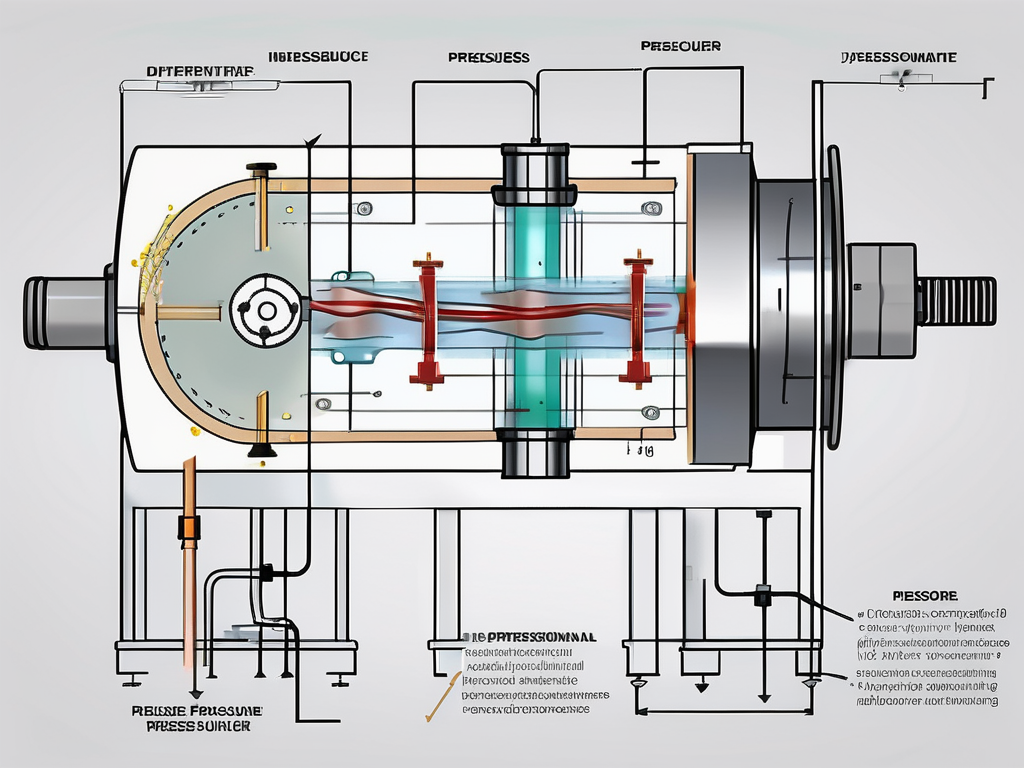
Understanding Differential Pressure Sensors: Applications and Benefits
Differential pressure sensors are a crucial component in various industries, providing critical data that enhances operational efficiency and safety. In this article, we will explore what these sensors are, their working mechanisms, applications, benefits, factors to consider when choosing one, and future trends in sensing technology.
What are Differential Pressure Sensors?
Definition and Basic Principles
Differential pressure sensors are devices designed to measure the difference in pressure between two points in a system. This difference can be indicative of flow rates, blockages, and various operational parameters within a system. The basic principle behind these sensors involves the conversion of mechanical pressure differences into electrical signals that can be analyzed and interpreted. These sensors are invaluable in numerous industries, including oil and gas, pharmaceuticals, and water treatment, where precise pressure measurements are crucial for operational efficiency and safety.
The measurement achieved through a differential pressure sensor is critical in applications where maintaining a specific pressure is essential, such as in pipelines, HVAC systems, and chemical processing. By understanding the variance in pressure, operators can make informed decisions about system performance and maintenance needs. For instance, in HVAC systems, differential pressure sensors help ensure optimal airflow and energy efficiency, while in chemical processing, they can prevent dangerous over-pressurization scenarios by providing real-time feedback on system conditions.
Key Components of Differential Pressure Sensors
There are several key components that make up a differential pressure sensor, including:
- Pressure Ports: The input gateways where the fluid or gas enters the sensor to create a pressure differential.
