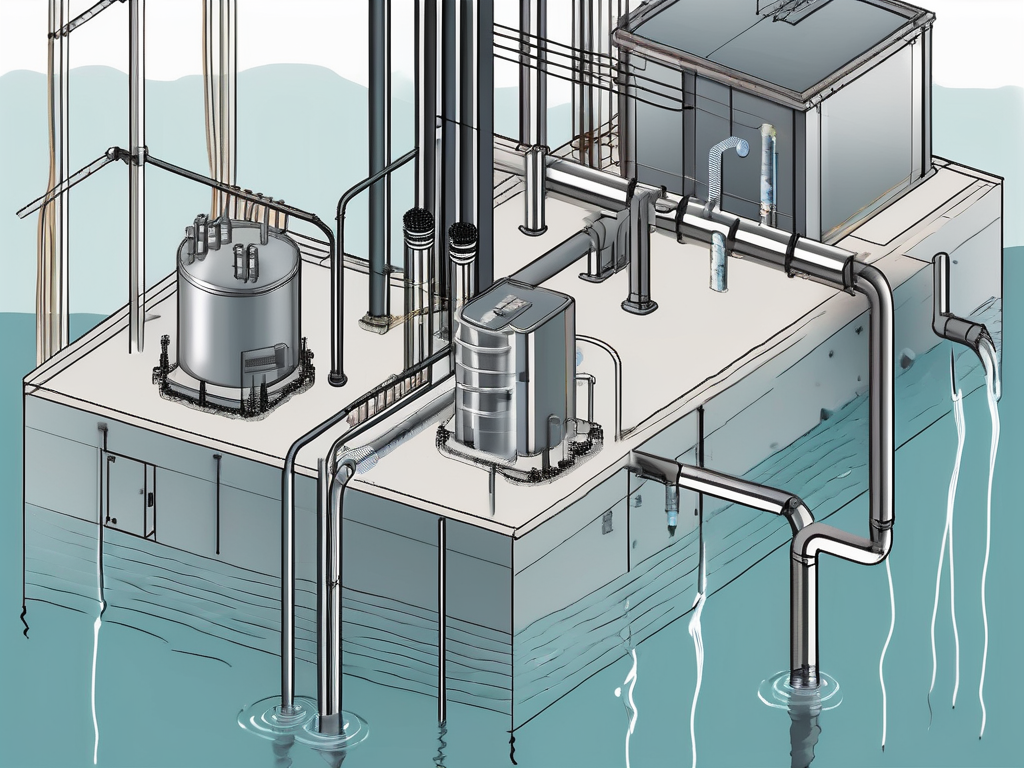
Understanding Lift Station Floats: A Comprehensive Guide
Lift stations play a critical role in the effective management of wastewater systems. At the heart of these operations are lift station floats, essential components that help optimize the performance of wastewater pumps. This comprehensive guide will delve into the workings, importance, and future advancements of lift station floats, providing you with a detailed understanding of their significance in modern wastewater management.
What are Lift Station Floats?
Lift station floats, also referred to as float switches, are devices used in wastewater lift stations to manage the level of liquid within a tank or well. Their primary purpose is to monitor the liquid's height and control the operation of the pumps based on that level. When the liquid reaches a predefined height, the float signal engages the pump, allowing for efficient and controlled pumping operations.
These floats are designed to rise and fall with the liquid level, typically employing a buoyant design that responds to changes in fluid height. When the float is at a designated level, it triggers electrical switches to turn the pump on or off. This automation is vital for maintaining optimal water levels and ensuring that wastewater systems operate smoothly. Additionally, lift station floats are often equipped with features that enhance their durability and performance, such as corrosion-resistant materials and protective casings, which are essential for withstanding the harsh conditions often found in wastewater environments.
The Basic Functionality of Lift Station Floats
The basic functionality of lift station floats can be broken down into two primary actions: sensing and switching. As the wastewater level rises, the float ascends until it reaches a certain height, where it activates an internal switch. This switch then sends a signal to start the pump, causing it to lift the wastewater to treatment facilities. Conversely, when the liquid level drops, a different float (typically situated lower) signals the pump to shut off, preventing dry running and potential damage.
