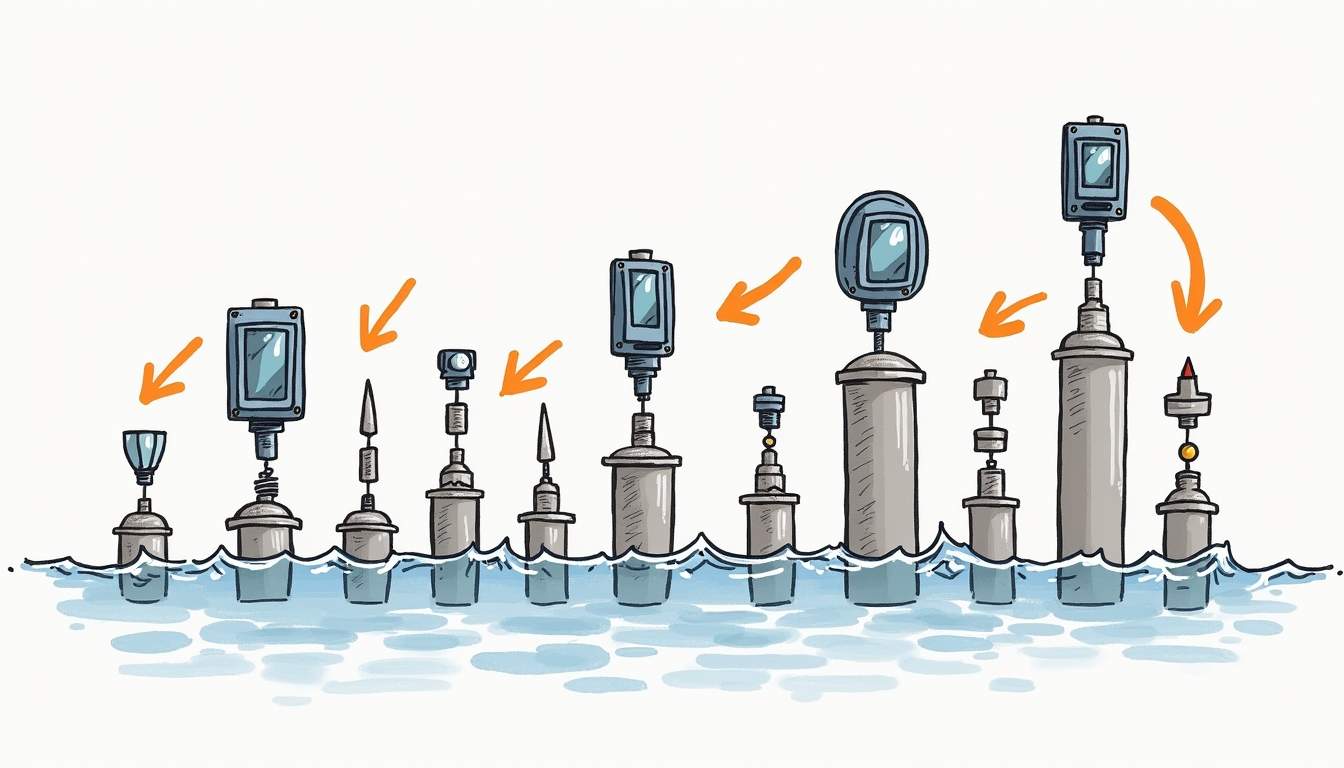
Understanding Level Switches: Types, Applications, and Benefits
Level switches are critical components in various industries, ensuring that processes run smoothly and efficiently. They play a crucial role in managing the levels of liquids and solids in tanks and containers, helping prevent overflow and ensuring optimal operational conditions. In this article, we will explore what level switches are, their different types, applications, benefits, and guidance on how to choose the right one for your needs.
What are Level Switches?
Level switches are devices that detect the level of a substance, usually liquids or solids, within a container or environment. When the substance reaches a predetermined level, the switch activates to either open or close a circuit, thereby controlling the operation of pumps, valves, or alarms. This makes level switches integral to maintaining safety and efficiency in various systems.
The Basic Principle of Level Switches
The basic principle behind level switches involves a simple on/off mechanism. When the level of the substance touches the switch, it either changes its state or activates another device. For instance, if a liquid reaches a high point, a level switch may signal a pump to turn off, preventing overflow. Conversely, if the level is too low, it may trigger a pump to turn on, ensuring adequate supply.
This straightforward principle underpins a wide range of designs and implementations, from simple mechanical switches to complex electronic systems, ensuring adaptability to different environments and materials. For example, in industrial applications, level switches can be found in tanks storing chemicals, where precise control is critical to avoid hazardous spills. In residential settings, they can be used in sump pumps to prevent flooding, showcasing their versatility across various sectors.
