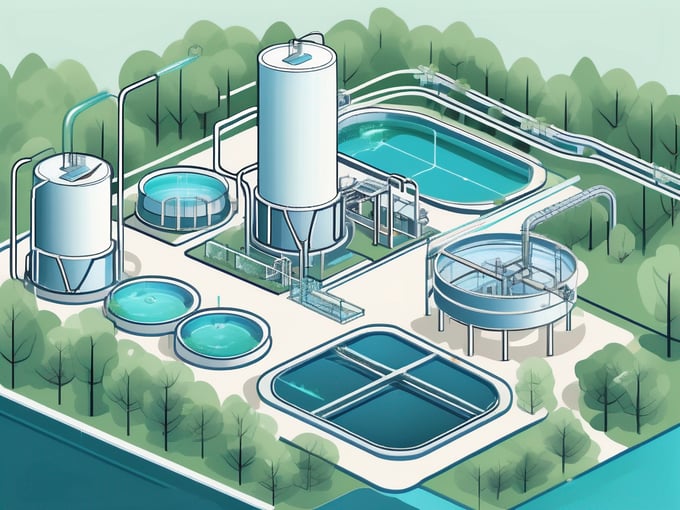
Automation has revolutionized various industries, including the water treatment sector. With advancements in technology, water treatment plants can now operate more efficiently and effectively, ensuring the delivery of clean and safe water to communities. In this comprehensive guide, we will explore the basics of automation in the water industry, the role of plant operators in automated systems, the implementation of automation in existing water plants, the benefits it brings, the challenges faced, and the future trends in water plant automation.
Understanding the Basics of Automation in the Water Industry
The water industry is constantly evolving, and one of the key advancements in recent years has been the implementation of automation. Automation in the water industry refers to the use of technology and control systems to monitor and regulate various processes in water treatment plants. It involves the integration of sensors, actuators, and programmable logic controllers (PLCs) to streamline and optimize plant operations.
Defining automation in the water industry is just the beginning. It's important to understand why automation is crucial in water treatment and the key components that make up an automated water treatment plant.
Defining Automation in the Water Industry
Automation in the water industry refers to the use of advanced technologies and control systems to monitor and regulate various processes in water treatment plants. These processes include filtration, disinfection, chemical dosing, and distribution. By automating these processes, water treatment plants can operate more efficiently and effectively.
Automation involves the integration of various components, including sensors, actuators, and programmable logic controllers (PLCs). These components work together to collect data, analyze it, and make necessary adjustments to ensure optimal performance.
The Importance of Automation in Water Treatment
Automation plays a vital role in water treatment by enhancing efficiency, reducing errors, and ensuring consistent compliance with regulatory standards. With automation, water treatment plants can achieve real-time monitoring, remote operation, and data-driven decision-making, leading to improved water quality and customer satisfaction.
One of the key benefits of automation is its ability to enhance efficiency. By automating processes such as chemical dosing and filtration, water treatment plants can minimize human error and ensure consistent and accurate results. This not only saves time and resources but also improves the overall quality of the treated water.
Automation also enables water treatment plants to comply with regulatory standards more effectively. By continuously monitoring and adjusting various parameters, such as pH, turbidity, and chlorine levels, automation ensures that the treated water meets the required quality standards. This helps to protect public health and maintain the integrity of the water supply.
Key Components of an Automated Water Treatment Plant
An automated water treatment plant consists of several key components that work together to ensure efficient and reliable operation.
The first component is sensors. Sensors are used to measure various parameters, such as pH, turbidity, and chlorine levels, in the water. These sensors provide real-time data that is essential for monitoring and controlling the treatment process.
The second component is actuators. Actuators are devices that control valves, pumps, and other equipment in the treatment plant. By receiving signals from the control system, actuators can adjust the flow rate, pressure, and other parameters to maintain optimal conditions.
The third component is programmable logic controllers (PLCs). PLCs are the brains of the automation system. They receive data from the sensors, process it, and execute commands to control the actuators. PLCs can be programmed to perform complex calculations and make decisions based on predefined rules.
Finally, a supervisory control and data acquisition (SCADA) system is used for centralized monitoring and control. The SCADA system collects data from the sensors and PLCs, displays it in a user-friendly interface, and allows operators to monitor and control the treatment process from a central location.
By integrating these key components, an automated water treatment plant can operate efficiently, ensure consistent water quality, and minimize the risk of human error.
The Role of Plant Operators in Automated Systems
Automation has become increasingly prevalent in water treatment plants, revolutionizing the way operations are conducted. As these plants transition from manual to automated operations, the role of plant operators has evolved to adapt to the changing technological landscape.
Proper training and education are crucial for plant operators to effectively manage automated systems. They must understand the principles of automation and become familiar with the sensors and control devices that are integral to these systems. Additionally, operators need to learn how to interpret and respond to the vast amount of data generated by the automation system.
Skills Required for Operating Automated Systems
Operating in an automated environment requires plant operators to possess a diverse range of skills to ensure the smooth functioning of the plant. Technical expertise in instrumentation and control systems is essential, as operators need to be proficient in operating and troubleshooting these complex systems.