- Diaphragm: A flexible membrane that reacts to pressure changes, often connected to a sensing element.
- Sensing Element: Converts the mechanical movement of the diaphragm into an electrical signal.
- Transmitter: Converts the electrical signal into a format suitable for display or further processing.
Understanding these components is essential in recognizing how differential pressure sensors function and how to maintain them effectively. For example, the diaphragm's material selection is crucial; it must be compatible with the media being measured to avoid degradation over time. Additionally, the calibration of the sensing element is vital for ensuring accuracy, as even minor discrepancies can lead to significant errors in pressure readings. Regular maintenance checks can help identify wear and tear, ensuring that the sensors continue to operate within their specified parameters.
Moreover, advancements in technology have led to the development of smart differential pressure sensors that incorporate digital interfaces and wireless communication capabilities. These modern sensors can provide real-time data analytics, allowing for predictive maintenance and reducing downtime in industrial applications. By integrating these sensors with IoT platforms, operators can monitor system performance remotely, enabling quicker response times to any irregularities detected in pressure levels. This evolution in sensor technology not only enhances operational efficiency but also contributes to safer working environments across various sectors.
The Working Mechanism of Differential Pressure Sensors
Process of Measurement
The operational mechanism of a differential pressure sensor involves a systematic process. When pressure is applied at the two ports of the sensor, the diaphragm bends, causing a shift in the measurement. This bending generates a change in resistance or capacitance, which correlates to the pressure difference. The design of the diaphragm is critical; it is often made from materials that offer a balance between flexibility and durability, allowing it to respond accurately to varying pressure levels without succumbing to fatigue over time.
Once the diaphragm moves, the sensing element detects this change and converts it into an electrical signal. This signal may vary depending on the sensor design and can either be analog or digital. The processed signal is then transmitted to a control system or display device for interpretation and analysis, allowing users to monitor system parameters efficiently. In many modern applications, these sensors are integrated with advanced data processing units that can filter noise and enhance signal clarity, providing users with real-time data that is both accurate and actionable. This capability is particularly beneficial in industries such as HVAC, where maintaining optimal pressure levels is essential for system efficiency and safety.
Sensor Calibration and Maintenance
To ensure optimal performance, regular calibration and maintenance of differential pressure sensors are required. Calibration is the process of adjusting the sensor output to match known standards, ensuring accuracy in the measurements. This calibration should be performed periodically, especially in critical applications where precision is paramount. Advanced calibration techniques may involve the use of reference standards and specialized equipment to ensure that the sensor's readings align perfectly with the expected values, thereby minimizing any potential discrepancies.
In terms of maintenance, periodic inspections and cleaning of the pressure ports and sensing elements are recommended. Environmental factors may contribute to sensor degradation; hence maintaining a clean operating environment is crucial for longevity. Additionally, factors such as temperature fluctuations, humidity, and exposure to corrosive substances can affect sensor performance. Therefore, implementing a routine maintenance schedule that includes environmental assessments can significantly extend the operational life of the sensor. Throughout its lifetime, a well-maintained differential pressure sensor can provide reliable measurements and prevent costly operational failures, making it an invaluable component in various industrial processes, from chemical manufacturing to water treatment facilities.
Applications of Differential Pressure Sensors
Use in HVAC Systems
Differential pressure sensors play a vital role in the HVAC industry. They monitor air pressure differences across filters, ensuring optimal airflow and filter performance. By measuring the pressure drop caused by the accumulation of particles, these sensors can signal when filters need to be replaced, thus maintaining indoor air quality and energy efficiency.
Additionally, in heating and cooling systems, differential pressure sensors help automate the control of pumps and variable air volume systems, leading to energy savings and improved comfort for building occupants. The integration of these sensors with smart building technologies allows for real-time adjustments based on occupancy and environmental conditions, further enhancing energy efficiency. For instance, when a room is unoccupied, the system can reduce airflow, thereby conserving energy while still maintaining a comfortable environment for when the space is in use.
