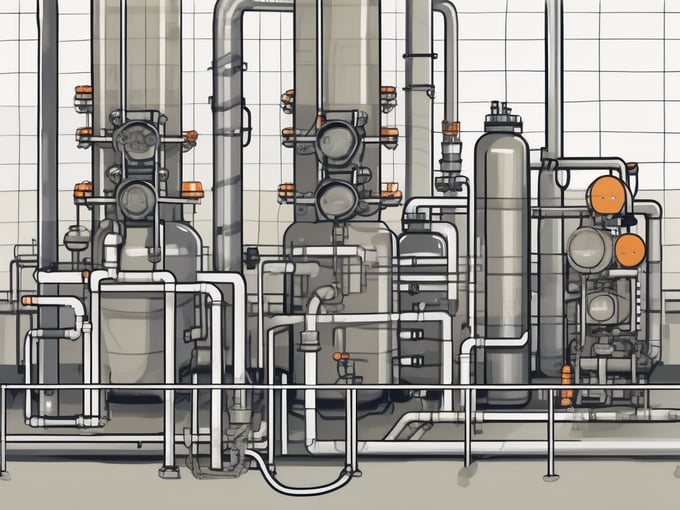
The Ultimate Guide to Preventative Maintenance for Technicians in the Sludge Management Industry
As a technician in the sludge management industry, understanding the importance of preventative maintenance is crucial for ensuring the efficient and safe operation of equipment. By adhering to key principles and implementing proper maintenance procedures, you can mitigate potential issues and extend the lifespan of your equipment.
Understanding Preventative Maintenance
Preventative maintenance refers to the proactive approach of regularly inspecting, cleaning, and servicing equipment to prevent breakdowns and costly repairs. In the sludge management industry, where equipment is subject to harsh conditions and heavy usage, preventative maintenance plays a vital role in ensuring the smooth operation of vital systems.
Sludge management is a critical aspect of wastewater treatment plants. It involves the proper handling and disposal of residual solids that are left behind after the treatment process. The equipment used in sludge management, such as pumps, mixers, and dewatering systems, are subjected to extreme conditions, including corrosive substances and high temperatures. Without proper maintenance, these systems can experience frequent breakdowns, leading to disruptions in the treatment process and potential environmental hazards.
The Importance of Preventative Maintenance in Sludge Management
Preventative maintenance is vital in the sludge management industry for several reasons. Firstly, it helps identify potential issues before they escalate into major problems, reducing downtime and costly repairs. By regularly inspecting equipment, technicians can detect early signs of wear, corrosion, or malfunctioning components. This proactive approach allows for timely repairs or replacements, preventing unexpected breakdowns that could halt the entire sludge management process.
Secondly, preventative maintenance ensures equipment is operating at peak efficiency, reducing energy consumption and minimizing environmental impact. Sludge management systems are energy-intensive, and any inefficiencies can result in increased energy usage and higher operational costs. Regular cleaning, lubrication, and calibration of equipment can optimize their performance, leading to significant energy savings and a reduced carbon footprint.
Lastly, by adhering to a proactive maintenance strategy, you can ensure the safety of operators and technicians. Sludge management equipment can be hazardous to work with, especially when not properly maintained. Malfunctioning parts or faulty safety mechanisms can put workers at risk of accidents or injuries. Regular inspections and maintenance procedures help identify and rectify potential safety hazards, creating a safer working environment for everyone involved.
Key Principles of Preventative Maintenance
When implementing a preventative maintenance program in sludge management, several key principles should guide your approach. Firstly, establish a regular inspection schedule to identify and address any signs of wear or damage. This schedule should consider the specific requirements of each equipment type, taking into account factors such as usage intensity and manufacturer recommendations. By conducting routine inspections, you can catch potential issues early on and take appropriate action to prevent further damage.
Additionally, create a comprehensive checklist for routine maintenance checks to ensure no important steps are missed. This checklist should cover all necessary tasks, such as cleaning filters, lubricating moving parts, and testing safety features. By following a standardized checklist, technicians can perform maintenance procedures consistently and thoroughly, reducing the risk of oversight or negligence.
