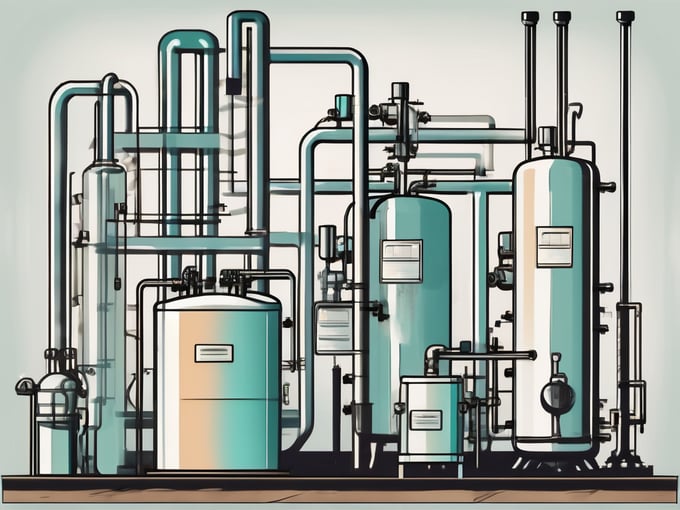
The Ultimate Guide to Preventative Maintenance for Specifying Engineers in the Water Industry
In the water industry, preventative maintenance plays a crucial role in ensuring the smooth operation and longevity of various systems and equipment. Understanding the importance of preventative maintenance is essential for specifying engineers who are responsible for the design and specification of such systems. This comprehensive guide aims to provide a deep dive into the key concepts, responsibilities, tools, challenges, and future trends in preventative maintenance for specifying engineers in the water industry.
Understanding the Importance of Preventative Maintenance
Preventative maintenance is the proactive approach to maintenance that focuses on preventing potential issues and breakdowns before they occur. In the water industry, where reliability and efficiency are paramount, this preventive approach plays a critical role in minimizing downtime, improving system performance, and ensuring compliance with regulatory requirements. By implementing a well-structured preventative maintenance plan, specifying engineers can optimize the life cycle of equipment, reduce costly repairs, and enhance overall operational efficiency.
Preventative maintenance goes beyond just fixing things when they break. It involves a systematic and strategic approach to identifying and addressing potential issues. This can include regular inspections, testing, servicing, and the replacement of worn-out parts. By taking a proactive stance, specifying engineers can prevent small problems from escalating into major breakdowns, ultimately saving time, money, and resources.
The Role of Preventative Maintenance in the Water Industry
Preventative maintenance serves as the backbone of the water industry. Its primary role is to identify and address potential issues in a timely manner, keeping the systems running smoothly and preventing unexpected failures. By conducting regular inspections, testing, and servicing, specifying engineers can identify and rectify small problems before they escalate into major breakdowns, minimizing disruptions in water supply, treatment processes, and distribution networks.
Water treatment plants, for example, rely heavily on preventative maintenance to ensure the quality and safety of the water being supplied to consumers. Regular checks and maintenance of filtration systems, pumps, and valves are essential to prevent contamination and ensure that the water meets regulatory standards. Without proper maintenance, these systems can become inefficient, leading to compromised water quality and potential health risks.
In addition to maintaining water quality, preventative maintenance also plays a crucial role in optimizing the overall efficiency of water systems. By regularly inspecting and cleaning equipment, specifying engineers can ensure that everything is operating at peak performance. This not only reduces energy consumption but also extends the lifespan of equipment, ultimately saving money in the long run.
The Impact of Neglecting Preventative Maintenance
Neglecting preventative maintenance can have severe consequences in the water industry. When equipment and systems are not properly maintained, they become more prone to breakdowns, leading to costly repairs, unscheduled downtime, and even safety hazards. Additionally, the lack of maintenance can impact water quality, compromising the health and well-being of consumers.