In simple terms, lift station floats create a feedback loop between the liquid level and pump operation. This automated process ensures that the wastewater is efficiently removed from the lift station, reducing the risk of overflow and maintaining system integrity. Furthermore, many modern lift station float systems are integrated with monitoring technologies that allow for remote access and real-time data tracking. This capability enables operators to respond swiftly to any irregularities, enhancing both safety and operational efficiency.
Different Types of Lift Station Floats
There are several types of lift station floats available, each designed to meet specific operational needs. The most common types include:
- Mechanical Floats: These floats use simple mechanical levels to switch the pump on and off. They are easy to install and maintain.
- Electronic Floats: These floats use electronic sensors to detect level changes, providing greater accuracy and reliability.
- Ultrasonic Sensors: These advanced devices measure the distance to the water surface using ultrasonic waves, allowing for precise level readings without any moving parts.
- Pressure Sensors: By measuring the pressure at the bottom of the tank, these sensors can infer water level, thus controlling the pump based on pressure changes.
Choosing the right type of lift station float depends on various factors, including the specific application, environmental conditions, and required reliability. For instance, in environments with high levels of debris or corrosive substances, mechanical floats may be less effective than electronic or ultrasonic options. Moreover, the installation location and the expected range of liquid levels can significantly influence the selection process, ensuring that the chosen float system is optimized for performance and longevity. Understanding these nuances can lead to more informed decisions, ultimately enhancing the efficiency of wastewater management systems.
The Importance of Lift Station Floats in Wastewater Management
Understanding the significance of lift station floats in wastewater management is crucial for maintaining a functional and efficient system. These components not only ensure the smooth operation of pumps but also protect the environment and public health.
Role in Controlling Pump Operation
The primary role of lift station floats is to control the operation of pumps within lift stations. By automatically activating and deactivating pumps as needed, these floats help manage fluid levels effectively. This prevents incidents where the pumps may run continuously, which can lead to wear and tear over time.
By controlling pump operations, lift station floats ultimately contribute to the durability of wastewater facilities. They reduce energy consumption since motors aren't running unnecessarily, leading to lower operational costs for municipalities and businesses alike. Furthermore, the integration of advanced float technologies, such as ultrasonic and pressure-based sensors, allows for even more precise monitoring of liquid levels, enhancing the overall efficiency of the wastewater management process.
Preventing Overflows and Backups
One of the biggest risks in wastewater management is overflow and backup, which can cause significant environmental and health hazards. Lift station floats play a vital role in preventing these occurrences. By accurately monitoring liquid levels and ensuring timely pump activation, they minimize the risk of excess liquid spilling over into the environment.
In addition, lift station floats can help identify potential issues before they escalate into larger problems, making them essential tools for maintaining the efficiency of sewage systems. Regular monitoring can indicate when the pump needs servicing, preventing costly emergency repairs and disruptions. Moreover, the implementation of alarm systems linked to the float mechanisms can alert operators immediately when levels reach critical thresholds, allowing for swift action to mitigate risks. This proactive approach not only safeguards public health but also preserves local ecosystems from the detrimental effects of untreated wastewater entering natural water bodies.
How Lift Station Floats Work
The operational mechanisms of lift station floats are quite fascinating and usually involve a blend of mechanical and electrical principles. To fully grasp how they function, an in-depth look at their mechanism and components is essential.
The Mechanism of Lift Station Floats
A lift station float works primarily on the principle of buoyancy. As wastewater levels in the lift station rise, the float moves upward, activating a switch that engages the pump. This mechanism can be mechanical or electronic, depending on the design of the float.
In mechanical floats, the simple connection of a float to a lever system activates the switch. In contrast, electronic floats may utilize microprocessors to relay the float's position to the control systems, adding a layer of sophistication and reliability. The choice between mechanical and electronic systems often hinges on factors such as the complexity of the wastewater system, the required precision of the float's operation, and environmental conditions that may affect performance.