Role in Water Treatment Plants
In water treatment facilities, differential pressure sensors are essential for monitoring pressure differences in filtration systems and pumps. They help detect blockages and provide real-time data that is critical for ensuring that water is treated efficiently and effectively. These sensors enable operators to identify issues before they escalate, allowing for timely maintenance and reducing downtime.
Moreover, these sensors also provide data that can prevent over-pressurization in pipes, reducing the risk of pipe failure and enhancing the overall resilience of the water distribution infrastructure. By continuously monitoring pressure levels, facilities can optimize their chemical dosing processes, ensuring that water is treated with the right amount of chemicals, thus improving water quality while minimizing chemical waste. This not only supports regulatory compliance but also promotes sustainable practices within the facility.
Importance in Oil and Gas Industry
The oil and gas industry relies heavily on differential pressure sensors for safe and efficient operations. These sensors help monitor the pressure difference across various stages of the drilling, refining, and distribution processes. By providing critical data on the flow of fluids, they enable operators to make informed decisions that enhance productivity and safety.
By ensuring that the pressure remains within safe limits at various points, differential pressure sensors help prevent leaks, explosions, and other dangerous situations, thereby safeguarding both personnel and the environment. Furthermore, in offshore drilling operations, these sensors are crucial for maintaining the integrity of subsea pipelines and equipment, where pressure fluctuations can indicate potential failures. The ability to remotely monitor these conditions not only enhances safety but also reduces the need for costly and time-consuming inspections, ultimately leading to more efficient resource management and operational reliability.
Benefits of Using Differential Pressure Sensors
Accuracy and Precision
One of the most prominent benefits of differential pressure sensors is their high accuracy and precision. In industries where minute pressure differences can signify critical changes in operation, these sensors deliver reliable measurements.
When correctly calibrated and maintained, differential pressure sensors can provide real-time data that is essential for ensuring system integrity and performance, leading to better decision-making processes in industrial environments. For instance, in the pharmaceutical industry, maintaining precise pressure differentials is vital for ensuring the integrity of sterile environments. Any deviation can compromise product quality, making the role of these sensors indispensable. Moreover, their ability to detect even the slightest pressure changes can prevent costly downtime by alerting operators to potential issues before they escalate into serious problems.
Versatility and Flexibility
Differential pressure sensors offer versatility across various applications and industries. Their designs can adapt to different operating conditions, such as high temperatures and corrosive environments, making them suitable for a wide range of tasks.
With customizable configurations, these sensors can be tailored to meet specific measurement needs, empowering operators to tackle diverse challenges in their systems effectively. For example, in HVAC systems, differential pressure sensors are used to monitor airflow and ensure optimal performance. They can be configured to measure pressure drops across filters, helping to maintain energy efficiency and prolong the lifespan of equipment. Additionally, their adaptability allows them to be integrated into various control systems, enhancing automation and operational efficiency across industries such as oil and gas, water treatment, and food processing.
Durability and Longevity
The typical design of differential pressure sensors emphasizes durability. Built with robust materials, these sensors can withstand harsh conditions, whether in outdoor environments or sterile industrial settings.
A long lifespan reduces the need for frequent replacements, allowing companies to save on maintenance costs and focus their resources on other operational areas. When investing in differential pressure sensors, businesses often emphasize the return on investment due to their longevity and reliability. Furthermore, many modern sensors are designed with advanced features such as self-diagnostics and built-in alarms, which enhance their functionality and reliability. These features not only improve the sensors' performance but also provide peace of mind to operators, knowing that they can rely on their equipment to perform consistently, even in the most demanding conditions. This durability is particularly important in industries where equipment failure can lead to significant downtime and financial losses, making differential pressure sensors a critical component in maintaining operational continuity.
Choosing the Right Differential Pressure Sensor
Factors to Consider
When selecting a differential pressure sensor, several factors must be considered to ensure optimal performance:
- Measurement Range: Understand the pressure ranges that the sensor must operate within.