Imagine a scenario where a water pump in a treatment plant fails unexpectedly due to lack of maintenance. This could result in a sudden disruption of water supply to an entire community, causing inconvenience and potential health risks. The cost of repairing or replacing the pump, as well as the loss of revenue due to downtime, can be substantial. Furthermore, if the water quality is compromised during the breakdown, it could lead to widespread contamination and health issues for the consumers.
By understanding the potential consequences of neglecting preventative maintenance, specifying engineers can emphasize its importance and drive the implementation of effective maintenance programs. They can educate stakeholders about the long-term benefits of investing in regular maintenance, such as improved reliability, reduced downtime, and enhanced customer satisfaction. Additionally, by highlighting the potential cost savings and regulatory compliance that come with preventative maintenance, engineers can gain support and resources to implement comprehensive maintenance plans.
Key Concepts in Preventative Maintenance
Before diving into the specifics of preventative maintenance, it is essential to grasp the key concepts that form its foundation. By familiarizing themselves with these concepts, specifying engineers can develop a solid understanding of the principles that guide effective maintenance strategies.
One important concept in preventative maintenance is the idea of proactive care. Unlike reactive maintenance, which involves addressing equipment failures after they occur, preventative maintenance focuses on preventing those failures from happening in the first place. This proactive approach helps to minimize downtime, reduce repair costs, and extend the lifespan of equipment.
Another key concept is the use of routine inspections. These inspections involve regularly examining equipment to identify any signs of wear, damage, or potential issues. By detecting problems early on, specifying engineers can take corrective action before they escalate into major failures. Inspections also provide an opportunity to assess the overall condition of the equipment and determine if any adjustments or replacements are necessary.
The Basics of Preventative Maintenance
At its core, preventative maintenance involves a series of planned activities aimed at preventing the occurrence of equipment failures. It includes routine inspections, lubrication, cleaning, adjustments, and replacements based on manufacturer recommendations, industry best practices, and equipment performance data. By adhering to these basic maintenance tasks, specifying engineers can ensure the reliability and performance of vital water industry assets.
Lubrication is an essential aspect of preventative maintenance. Proper lubrication helps to reduce friction and wear between moving parts, extending their lifespan and preventing premature failure. Different types of equipment require different lubricants, and specifying engineers must ensure that they use the correct lubricant in the appropriate quantities.
Cleaning is another crucial component of preventative maintenance. Over time, equipment can accumulate dirt, debris, and other contaminants, which can hinder its performance and lead to malfunctions. Regular cleaning helps to remove these substances and maintain optimal operating conditions.
Adjustments are necessary to ensure that equipment operates within specified parameters. These adjustments may involve calibrating sensors, aligning components, or fine-tuning settings. By making these adjustments on a regular basis, specifying engineers can optimize equipment performance and prevent issues related to misalignment or incorrect settings.
Advanced Techniques in Preventative Maintenance
Beyond the basics, advanced techniques in preventative maintenance are continuously evolving to enhance reliability and efficiency. These techniques include condition-based monitoring, predictive analytics, and remote monitoring systems.
Condition-based monitoring utilizes sensors and data analysis to assess the health of equipment and detect potential issues in real-time. By continuously monitoring key parameters such as temperature, vibration, and pressure, engineers can identify abnormal patterns or deviations from normal operating conditions. This early detection allows for timely intervention and preventive measures to be taken, reducing the risk of unexpected failures.
Predictive analytics employ algorithms to forecast equipment failures based on historical data and patterns. By analyzing data from past failures and equipment performance, engineers can identify trends and patterns that indicate the likelihood of future failures. This information enables them to prioritize maintenance activities and allocate resources effectively.
Remote monitoring systems enable engineers to monitor equipment performance and diagnose problems remotely, reducing response times and minimizing downtime. These systems utilize sensors, communication technologies, and data analysis to provide real-time information about equipment status and performance. By remotely accessing this information, engineers can make informed decisions and take immediate action, even if they are not physically present at the equipment's location.
In conclusion, preventative maintenance encompasses a range of activities aimed at preventing equipment failures. By understanding the key concepts and utilizing both basic and advanced techniques, specifying engineers can ensure the reliability, performance, and longevity of vital water industry assets.