Understanding the Float Switch
The float switch is an integral part of how lift station floats function. It can come in different designs, including tethered float switches and vertical float switches. Each design has its own benefits, and the choice often comes down to specific application requirements.
A tethered float switch is typically suspended by a cable, allowing it to move freely with the liquid level. Conversely, vertical float switches are fixed at a point while the float moves up and down, providing a compact solution ideal for smaller tanks. Understanding the switch mechanism is crucial for troubleshooting and maintaining lift station operations. Moreover, the materials used in the construction of these floats can significantly influence their durability and performance. For instance, floats made from high-density polyethylene (HDPE) are resistant to corrosion and can withstand harsh chemical environments, making them suitable for a variety of wastewater applications. Additionally, advancements in float technology have led to the development of smart floats that can provide real-time data on water levels, enhancing monitoring capabilities and enabling proactive maintenance strategies.
Troubleshooting Common Lift Station Float Problems
Just like any technical device, lift station floats can experience issues that hinder their performance. Understanding common problems and their solutions can be beneficial for operators and maintenance teams.
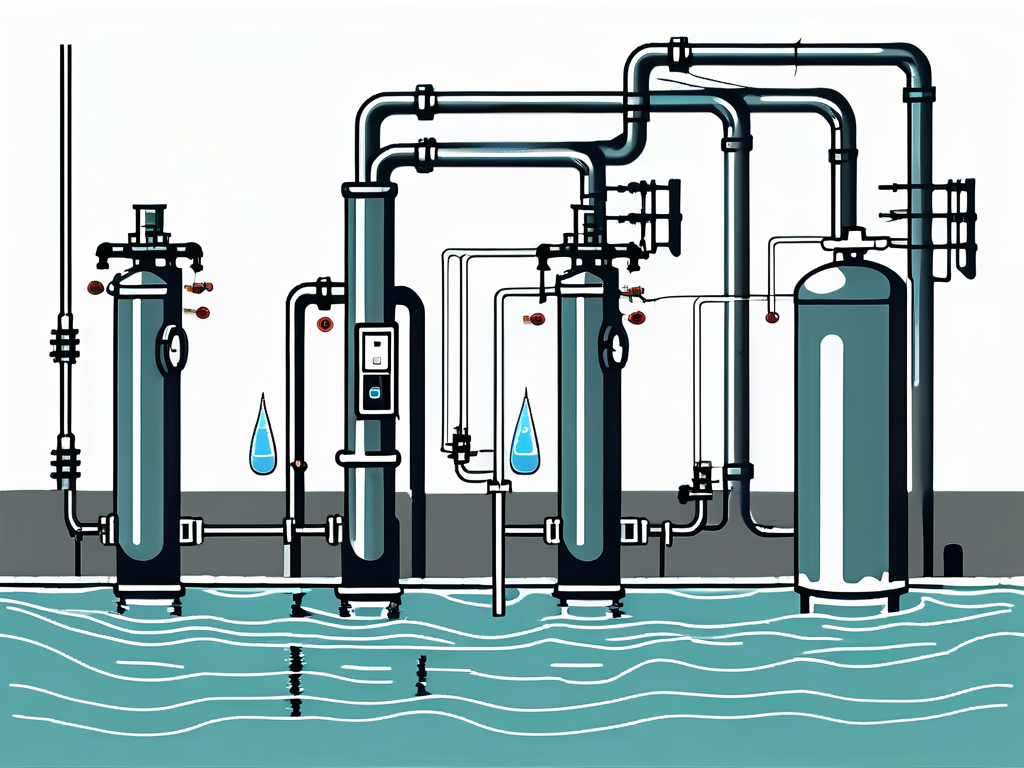
Identifying Common Issues
Some common issues associated with lift station floats include:
- Sticking Floats: These can remain stuck in one position, causing inaccurate readings and potential overflows.
- Electrical Failures: Broken connections or corroded wiring can lead to failure in the switching mechanism.
- Debris Accumulation: Floating debris can obstruct the movement of the float, affecting its functionality.