- Medium Being Measured: Consider whether the sensor will be used for gases or liquids and if these substances are corrosive.
- Accuracy Requirements: Determine the level of precision needed for your specific application.
- Environmental Conditions: Evaluate factors like temperature, humidity, and potential exposure to contaminants.
Taking the time to evaluate these aspects can lead to a more informed decision and better overall performance from the chosen sensor. Additionally, it is crucial to consider the installation environment. For example, sensors installed in industrial settings may face vibrations or electromagnetic interference, which could affect their performance. Therefore, choosing a sensor with robust housing and proper shielding can mitigate these risks. Furthermore, understanding the long-term operational costs, including maintenance and potential downtime, can also influence your choice, ensuring that the selected sensor not only meets immediate needs but is also sustainable over time.
Common Misconceptions and Pitfalls
There are several misconceptions surrounding differential pressure sensors that can lead to errors in application:
- Assuming All Sensors Are the Same: Not all differential pressure sensors are created equal. It's important to understand specific requirements before making a choice.
- Ignoring Calibration Needs: Some users may overlook the necessity of regular calibration, which can lead to inaccuracies over time.
- Neglecting Environmental Factors: Users often underestimate the impact of environmental conditions, leading to sensor failure.
Being aware of these potential pitfalls can ensure more efficient utilization of differential pressure sensors in various applications. Moreover, it is essential to recognize that the integration of these sensors into existing systems can pose challenges. For instance, compatibility with existing data acquisition systems or control software should be assessed to avoid integration issues. Additionally, users should be educated on the importance of sensor placement; improper positioning can lead to erroneous readings and ultimately affect system performance. By addressing these misconceptions and understanding the broader context of sensor application, users can maximize the effectiveness of their differential pressure sensors and enhance overall operational efficiency.
Future Trends in Differential Pressure Sensing Technology
Innovations and Developments
The field of differential pressure sensing technology is continually evolving. Innovations such as MEMS (Micro-Electro-Mechanical Systems) technology have paved the way for smaller, more sensitive sensors that are also cost-effective. Such advancements are transforming the landscape, making differential pressure sensors more accessible across numerous applications. These miniature sensors not only reduce the physical footprint of installations but also enhance the precision of measurements, which is crucial in industries like pharmaceuticals and aerospace where even the slightest pressure variation can lead to significant consequences.
Additionally, developments in materials science are leading to sensors that can operate in even more challenging environments, pushing the boundaries of where these tools can be utilized effectively. For instance, the introduction of advanced polymers and composites allows sensors to withstand extreme temperatures and corrosive substances, making them ideal for use in oil and gas exploration or chemical processing. This adaptability ensures that differential pressure sensors can meet the rigorous demands of modern industrial applications while maintaining reliability and accuracy.
Impact of IoT and AI on Pressure Sensing
The integration of IoT (Internet of Things) technology is changing how differential pressure sensors are utilized. Connected sensors can offer remote monitoring capabilities, sending real-time data to central systems for analysis. This connectivity not only facilitates immediate access to critical data but also enables the seamless integration of pressure sensing into larger automated systems, enhancing overall operational efficiency. For example, in smart buildings, differential pressure sensors can help regulate HVAC systems by adjusting airflow based on real-time occupancy and environmental conditions, leading to energy savings and improved comfort.
Furthermore, the application of AI (Artificial Intelligence) in data analysis can revolutionize predictive maintenance strategies. By employing sophisticated algorithms, companies can anticipate issues before they arise, minimizing downtime and optimizing workflow efficiency. AI-driven analytics can sift through vast amounts of sensor data to identify patterns and anomalies that may indicate potential failures. This proactive approach not only extends the lifespan of equipment but also significantly reduces maintenance costs, allowing organizations to allocate resources more effectively. As industries increasingly adopt these technologies, the role of differential pressure sensors will become even more critical in ensuring operational excellence and safety.