The Role of Specifying Engineers in Preventative Maintenance
Specifying engineers play a vital role in the successful implementation of preventative maintenance programs in the water industry. Their expertise in system design, specifications, and maintenance planning enables them to optimize the reliability, performance, and longevity of equipment and systems.
When it comes to preventative maintenance, specifying engineers have a range of responsibilities. They are not only involved in the design of water industry systems but also ensure that these systems are designed with maintenance in mind. This means that they carefully consider factors such as easy access, inspection, and maintenance activities. By incorporating these considerations into the design process, specifying engineers make it easier for maintenance personnel to carry out their tasks effectively and efficiently.
Another crucial responsibility of specifying engineers is the selection of components and materials that are durable and easy to maintain. They carefully evaluate various options and choose those that not only meet the performance requirements but also have a long lifespan and require minimal maintenance. This selection process involves extensive research, testing, and collaboration with suppliers to ensure that the chosen components and materials are of the highest quality.
In addition to designing systems and selecting components, specifying engineers also collaborate with stakeholders to develop preventative maintenance schedules, procedures, and documentation. They work closely with maintenance teams, operations managers, and other relevant parties to create comprehensive maintenance plans that address all the necessary tasks and intervals. These plans outline the specific maintenance activities, such as inspections, lubrication, calibration, and replacements, that need to be carried out to ensure the optimal functioning of the equipment and systems.
Skills Required for Effective Maintenance Planning
Effective maintenance planning requires a diverse skill set from specifying engineers. They need to have a deep understanding of water industry processes and equipment to accurately assess maintenance requirements. This knowledge allows them to identify potential issues and develop strategies to prevent equipment failures and system breakdowns.
Furthermore, specifying engineers must stay updated with the latest maintenance best practices and regulations. They need to be aware of industry standards and guidelines to ensure that their maintenance plans comply with the necessary requirements. This involves continuous learning and professional development to stay ahead of technological advancements and changes in regulations.
Strong analytical and problem-solving skills are essential for specifying engineers involved in maintenance planning. They need to be able to analyze data, identify patterns, and make informed decisions regarding maintenance strategies. By leveraging their analytical skills, specifying engineers can optimize maintenance schedules, prioritize critical tasks, and allocate resources effectively.
Effective communication skills are crucial for specifying engineers as they collaborate with other departments, contractors, and suppliers. They need to clearly communicate maintenance requirements, expectations, and timelines to ensure smooth coordination and execution of maintenance activities. Additionally, they must be able to effectively convey technical information to non-technical stakeholders, such as management and operations teams, to gain their support and understanding.
In conclusion, specifying engineers play a vital role in preventative maintenance in the water industry. Their expertise in system design, specifications, and maintenance planning allows them to optimize the reliability, performance, and longevity of equipment and systems. By considering maintenance during the design process, selecting durable components, and developing comprehensive maintenance plans, specifying engineers contribute to the overall success of preventative maintenance programs.
Tools and Technologies for Preventative Maintenance
Various tools and technologies are available to assist specifying engineers in executing preventative maintenance tasks more efficiently and effectively.
Essential Tools for Maintenance
Specifying engineers should have access to a comprehensive set of tools to perform maintenance tasks. These may include instruments for measuring pressure, temperature, and flow rates, as well as tools for equipment calibration, lubrication, and cleaning. Furthermore, computerized maintenance management systems (CMMS) can help streamline maintenance processes, track equipment history, schedule maintenance activities, and generate reports.
Emerging Technologies in Maintenance Management
The field of maintenance management is evolving rapidly with the introduction of cutting-edge technologies. Internet of Things (IoT) devices, for example, enable real-time monitoring of equipment performance and condition. Artificial intelligence (AI) and machine learning algorithms can analyze vast amounts of data to identify patterns and predict maintenance needs. Augmented reality (AR) and virtual reality (VR) technologies offer new training and troubleshooting possibilities. By staying up-to-date with these emerging technologies, specifying engineers can leverage their potential to drive advancements in preventative maintenance practices.