Regular inspections can help identify these issues early, allowing for timely repairs and maintenance. In addition to these common problems, operators should also be aware of the impact of environmental factors such as temperature fluctuations and chemical exposure, which can exacerbate wear on float components. For instance, extreme temperatures can cause materials to become brittle, while exposure to harsh chemicals can lead to degradation of the float's surface, further complicating performance.
Maintenance Tips for Lift Station Floats
Maintaining lift station floats is key to ensuring their longevity and reliability. Here are some essential tips for maintenance:
- Regularly inspect floats for signs of wear and tear.
- Ensure that the float is free of obstructions and debris.
- Test the electrical connections to prevent failures.
- Clean the floats as needed to avoid fouling and malfunction.
Implementing a robust maintenance schedule can enhance the efficiency of lift station floats and extend their lifespan. Additionally, operators should consider documenting maintenance activities and any issues encountered during inspections. This record-keeping can provide valuable insights over time, helping to identify patterns that may indicate underlying problems. Furthermore, training staff on the importance of proper float operation and maintenance can foster a proactive approach, ensuring that all team members are equipped to recognize potential issues before they escalate into costly repairs or system failures.
Choosing the Right Lift Station Floats
With various options available, selecting the right lift station float can be daunting. Key considerations include environmental factors, space constraints, and the specific requirements of your wastewater pumping system. The right choice not only ensures efficient operation but also contributes to the longevity of the entire lift station setup, minimizing the risk of costly repairs and downtime.
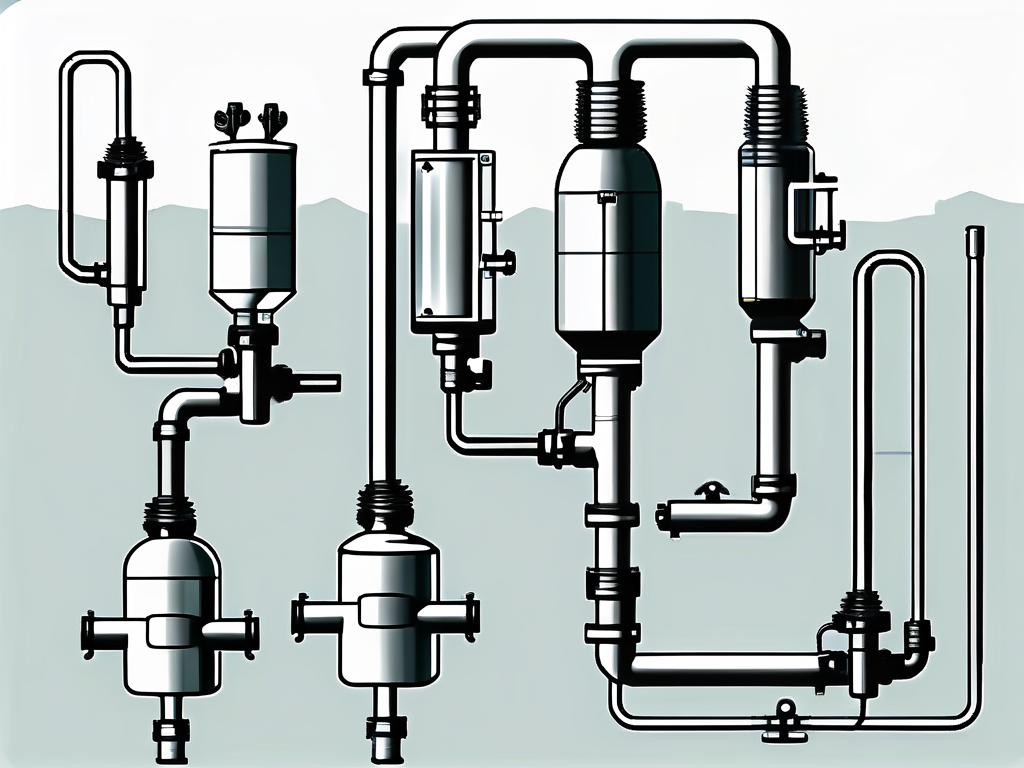
Factors to Consider When Selecting Lift Station Floats
When choosing lift station floats, consider the following factors:
- Fluid Type: Ensure compatibility with the type of wastewater being managed. Different fluids can have varying densities and chemical compositions, which can affect float performance.
