maximizes the lifespan of equipment, minimizes downtime, and enhances the overall safety and efficiency of groundwater management operations.
Essential Preventative Maintenance Techniques
Implementing the right preventative maintenance techniques is crucial to ensure the longevity and performance of groundwater management equipment and infrastructure.
Groundwater management is a critical aspect of maintaining a sustainable water supply. It involves the careful monitoring and control of groundwater levels to prevent depletion and contamination. To effectively manage groundwater, it is essential to implement preventative maintenance techniques that keep the equipment and infrastructure in optimal condition.
Regular Inspection and Monitoring
Regular inspections allow safety officers to identify potential issues early on. This can include visual inspections, equipment condition assessments, and performance monitoring. By conducting routine inspections, safety officers can ensure that all components of the groundwater management system are functioning properly.
During visual inspections, safety officers carefully examine the equipment for any signs of wear and tear, corrosion, or leaks. They also inspect the surrounding infrastructure, such as pipes and valves, to ensure there are no signs of damage or deterioration. Additionally, equipment condition assessments involve evaluating the performance of pumps, motors, and other mechanical components to identify any potential problems.
Performance monitoring is another crucial aspect of regular inspection. By continuously monitoring the system's performance, safety officers can detect any deviations from normal operating conditions. This can include monitoring flow rates, pressure levels, and water quality parameters. By detecting and addressing problems proactively, safety officers can prevent costly breakdowns or accidents.
Predictive Maintenance Strategies
Predictive maintenance leverages advanced monitoring technologies, such as vibration analysis, thermography, and oil analysis. By monitoring key indicators, safety officers can detect signs of impending failure and take corrective action before it occurs.
Vibration analysis involves measuring the vibration levels of rotating equipment, such as pumps and motors. By analyzing the vibration patterns, safety officers can identify any abnormalities that may indicate a potential failure. This allows them to schedule maintenance activities and replace worn-out components before they cause a breakdown.
Thermography, on the other hand, uses infrared cameras to detect temperature variations in equipment. By identifying hotspots or abnormal temperature patterns, safety officers can pinpoint potential issues, such as overheating or insulation problems. This enables them to take corrective measures to prevent equipment failure.
Oil analysis is another valuable predictive maintenance technique. By analyzing the properties and contaminants in lubricating oils, safety officers can assess the condition of equipment, such as pumps and motors. This helps them identify any signs of wear, contamination, or degradation, allowing them to schedule maintenance activities accordingly.
By implementing regular inspection and monitoring, as well as predictive maintenance strategies, safety officers can ensure the reliable and efficient operation of groundwater management equipment and infrastructure. This not only extends the lifespan of the equipment but also minimizes the risk of unexpected failures and costly repairs.
Implementing a Preventative Maintenance Program
Developing and implementing an effective preventative maintenance program is essential for safety officers in the groundwater management industry. By following these steps, you can establish a robust maintenance plan:
Steps to Develop an Effective Maintenance Plan
1. Assess Equipment: Identify the critical equipment that requires preventative maintenance.
2. Define Maintenance Tasks: Determine the specific maintenance tasks required for each equipment type.
3. Establish a Schedule: Develop a schedule for performing routine maintenance tasks based on equipment manufacturer recommendations and industry best practices.
4. Assign Responsibilities: Assign roles and responsibilities for maintenance activities, ensuring clear accountability.
5. Document Procedures: Create detailed procedures for performing maintenance tasks, including step-by-step instructions and safety guidelines.
6. Track and Evaluate: Implement a system to track maintenance activities and evaluate their effectiveness.
Training and Skill Development for Maintenance
Equipping safety officers with the necessary skills and knowledge is crucial for the success of any preventative maintenance program. Provide comprehensive training on equipment operation, maintenance techniques, and safety protocols. Continuous learning, certifications, and workshops can further enhance the skill sets of safety officers.
When it comes to assessing equipment, safety officers need to have a keen eye for identifying critical components that require preventative maintenance. This involves conducting thorough inspections and utilizing diagnostic tools to detect any potential issues before they escalate into major problems. By regularly assessing the equipment, safety officers can ensure that all necessary maintenance tasks are identified and addressed in a timely manner.