Moreover, prioritize the use of OEM (Original Equipment Manufacturer) parts and follow manufacturer guidelines for maintenance procedures. OEM parts are specifically designed for the equipment and have been tested for compatibility and performance. Using genuine parts ensures optimal functionality and extends the lifespan of the equipment. Additionally, following manufacturer guidelines for maintenance procedures guarantees that you are performing the necessary tasks correctly, avoiding any potential damage caused by improper maintenance practices.
Lastly, maintain accurate maintenance records to track repairs, replacements, and identify trends or recurring issues. Keeping detailed records allows you to monitor the history of each piece of equipment, including past maintenance activities and any problems encountered. By analyzing this data, you can identify patterns or recurring issues, enabling you to take proactive measures to prevent future problems. Maintenance records also serve as a valuable resource for audits, compliance checks, and warranty claims.
Essential Tools and Equipment for Preventative Maintenance
Equipping technicians with the right tools and equipment is crucial for effective preventative maintenance in the sludge management industry. Without the proper gear, technicians may face challenges in ensuring the smooth operation of equipment and preventing potential issues from escalating.
When it comes to performing preventative maintenance in the sludge management industry, safety should always be a top priority. Technicians must be equipped with the necessary personal protective equipment (PPE) to safeguard themselves from potential hazards that they may encounter during their work.
Safety Gear for Technicians
Personal protective equipment (PPE) is of utmost importance for technicians working in the sludge management industry. This includes gloves, safety goggles, respirators, and protective clothing to protect against potential hazards, such as exposure to harmful chemicals or contaminants.
Gloves are essential for technicians as they provide a barrier between their hands and any potentially harmful substances they may come into contact with. Safety goggles protect their eyes from splashes or airborne particles that could cause injury or irritation. Respirators are crucial for filtering out harmful fumes or gases that may be present in the sludge management environment. Additionally, protective clothing, such as coveralls or aprons, helps to prevent any contaminants from coming into direct contact with the technician's skin or clothing.
By providing technicians with the necessary safety gear, companies can ensure that their employees are protected and minimize the risk of accidents or injuries in the workplace.
Maintenance Tools and Their Uses
Various maintenance tools are essential for performing routine checks and servicing equipment. These tools enable technicians to identify potential issues, make necessary adjustments, and ensure that equipment is functioning optimally.
Wrenches are commonly used tools in preventative maintenance. They come in different sizes and types, such as adjustable wrenches or socket wrenches, and are used to tighten or loosen bolts and nuts. Screwdrivers are another essential tool, allowing technicians to remove or fasten screws during equipment maintenance.
Lubrication equipment, such as grease guns or oil dispensers, are crucial for ensuring that moving parts are properly lubricated. This helps to reduce friction and wear, extending the lifespan of equipment and preventing breakdowns. Pressure gauges are used to measure and monitor pressure levels, allowing technicians to identify any abnormalities that may indicate a potential issue.
In addition to these basic tools, diagnostic tools play a significant role in preventative maintenance. These tools, such as multimeters or thermal imaging cameras, enable technicians to assess the performance of electrical systems or identify any anomalies that may not be visible to the naked eye.
Each tool serves a specific purpose and should be used according to manufacturer guidelines. Proper training and familiarization with these tools are essential to ensure that technicians can effectively carry out their maintenance tasks.
By equipping technicians with the necessary maintenance tools, companies can empower their workforce to perform preventative maintenance with precision and efficiency. This, in turn, helps to minimize downtime, reduce repair costs, and prolong the lifespan of equipment in the sludge management industry.
Maintenance Procedures and Protocols
Implementing standardized maintenance procedures and protocols is crucial for effective preventative maintenance. This ensures consistency and ensures that no vital steps are overlooked.
When it comes to maintaining equipment in the sludge management industry, routine maintenance checks are essential. Regular inspections are conducted to identify any signs of wear, damage, or potential problems with the equipment. These inspections involve a range of activities, including visual inspections, checking fluid levels and pressure, ensuring proper connections, and cleaning or replacing filters as needed.