- Environmental Conditions: Assess temperature, pressure, and potential corrosive elements in the environment. For instance, extreme temperatures can affect the materials used in float construction, while corrosive substances may necessitate the use of specialized coatings or materials.
- Space Limitations: Evaluate the physical space available for float installation. In tight spaces, compact float designs may be necessary to ensure proper operation without hindering other equipment.
Taking the time to consider these factors can lead to more effective and reliable wastewater management solutions. Additionally, understanding the specific operational demands of your facility can help tailor your selection to enhance overall system performance, ensuring that the lift station operates smoothly under varying conditions.
The Pros and Cons of Various Float Types
Each type of lift station float has its advantages and disadvantages. For example:
- Mechanical Floats: Pros include simplicity and ease of installation. Cons might involve maintenance challenges and susceptibility to mechanical failure. Regular inspections are often required to ensure they remain functional.
- Electronic Floats: These offer greater accuracy and reliability; however, they can be more complex and costly to install. Their advanced features often include programmable settings, allowing for customization based on specific operational needs.
- Ultrasonic Sensors: Pros include no moving parts, providing long-lasting functionality; cons include higher initial costs and potential sensitivity to external factors. They can be particularly advantageous in applications where traditional floats may struggle, such as in turbulent or rapidly changing fluid levels.
Understanding these trade-offs is essential in making an informed decision that aligns with your operational needs. Furthermore, it is crucial to consider the long-term implications of your choice, as the right float can significantly reduce maintenance costs and improve the reliability of your wastewater management system over time. Investing in quality floats may also enhance the overall efficiency of the lift station, leading to better resource management and environmental compliance.
The Future of Lift Station Floats
The realm of lift station floats is continually evolving, with advancements driven by technology and a focus on sustainability. Keeping an eye on these trends can benefit wastewater management practices.
Technological Advancements in Lift Station Floats
Emerging technologies are enhancing the performance and reliability of lift station floats. Developments in smart sensors and IoT connectivity are at the forefront, allowing for real-time monitoring and control.
These innovations facilitate remote diagnostics, enabling operators to respond quickly to potential issues before they escalate. Furthermore, advanced analytics can predict maintenance needs, reducing downtime and operational costs. The integration of machine learning algorithms can also optimize the operation of lift stations by analyzing historical data and identifying patterns that may indicate future performance issues.
Additionally, the use of cloud-based platforms for data storage and analysis allows for greater collaboration among teams, ensuring that all stakeholders have access to the same information. This interconnected approach not only enhances operational efficiency but also fosters a culture of proactive management within wastewater facilities.
Sustainability and Lift Station Floats
As with many industrial applications, there’s a growing emphasis on sustainability within wastewater management. Lift station floats are increasingly designed with eco-friendly materials and energy-efficient technologies.
By investing in sustainable float solutions, municipalities can improve their environmental footprint while enhancing the operational efficiency of their wastewater systems. This forward-thinking approach not only meets regulatory standards but also supports community well-being. Moreover, the implementation of solar-powered floats can significantly reduce energy consumption, making lift stations more self-sufficient and less reliant on traditional power sources.
Furthermore, the lifecycle assessment of lift station floats is becoming a critical factor in their design and selection. Manufacturers are now taking into account the entire lifecycle of the product, from raw material extraction to disposal, ensuring that the floats are not only effective during their operational phase but also minimize waste and environmental impact at the end of their life. This holistic view of sustainability is paving the way for innovative solutions that benefit both the environment and the economy.
In conclusion, understanding lift station floats is essential for anyone involved in wastewater management. By grasping their functionality, troubleshooting common issues, and staying informed on current technological advancements, we can ensure the sustainable and efficient operation of our vital wastewater systems.