Defining maintenance tasks is another crucial step in developing an effective maintenance plan. Safety officers need to have a clear understanding of the specific tasks that need to be performed for each equipment type. This includes tasks such as lubrication, calibration, cleaning, and inspection. By defining these tasks, safety officers can ensure that all necessary maintenance activities are carried out consistently and effectively.
Establishing a schedule for routine maintenance tasks is essential to ensure that equipment remains in optimal condition. Safety officers should consider equipment manufacturer recommendations and industry best practices when developing the maintenance schedule. By adhering to a regular maintenance schedule, safety officers can minimize the risk of equipment failure and maximize the lifespan of the equipment.
Assigning responsibilities is a critical aspect of a preventative maintenance program. Safety officers need to clearly define roles and responsibilities for maintenance activities to ensure that everyone understands their accountability. This includes designating individuals who will be responsible for performing specific maintenance tasks, as well as those who will oversee the overall maintenance program. By assigning responsibilities, safety officers can create a culture of ownership and accountability within the organization.
Documenting procedures is essential for ensuring consistency and efficiency in maintenance activities. Safety officers should create detailed procedures that outline step-by-step instructions for performing maintenance tasks. These procedures should also include safety guidelines to ensure that maintenance activities are carried out in a safe manner. By documenting procedures, safety officers can provide clear guidance to maintenance personnel and minimize the risk of errors or accidents.
Implementing a system to track maintenance activities and evaluate their effectiveness is crucial for continuous improvement. Safety officers should utilize maintenance management software or other tracking tools to record and monitor maintenance tasks. This allows them to track the frequency and duration of maintenance activities, identify trends or patterns, and assess the overall effectiveness of the maintenance program. By regularly evaluating the maintenance activities, safety officers can identify areas for improvement and make necessary adjustments to optimize the program.
Training and Skill Development for Maintenance
Equipping safety officers with the necessary skills and knowledge is crucial for the success of any preventative maintenance program. Comprehensive training should be provided to safety officers on equipment operation, maintenance techniques, and safety protocols. This training should cover topics such as equipment troubleshooting, preventive maintenance strategies, and emergency response procedures. By ensuring that safety officers are well-trained, organizations can minimize the risk of equipment failure and ensure the safety of personnel.
Continuous learning is essential in the field of maintenance. Safety officers should be encouraged to pursue certifications and attend workshops or seminars to enhance their knowledge and skills. These learning opportunities can provide safety officers with the latest industry insights, best practices, and technological advancements in maintenance. By staying updated with the latest developments, safety officers can continuously improve their maintenance practices and contribute to the overall success of the preventative maintenance program.
In conclusion, developing and implementing an effective preventative maintenance program requires careful planning, clear communication, and continuous improvement. By following the steps outlined above and investing in training and skill development, safety officers can establish a robust maintenance plan that ensures the reliability, safety, and longevity of equipment in the groundwater management industry.
Technology in Preventative Maintenance
Technology has revolutionized preventative maintenance in the groundwater management industry, empowering safety officers with powerful tools to streamline operations and enhance efficiency.
With the rapid advancement of technology, the groundwater management industry has witnessed a significant transformation in the way maintenance is conducted. Specialized software and tools have emerged, offering a wide range of features to aid in maintenance management.
Modern Tools and Software for Maintenance Management
These innovative tools provide safety officers with the ability to track maintenance schedules with ease. Gone are the days of manual record-keeping and cumbersome spreadsheets. With just a few clicks, safety officers can now generate work orders, manage inventory, and analyze equipment performance data.
Imagine a scenario where safety officers can effortlessly monitor the maintenance status of multiple sites simultaneously. This level of efficiency not only saves time but also ensures that no maintenance task goes unnoticed or delayed.
Moreover, the integration of these tools with cloud-based platforms allows for seamless collaboration among team members. Safety officers can assign tasks, share progress updates, and communicate with technicians in real-time, all within a centralized system.
By adopting such tools, safety officers can significantly improve efficiency and reduce costs. The streamlined processes enable them to allocate resources more effectively, ensuring that maintenance tasks are completed promptly and with precision.
The Impact of Automation and AI in Maintenance
While modern tools have revolutionized maintenance management, the introduction of automation and Artificial Intelligence (AI) has taken it to a whole new level.