Key Components of Level Switches
Level switches typically feature several essential components regardless of their type, including:
- Sensor: The component that detects the level of the material, identifying when it reaches a specified set point.
- Actuator: This element triggers a change in state (on/off) once the sensor detects the pre-defined level.
- Output Signal: The communication mechanism that informs other system components, such as alarms or control systems.
- Housing: The protective casing that maintains the integrity of the switch during operation, often designed to withstand environmental stresses.
By understanding these key components, users can better appreciate how level switches operate and their role in broader systems. Additionally, the choice of materials for these components is crucial; for instance, sensors may be made from stainless steel or plastic, depending on the chemical properties of the substances being monitored. This ensures durability and reliability, especially in harsh environments where exposure to corrosive materials is common.
Moreover, the technology behind level switches is continually evolving. Modern level switches may incorporate advanced features such as wireless communication, allowing for remote monitoring and control. This innovation not only enhances operational efficiency but also provides real-time data analytics, enabling users to make informed decisions about their processes. Such advancements are particularly beneficial in industries like water treatment, food and beverage, and pharmaceuticals, where precision and compliance with safety standards are paramount.
Different Types of Level Switches
Level switches are classified into various types based on their operational principles and mechanisms. This section explores the most common types, each suited to specific applications and materials.
Mechanical Level Switches
Mechanical level switches use physical mechanisms to detect changes in level. These could be as simple as a float rising and falling with the liquid level, which actuates a switch. Their design is straightforward and typically low-cost, making them popular in many applications.
One common example is a float switch, which rises with the liquid level and activates a relay switch. However, their mechanical nature can be susceptible to wear and tear and may not always be suitable for high-viscosity or highly corrosive materials. Additionally, mechanical switches may require regular maintenance to ensure proper functioning, particularly in environments with fluctuating temperatures or pressures that could affect the float's buoyancy.
Electronic Level Switches
Electronic level switches utilize sensors and electronic circuits to detect levels. These devices can offer greater accuracy and flexibility compared to mechanical switches. They can include technologies such as capacitive, ultrasonic, and radar-based sensing.
With no moving parts, electronic level switches are generally more durable and reliable, especially in demanding environments. They can provide immediate feedback and are well-suited for large-scale industrial applications where precision is crucial. Furthermore, many electronic level switches can be integrated into automated systems, allowing for remote monitoring and control, which enhances operational efficiency and reduces the need for manual intervention.
Magnetic and Float Level Switches
Magnetic and float level switches combine the principles of buoyancy and magnetism. These switches use a float with a magnet that moves in accordance with the fluid level. When the float reaches a certain point, it activates a reed switch or another contact that can control pumps and valves.
These switches are often used in water treatment plants, wastewater management, and other applications where the level of water or other fluids needs to be consistently monitored. Their reliable operation in varying conditions makes them a preferred choice for many critical applications. Moreover, magnetic float switches can be designed to operate in hazardous environments, as they can be constructed from materials that resist corrosion and withstand extreme temperatures, ensuring longevity and safety in challenging conditions. This versatility makes them an essential component in many industrial processes, where maintaining the correct fluid levels is vital for operational success.
Applications of Level Switches
Level switches find application across various sectors due to their versatility and effectiveness. Understanding the specific applications can help in identifying the right type of switch for individual needs.
Industrial Use of Level Switches
In the industrial sector, level switches are employed in manufacturing processes, chemical handling, and storage operations. They aid in avoiding overflow situations, reducing risks of spills and environmental damage.
Additionally, in processes like mixing or batching, level switches ensure that operations proceed as planned by maintaining optimal levels of ingredients or materials. Their reliability translates directly into operational efficiency and safety. Furthermore, in industries such as food and beverage, level switches are crucial for maintaining the quality and consistency of products, as they help monitor and control the levels of liquids in tanks and silos, ensuring that production runs smoothly without interruptions.
Level Switches in Home Appliances
Home appliances frequently utilize level switches, particularly in appliances such as washing machines and dishwashers. These switches help regulate water levels for effective cleaning cycles, preventing overflow or inadequate water supply.
The integration of level switches helps enhance the user experience by providing automated responses and ensuring appliances operate within their designed specifications. In addition to washing machines, level switches are also found in water heaters and sump pumps, where they play a vital role in maintaining proper water levels. This not only improves energy efficiency but also prolongs the lifespan of the appliances by preventing potential damage from improper water levels.
Level Switches in the Automotive Industry
In the automotive sector, level switches play a critical role in fuel monitoring, coolant levels, and other fluid measurements. They ensure that vehicles operate safely and efficiently, providing indications when maintenance is required.