Furthermore, the ability to analyze and interpret data is crucial for operators to make informed decisions and optimize plant performance. They must be able to identify trends, detect anomalies, and take appropriate actions based on the insights derived from the data.
Communication and collaboration skills are also of utmost importance for plant operators in automated environments. They often need to coordinate with other departments and stakeholders, such as maintenance teams, engineers, and management, to ensure seamless operations and address any issues that may arise.
Responsibilities of Plant Operators in Automated Environments
Plant operators play a critical role in maintaining the functionality and efficiency of automated water treatment systems. Their responsibilities encompass a wide range of tasks that are essential for the smooth operation of the plant.
Regular monitoring of process parameters is one of the primary responsibilities of plant operators. They must continuously monitor various parameters such as flow rates, pressure levels, and chemical dosages to ensure that the plant is operating within the desired parameters.
Calibration of sensors and control devices is another important task that operators need to perform regularly. Accurate calibration is crucial for obtaining reliable data and ensuring the proper functioning of the automation system.
In the event of equipment malfunctions, plant operators are responsible for troubleshooting and resolving the issues. They must possess the technical knowledge and problem-solving skills to identify the root cause of the problem and implement appropriate corrective measures.
Preventive maintenance tasks are also part of the operator's responsibilities. This includes routine inspections, cleaning, and servicing of equipment to prevent potential failures and ensure the longevity of the plant's assets.
Operators must also be vigilant and responsive to alarms generated by the automation system. Promptly responding to alarms and taking appropriate actions is crucial to prevent any disruptions in plant operations and maintain the desired water quality.
In conclusion, the role of plant operators in automated systems is multifaceted and demanding. They must possess technical expertise, analytical skills, and effective communication abilities to effectively manage and optimize the performance of automated water treatment plants.
Implementing Automation in Existing Water Plants
Automation has become an increasingly popular solution for improving the efficiency and effectiveness of water treatment plants. By implementing automated systems, water plants can streamline their operations, enhance control and monitoring capabilities, and ultimately provide better quality water to their communities. In this article, we will explore the process of implementing automation in existing water plants, from evaluating the need for automation to the installation and testing of automated equipment.
Evaluating the Need for Automation
Before embarking on the journey of automation, it is crucial to evaluate the need for it in an existing water treatment plant. Several factors must be considered during this evaluation process. Firstly, the size of the plant plays a significant role in determining the feasibility of automation. Larger plants with complex operations may benefit more from automation compared to smaller plants with simpler processes.
Additionally, the scope of operations should be taken into account. Water treatment plants that handle multiple processes, such as filtration, disinfection, and chemical dosing, may find automation particularly advantageous. On the other hand, plants with limited operations may not require extensive automation.
Regulatory requirements also play a crucial role in the decision-making process. Compliance with regulations is essential for water treatment plants, and automation can help ensure that all necessary standards are met consistently. By automating certain processes, plants can minimize the risk of human error and ensure compliance with regulatory guidelines.
Lastly, budget considerations are vital when evaluating the need for automation. Implementing automated systems can require a significant investment, including the cost of equipment, installation, and training. Therefore, it is essential to assess the financial feasibility of automation and determine whether the long-term benefits outweigh the initial costs.
Planning and Designing Automated Systems
Once the decision to implement automation has been made, the planning and design phase comes into play. This phase involves careful consideration of the specific automation requirements and the selection of appropriate technologies that align with the plant's needs.
During this phase, it is crucial to involve plant operators and other stakeholders. Their insights and expertise can provide valuable input in identifying the areas that would benefit most from automation. By involving them in the planning and design process, the automated system can be tailored to meet the operational needs and address any concerns or challenges that may arise.
Furthermore, integrating the selected automation technologies into the existing plant infrastructure requires careful planning. Compatibility with the current systems, such as SCADA (Supervisory Control and Data Acquisition) and PLCs (Programmable Logic Controllers), should be ensured. This integration process may involve retrofitting existing equipment or installing new components to enable seamless communication and control between different parts of the plant.
Installation and Testing of Automated Equipment
With the design finalized, the installation of automated equipment can begin. This phase involves integrating various components, such as sensors, actuators, PLCs, and the SCADA system, into the existing plant infrastructure.
Rigorous testing and commissioning should be conducted to verify the reliability and functionality of the automated system. This testing phase ensures that the system operates as intended and meets the desired objectives. It involves simulating different scenarios and evaluating the system's response to various inputs and conditions.
During the testing phase, any issues or glitches that arise should be addressed promptly to ensure the system's optimal performance. Regular maintenance and calibration of the automated equipment are also essential to guarantee its long-term reliability and accuracy.