Predictive analytics, powered by machine learning algorithms, has become a game-changer in the industry. Safety officers can now leverage historical data and real-time information to predict equipment failures before they occur. This proactive approach, known as predictive maintenance, helps prevent costly breakdowns and minimizes downtime.
Furthermore, the Internet of Things (IoT) sensors play a crucial role in enabling real-time monitoring of equipment performance. These sensors collect data on various parameters such as temperature, pressure, and vibration, providing valuable insights into the health of the equipment. Safety officers can then make data-driven decisions, optimizing maintenance efforts and ensuring the longevity of the equipment.
Artificial Intelligence algorithms, combined with the power of automation, can analyze vast amounts of data in a fraction of the time it would take a human. This not only saves valuable resources but also increases the accuracy of maintenance predictions. Safety officers can rely on these advanced technologies to identify patterns, detect anomalies, and make informed decisions regarding maintenance tasks.
In conclusion, the integration of technology into preventative maintenance has revolutionized the groundwater management industry. Modern tools and software have simplified maintenance management, while automation and AI have enabled predictive maintenance and real-time monitoring. As technology continues to advance, safety officers can expect even more innovative solutions to enhance efficiency and ensure the smooth operation of groundwater management systems.
Evaluating the Success of Your Preventative Maintenance Program
Continuous evaluation of your preventative maintenance program is vital for identifying areas of improvement and ensuring long-term success.
When it comes to evaluating the success of your preventative maintenance program, there are several key performance indicators (KPIs) that you should monitor and analyze. These KPIs can provide valuable insights into the effectiveness of your maintenance efforts and help you make data-driven decisions for improvement.
Key Performance Indicators for Maintenance Success
One important KPI to consider is equipment uptime. By tracking the amount of time your equipment is operational, you can get a sense of how well your preventative maintenance program is preventing breakdowns and minimizing downtime. High equipment uptime indicates that your maintenance efforts are effective in keeping your equipment in good working condition.
Another KPI to monitor is the mean time between failures (MTBF). This metric measures the average amount of time that passes between equipment failures. A longer MTBF indicates that your preventative maintenance program is successfully reducing the frequency of breakdowns and increasing the reliability of your equipment.
In addition to equipment uptime and MTBF, it's also important to keep an eye on maintenance costs. By tracking the amount of money you spend on maintenance activities, you can assess the efficiency of your preventative maintenance program. Ideally, your maintenance costs should be reasonable and proportional to the value of the equipment you are maintaining.
By regularly monitoring and analyzing these KPIs, safety officers can gain a comprehensive understanding of the effectiveness of their preventative maintenance program. Armed with this knowledge, they can identify areas of improvement and make informed decisions to optimize their maintenance efforts.
Continuous Improvement in Preventative Maintenance
While evaluating the success of your preventative maintenance program is important, it's equally crucial to embrace a culture of continuous improvement. This involves seeking feedback from maintenance personnel, monitoring industry trends, and implementing lessons learned from past incidents.
Maintenance personnel are on the front lines of your maintenance program, and their insights and experiences can provide valuable feedback for improvement. Regularly engaging with them and encouraging open communication can help identify potential issues and areas for enhancement.
Monitoring industry trends is another key aspect of continuous improvement. Technology and best practices in maintenance are constantly evolving, and staying up-to-date with the latest advancements can help you optimize your preventative maintenance program. Attending conferences, workshops, and webinars, and networking with industry professionals can provide valuable insights into emerging trends and innovative approaches to maintenance.
Furthermore, it's important to learn from past incidents and near-misses. Analyzing the root causes of failures and incidents can help you identify weaknesses in your maintenance program and implement corrective actions to prevent similar occurrences in the future. By continuously learning from your experiences, you can refine and enhance your preventative maintenance program over time.
By following the principles and implementing the techniques outlined in this guide, safety officers in the groundwater management industry can establish a robust preventative maintenance program. Through proactive measures, leveraging technology, and continuous improvement, they play a vital role in promoting safety, efficiency, and environmental responsibility in groundwater management operations.
Remember, preventative maintenance is not a one-time task but an ongoing commitment. Start implementing preventative maintenance today to safeguard your organization's success and secure a sustainable future for the groundwater management industry.