Developing a Preventative Maintenance Plan
A well-documented preventative maintenance plan is crucial for specifying engineers to ensure consistency and effectiveness in their maintenance efforts.
Steps to Create a Maintenance Plan
The first step in creating a maintenance plan is to assess the assets and systems that require maintenance. This involves identifying critical equipment, determining maintenance frequency, and establishing performance metrics. Once the assets are identified, specifying engineers can develop detailed maintenance procedures, including inspection checklists, lubrication guidelines, and replacement schedules. Clear documentation of the plan ensures that maintenance tasks are carried out consistently and accurately.
Evaluating and Updating Your Maintenance Plan
Periodic evaluation of the maintenance plan is crucial to ensure its ongoing relevance and effectiveness. Specifying engineers should review equipment performance data, maintenance records, and feedback from maintenance personnel to identify areas for improvement. By analyzing this information, they can make informed decisions about adjustments to the plan, such as optimizing maintenance intervals or incorporating new technologies. Continuous evaluation and updating of the maintenance plan enable specifying engineers to optimize performance, reduce costs, and stay ahead of potential equipment failures.
Overcoming Challenges in Preventative Maintenance
Implementing and maintaining a preventative maintenance program in the water industry is not without its challenges. Specifying engineers need to be aware of common obstacles and employ effective strategies to address them.
Common Obstacles in Implementing Maintenance Plans
Resistance to change, limited resources, and competing priorities are common obstacles faced when implementing maintenance plans. Resistance to change can be overcome through effective communication and training programs, which educate stakeholders about the benefits of preventative maintenance. Limited resources, such as budget constraints, can be addressed by prioritizing critical assets and leveraging cost-effective maintenance technologies. By aligning maintenance goals with overall organizational objectives, specifying engineers can address competing priorities and garner support for maintenance initiatives.
Strategies to Address Maintenance Challenges
Addressing maintenance challenges requires a proactive and systematic approach. Providing comprehensive training for maintenance personnel equips them with the necessary skills to carry out maintenance tasks effectively. Regular communication and collaboration with stakeholders foster a culture of accountability and engagement. Leveraging data analytics and advanced technologies enables specifying engineers to detect potential issues early, optimize maintenance resources, and streamline maintenance processes. By applying these strategies, specifying engineers can overcome maintenance challenges and ensure the long-term success of preventative maintenance programs.
The Future of Preventative Maintenance in the Water Industry
The water industry is poised for significant advancements in preventative maintenance practices. Specifying engineers must be prepared for emerging trends that will shape the future of maintenance in this industry.
Trends Shaping Preventative Maintenance
One major trend is the increasing integration of IoT devices and sensors, which will enable real-time monitoring of equipment performance and condition. This data-driven approach will allow for more accurate predictions of maintenance needs and optimization of maintenance schedules. Additionally, advances in AI and machine learning will revolutionize maintenance practices by automating processes, identifying patterns, and enabling predictive maintenance. Augmented reality and virtual reality technologies will play a crucial role in training and assisting maintenance personnel. By embracing these trends, specifying engineers can harness the full potential of technology to enhance maintenance practices in the water industry.
Preparing for Future Maintenance Needs
As the water industry continues to evolve, specifying engineers must stay updated with the latest industry developments and emerging technologies. Continuous professional development ensures that engineers have the necessary knowledge and skills to adapt to changing maintenance needs. By actively engaging in industry forums, conferences, and networking opportunities, specifying engineers can stay informed about emerging trends and collaborate with experts in the field. Proactively preparing for future maintenance needs positions specifying engineers to lead in the implementation of innovative maintenance strategies and technologies.
In Conclusion
Preventative maintenance is crucial for specifying engineers in the water industry to ensure the reliability, performance, and longevity of equipment and systems. By understanding the importance of preventative maintenance, grasping key concepts, leveraging tools and technologies, developing effective maintenance plans, overcoming challenges, and staying prepared for the future, specifying engineers can optimize maintenance efforts and contribute to the continuous improvement of the water industry.