In conclusion, implementing automation in existing water treatment plants requires careful evaluation, planning, and design. By considering factors such as plant size, scope of operations, regulatory requirements, and budget, water plants can determine the need for automation and assess its feasibility. The involvement of plant operators and stakeholders during the planning and design phase ensures that the automated system aligns with operational needs. Finally, the installation and testing of automated equipment, followed by regular maintenance, guarantees the reliability and effectiveness of the automated system. With automation, water treatment plants can enhance their operations, improve water quality, and better serve their communities.
Benefits of Automation in the Water Industry
The water industry plays a crucial role in ensuring the availability of clean and safe water for various purposes, including drinking, agriculture, and industrial use. With the advancement of technology, automation has emerged as a powerful tool in improving the efficiency, productivity, and overall performance of the water industry. Let's explore some of the key benefits of automation in this sector.
Improving Efficiency and Productivity
Automation enhances operational efficiency and productivity by reducing manual intervention and minimizing human errors. By automating various processes, such as water treatment, distribution, and monitoring, organizations can streamline their operations and achieve higher levels of efficiency. With automation, processes can be optimized, and resources can be utilized more effectively, leading to cost savings and increased output.
For example, automated systems can continuously monitor water flow rates, pressure levels, and chemical dosages, ensuring that the treatment process is optimized for maximum efficiency. By eliminating the need for manual adjustments, automation reduces the chances of human errors and ensures consistent and reliable water treatment.
Enhancing Water Quality and Safety
Automation plays a crucial role in improving water quality and safety by enabling real-time monitoring of critical parameters and rapid response to deviations. Traditional manual monitoring methods often rely on periodic sampling and laboratory testing, which may not provide timely information about water quality issues.
By contrast, automated systems can continuously monitor various parameters, such as pH levels, turbidity, chlorine levels, and microbial contamination. In case of any deviations from the desired levels, automated systems can trigger alarms and take corrective actions promptly. This ensures that water meets regulatory standards and is safe for consumption.
Furthermore, automation allows for the integration of advanced technologies, such as remote sensing and data analytics, which can provide deeper insights into water quality trends and potential risks. By leveraging these technologies, organizations can proactively identify and address water quality issues before they become significant problems.
Reducing Operational Costs
Automation reduces operational costs in several ways. By optimizing processes, energy consumption can be minimized, resulting in lower utility bills. For example, automated control systems can adjust pump speeds and valve positions based on real-time demand, ensuring that energy is used efficiently.
Additionally, automation reduces the need for manual labor, leading to reduced staffing requirements. With automated systems taking care of routine tasks, employees can focus on more value-added activities, such as maintenance and troubleshooting. This not only improves overall productivity but also enhances job satisfaction among employees.
Moreover, preventive maintenance can be scheduled more efficiently with automation. By continuously monitoring equipment performance and predicting potential failures, organizations can plan maintenance activities proactively, reducing downtime and repair costs. This proactive approach also extends the lifespan of equipment, further contributing to cost savings.
In conclusion, automation brings numerous benefits to the water industry, including improved efficiency, enhanced water quality and safety, and reduced operational costs. As technology continues to advance, the potential for automation in this sector is vast, promising a more sustainable and reliable water supply for all.
Challenges and Solutions in Water Plant Automation
Overcoming Technical Difficulties
Implementing automation in water plants can present technical challenges, such as system integration issues, compatibility problems, and software bugs. These difficulties can be overcome by thorough planning, engaging knowledgeable experts, conducting extensive testing, and having a contingency plan in place to address any potential issues.
Addressing Training and Skill Gaps
The transition to automated systems requires plant operators to acquire new skills and knowledge. Adequate training programs should be provided to bridge any skill gaps. Collaborating with educational institutions, industry associations, and automation solution providers can facilitate training and help operators stay updated with the latest advancements.
Ensuring System Security and Reliability
System security and reliability are paramount in water plant automation. Robust cybersecurity measures should be implemented to protect against potential threats and vulnerabilities. Regular system audits, data backups, and compliance with industry standards can help ensure system integrity and minimize the risk of cyberattacks.
Future Trends in Water Plant Automation
Advances in Automation Technology
The future of water plant automation holds exciting possibilities. Advancements in automation technology, such as machine learning and artificial intelligence, will enable more intelligent and adaptive systems. Predictive maintenance, anomaly detection, and advanced analytics will further optimize plant operations.
Impact of IoT and AI on Water Treatment Automation
The integration of the Internet of Things (IoT) and artificial intelligence (AI) will revolutionize water treatment automation. IoT devices and sensors will collect vast amounts of data, enabling real-time monitoring and analysis. AI algorithms will provide insights and recommendations for efficient operation, predictive maintenance, and optimal resource management.
Sustainability and Automation: The Way Forward
Sustainability will be a key focus in the future of water plant automation. Automated systems will enable improved water conservation, energy efficiency, and sustainable resource management. Water treatment plants will play a pivotal role in addressing global water scarcity and environmental challenges.
As automation continues to transform the water industry, plant operators must embrace the opportunities it brings. By understanding the basics of automation, acquiring the necessary skills, and adapting to changing technologies, operators can ensure the efficient and reliable operation of water treatment plants, ultimately contributing to a sustainable and resilient water supply for communities.