As automobiles become increasingly advanced with various monitoring systems, level switches will continue to be a pivotal part of their operation, contributing to reliability and safety on the roads. Moreover, with the rise of electric vehicles, level switches are being adapted to monitor battery fluid levels and other essential fluids, ensuring optimal performance and safety. These advancements highlight the evolving nature of level switch applications, as they become integral to the next generation of automotive technology, enhancing both performance and user confidence in vehicle operations.
Benefits of Using Level Switches
The implementation of level switches in various applications brings numerous advantages that enhance operations and safety. Here are some key benefits to consider.
Enhancing Safety with Level Switches
One of the primary benefits of level switches is their ability to enhance safety. By providing real-time monitoring of liquid or solid levels, these devices help prevent overflow situations that may lead to spillage or environmental hazards.
Moreover, they can trigger alarms or emergency cut-off mechanisms, significantly reducing the chances of accidents in industrial environments or when dealing with hazardous materials. In addition to these immediate safety features, level switches also contribute to regulatory compliance. Many industries are subject to strict environmental regulations, and having a reliable level monitoring system in place can help ensure adherence to these standards, thus safeguarding both the environment and the company's reputation.
Improving Efficiency through Level Switches
Level switches contribute to operational efficiency by ensuring that processes are maintained within optimal parameters. Automatic control of pumps and valves helps in eliminating manual monitoring, thereby reducing labor costs and minimizing human error.
In industries such as food processing, where levels need to be consistently monitored, level switches guarantee product quality and consistency, leading to happier customers and reduced waste. Furthermore, in sectors like water treatment and chemical processing, the integration of level switches allows for better resource management. By optimizing the use of raw materials and minimizing waste, companies can not only enhance their bottom line but also promote sustainable practices that are increasingly important in today's market.
Cost-Effectiveness of Level Switches
Investing in level switches can lead to significant savings in the long run. By preventing overflow and spills, companies avoid costly cleanup, fines, and potential legal ramifications associated with environmental violations.
Moreover, the reduced need for manual oversight translates to lower labor costs. With the advancements in technology, many level switches now boast longevity and minimal maintenance, further adding to their cost-effectiveness. Additionally, the initial investment in these devices can often be offset by the reduction in operational disruptions and downtime. For businesses that rely heavily on continuous processes, such as manufacturing and energy production, the reliability provided by level switches can be a game-changer, ensuring that production schedules are met without unexpected interruptions.
Choosing the Right Level Switch
Selecting the correct level switch is crucial for the effectiveness of any application. This section outlines factors that should influence your decision-making process.
Factors to Consider When Selecting a Level Switch
Several factors must be considered when choosing a level switch to ensure optimal performance:
- Type of Material: Consider the properties of the material (liquid or solid) being monitored. Some switches may not be suitable for highly viscous or corrosive substances.
- Accuracy Requirements: Determine how precisely you need to measure the level. This will influence the type of level switch selected.
- Environmental Conditions: The operating environment can impact the durability and performance of a level switch. Choose materials and designs that can withstand these conditions.
- Power Supply: Assess available power sources, as some level switches may require specific electrical requirements.
By thoroughly evaluating these factors, you can select a level switch that meets your operational needs effectively. Additionally, it is essential to consider the potential for future scalability and integration with existing systems. As industries evolve, the demand for more sophisticated monitoring solutions may arise, making it prudent to select a level switch that can adapt to changing requirements without necessitating a complete overhaul of your setup.
Understanding the Limitations of Different Level Switches
Every type of level switch comes with its own set of limitations. For instance, mechanical switches may be prone to wear and require more maintenance, particularly in harsh environments. On the other hand, electronic level switches may come at a higher upfront cost as compared to mechanical ones.
Understanding these limitations allows users to make informed decisions, balancing the pros and cons according to their unique operational requirements. It is also beneficial to consider the manufacturer's recommendations and reviews to make a well-rounded choice. Furthermore, the installation process and the required calibration for each type of switch can vary significantly. This means that not only should you assess the switch's capabilities, but also the resources and expertise available for installation and ongoing maintenance, which can influence the total cost of ownership over time.
In addition, the choice of level switch can also be influenced by regulatory compliance and safety standards applicable to your industry. Many sectors, such as food and beverage or pharmaceuticals, have stringent guidelines that dictate the materials and technologies that can be used. Ensuring that your selected level switch adheres to these regulations is paramount to avoid costly fines and ensure product safety. By taking all these factors into account, you can make a more comprehensive decision that aligns with both your immediate needs and long-term operational goals.