Visual inspections play a significant role in routine maintenance checks. Technicians carefully examine the equipment, looking for any visible signs of wear or damage. They inspect the outer casing, components, and connections to ensure everything is in proper working condition. This meticulous examination helps identify potential issues before they escalate into major problems.
Fluid levels and pressure are critical factors to monitor during maintenance checks. Technicians carefully measure and assess the levels of various fluids, such as oil, coolant, or hydraulic fluid, depending on the equipment. They also check the pressure levels to ensure they are within the specified range. Any abnormalities in fluid levels or pressure can indicate a potential issue that needs to be addressed promptly.
Proper connections are vital for the safe and efficient operation of equipment. During routine maintenance checks, technicians inspect all connections, including electrical, hydraulic, and mechanical connections. They ensure that all connections are secure, free from corrosion, and functioning correctly. Any loose or faulty connections are immediately rectified to prevent equipment malfunction or accidents.
In addition to visual inspections and checking fluid levels and connections, cleaning and replacing filters are also part of routine maintenance checks. Filters play a crucial role in removing impurities and contaminants from the equipment's fluids or air. Technicians clean or replace filters as needed to maintain optimal performance and prevent any potential damage caused by clogged or dirty filters.
Maintenance Protocols for Different Equipment
Each equipment in the sludge management industry requires specific maintenance protocols. These protocols are tailored to the unique characteristics and requirements of each equipment type.
Cleaning and flushing procedures are essential maintenance protocols for many types of equipment. These procedures involve thoroughly cleaning the equipment to remove any accumulated dirt, debris, or sludge. Flushing procedures are often employed to remove any residual contaminants or build-up from the internal components of the equipment. These cleaning and flushing protocols help maintain the efficiency and longevity of the equipment.
Lubrication schedules are another critical aspect of maintenance protocols. Proper lubrication ensures smooth operation and reduces friction between moving parts. Technicians follow specific schedules to apply the appropriate lubricants to the equipment's various components. This helps prevent excessive wear and tear and extends the equipment's lifespan.
Calibration checks are necessary for equipment that relies on precise measurements or controls. Technicians perform regular calibration checks to ensure that the equipment's sensors, gauges, or control systems are accurately measuring and controlling the desired parameters. Calibration checks help maintain the equipment's accuracy and reliability, ensuring optimal performance.
Some equipment in the sludge management industry may require prescribed testing or analysis as part of their maintenance protocols. This can involve conducting various tests to assess the equipment's performance, efficiency, or safety. Technicians follow specific testing procedures and analyze the results to identify any potential issues or areas for improvement.
In conclusion, implementing standardized maintenance procedures and protocols is crucial for effective preventative maintenance in the sludge management industry. Routine maintenance checks, tailored maintenance protocols for different equipment, and adherence to these protocols ensure the equipment's optimal performance, longevity, and safety.
Troubleshooting Common Issues
Despite diligent preventative maintenance efforts, equipment issues can still arise. It is essential for technicians to be equipped with troubleshooting skills to effectively identify and resolve common problems.
Identifying Common Problems in Sludge Management Equipment
Familiarize yourself with the most common issues that could occur in sludge management equipment, such as clogs, leaks, or faulty sensors. Developing a comprehensive understanding of these issues will aid in quick and accurate troubleshooting.
One common problem that technicians often encounter in sludge management equipment is clogs. These clogs can occur due to a build-up of solid waste material, which can hinder the proper functioning of the equipment. To identify a clog, technicians need to carefully inspect the equipment and look for any signs of blockage, such as reduced flow or abnormal noises. Once a clog is identified, technicians can then proceed with the appropriate steps to remove it and restore the equipment's functionality.
In addition to clogs, leaks are another common issue that technicians may face when dealing with sludge management equipment. Leaks can occur due to various reasons, such as damaged seals or connections. To identify a leak, technicians need to visually inspect the equipment and look for any signs of fluid leakage, such as puddles or damp areas. Once a leak is identified, technicians can then proceed with the necessary repairs or replacements to prevent further damage and ensure the equipment operates efficiently.
Faulty sensors are also a frequent problem in sludge management equipment. These sensors play a crucial role in monitoring and controlling various parameters, such as pressure or temperature. When a sensor malfunctions, it can lead to inaccurate readings or even equipment failure. To identify a faulty sensor, technicians need to perform diagnostic tests using specialized equipment or consult the equipment's manual for guidance. Once a faulty sensor is identified, technicians can then proceed with the appropriate steps to repair or replace it, ensuring the equipment operates reliably.
Steps for Effective Troubleshooting
When troubleshooting equipment, it is crucial to follow a systematic approach. Start by gathering as much information as possible about the problem, such as error codes or unusual behavior. This information can provide valuable insights into the potential causes of the issue.
Next, technicians should refer to equipment manuals or consult with experienced technicians to identify potential causes and solutions. These resources can provide valuable guidance and help narrow down the possible reasons for the problem. By leveraging the knowledge and expertise of others, technicians can save time and ensure a more accurate troubleshooting process.
Once potential causes have been identified, technicians should proceed with testing and verifying each one. This involves systematically checking each potential cause and observing the equipment's response. By conducting these tests, technicians can confirm or eliminate potential causes until the issue is resolved.
Throughout the troubleshooting process, it is important for technicians to document their findings, including the steps taken and the results obtained. This documentation can serve as a valuable reference for future troubleshooting efforts and can also be shared with other technicians or equipment manufacturers for further assistance if needed.
In conclusion, troubleshooting common issues in equipment requires a combination of knowledge, experience, and a systematic approach. By familiarizing themselves with common problems and following a structured troubleshooting process, technicians can effectively identify and resolve issues, ensuring the smooth operation of sludge management equipment.
Maintenance Scheduling and Planning
Creating an effective maintenance schedule and plan is key to ensuring that preventative maintenance tasks are carried out consistently and proactively.
Creating an Effective Maintenance Schedule
Establish a maintenance schedule that takes into account the manufacturer's recommendations, equipment usage patterns, and any specific factors unique to your facility. This schedule should clearly outline the frequency of maintenance tasks, including routine checks, cleaning, lubrication, and scheduled replacements.
Importance of Regular Maintenance Planning
Regular maintenance planning is essential for maximizing the effectiveness of preventative maintenance. This involves coordinating maintenance tasks with production schedules, ensuring availability of necessary resources and parts, and communicating planned maintenance with relevant stakeholders to minimize any disruptions.
Training and Skill Development for Technicians
Continuous training and skill development are vital for technicians in the sludge management industry to keep up with evolving technologies and industry best practices.
Essential Skills for Sludge Management Technicians
Technicians should possess a strong understanding of the equipment they work with, as well as the knowledge and skills required to perform routine maintenance tasks. This includes familiarity with safety protocols, troubleshooting techniques, usage of tools and equipment, and interpreting technical manuals and diagrams.
Ongoing Training and Development Opportunities
Encourage technicians to participate in training programs, workshops, and industry conferences to stay updated with the latest advancements in sludge management technology and maintenance practices. Invest in their professional development to ensure they can adapt to changes and perform their job effectively.
The Future of Preventative Maintenance in Sludge Management
The future of preventative maintenance in the sludge management industry holds exciting possibilities, driven by technological advancements and a growing focus on sustainability.
Technological Advancements in Maintenance
Emerging technologies, such as real-time monitoring systems, predictive analytics, and remote diagnostics, are transforming the way maintenance is performed. These advancements enable technicians to detect equipment issues before they become critical, optimize maintenance schedules, and improve overall equipment performance.
Sustainability and Preventative Maintenance
As the sludge management industry emphasizes sustainable practices, preventative maintenance plays a vital role in minimizing environmental impact. By ensuring equipment operates efficiently and safely, preventative maintenance contributes to reducing energy consumption, minimizing waste generation, and promoting a more sustainable approach to sludge management.
In conclusion, preventative maintenance is essential for technicians working in the sludge management industry to ensure equipment operates efficiently, reduce downtime, and mitigate potential issues. By adhering to key principles, using the right tools, following maintenance procedures, and continuously developing skills, technicians can play a crucial role in maintaining the effective and environmentally conscious operation of sludge management equipment.