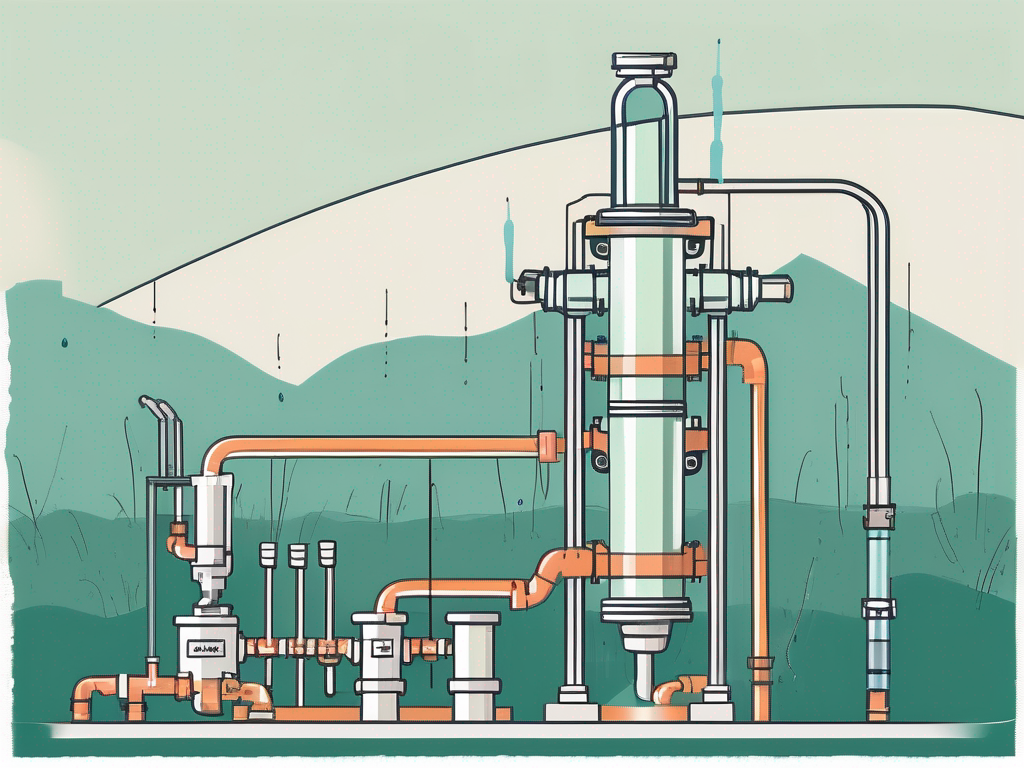
Understanding Well Chlorine Injection Systems: A Comprehensive Guide
Well chlorine injection systems are essential for ensuring safe and clean water from groundwater sources. These systems play a crucial role in purifying water by eliminating harmful bacteria and contaminants. This article will explore the components, mechanisms, and types of chlorine used in these systems, as well as maintenance, safety measures, and future advancements.
The Basics of Well Chlorine Injection Systems
Before diving deeper, it’s essential to establish a foundational understanding of what well chlorine injection systems are and their significance in water treatment.
What is a Well Chlorine Injection System?
A well chlorine injection system is a water treatment method utilized to disinfect groundwater. It introduces chlorine, a powerful disinfectant, directly into the water supply. The system typically includes specialized equipment that interacts with the water flow, ensuring a controlled and effective treatment process.
These systems are particularly useful in areas where groundwater may be contaminated with pathogens or other harmful substances. By utilizing chlorine injection, water quality can be improved, making it safe for drinking, cooking, and other residential uses. Additionally, these systems can be tailored to meet the specific needs of different water sources, allowing for adjustable chlorine levels based on the degree of contamination detected. This flexibility is crucial for ensuring that the water remains safe without over-chlorination, which can lead to undesirable tastes and odors.
Importance of Chlorine in Water Treatment
Chlorine is widely recognized for its efficacy in killing bacteria, viruses, and other microorganisms. It disrupts the cellular processes of these harmful entities, rendering them inactive.
Not only does chlorine provide immediate disinfection, but its residual effect also helps maintain water safety during storage and distribution. This makes chlorine a preferred choice in many municipal and private well water treatment applications. Furthermore, the use of chlorine in water treatment is supported by extensive research and regulatory guidelines, ensuring that its application meets health standards. Monitoring systems are often integrated into well chlorine injection setups, allowing for real-time assessment of chlorine levels and water quality. This continuous oversight is vital for adapting treatment protocols as needed, especially in regions prone to seasonal variations in water quality or during extreme weather events that may affect groundwater sources.
Components of a Well Chlorine Injection System
A well chlorine injection system is composed of several critical components, each designed to facilitate effective chlorine treatment.
Chlorine Injector
The chlorine injector is the heart of the system. It functions by creating a suction that draws chlorine solution into the water stream. The injector must be calibrated accurately to ensure the correct dosage of chlorine is mixed with water.
Maintaining the injector's performance is vital, as improper injection can lead to either insufficient disinfection or excessive chlorine levels, both of which can be detrimental. Regular maintenance checks, including cleaning and recalibrating the injector, are essential to ensure optimal performance and longevity of the system. Additionally, monitoring the injector's pressure and flow rates can provide insights into its operational efficiency, allowing for timely adjustments to be made before issues arise.
Chlorine Solution Tank
The chlorine solution tank stores the concentrated chlorine solution. It is essential for this tank to be made of materials that can withstand the corrosive nature of chlorine.
Moreover, the tank needs to be easily accessible for refilling and maintenance. Regular inspection of the solution level aids in planning when to refill to ensure continuous operation. It's also beneficial to incorporate a level sensor or gauge that provides real-time data on the chlorine solution's volume, helping operators manage supply more effectively. In addition, the tank should be equipped with safety features, such as a venting system to release any built-up pressure, ensuring safe handling and operation of the chlorine solution.
Injection Check Valve
The injection check valve is installed downstream from the injector. Its primary function is to prevent backflow of water into the chlorine tank, ensuring that only treated water is delivered to the user.
This component plays a crucial role in maintaining system integrity and preventing contamination of the chlorine solution. Regular testing of the check valve is necessary to confirm its functionality, as any failure could compromise the entire disinfection process. Additionally, using a high-quality check valve that can withstand the pressures and chemical interactions within the system is essential for long-term reliability. Operators should also be aware of the signs of wear and tear, such as leaks or unusual noises, which may indicate that the check valve needs to be replaced or serviced to maintain optimal system performance.
Working Mechanism of Chlorine Injection Systems
Understanding the operational mechanism of chlorine injection systems provides insight into how they effectively disinfect water. These systems are widely employed in municipal water treatment facilities, swimming pools, and various industrial applications, ensuring that the water is safe for consumption and use. The efficiency of chlorine injection systems is critical, as they play a vital role in public health by eliminating harmful microorganisms that can lead to waterborne diseases.
Chlorine Injection Process
The chlorine injection process begins when water flows through the system. The injector creates negative pressure, which draws chlorine solution from the tank. The solution is then mixed with the incoming water, ensuring a homogeneous blend. This mixing is often facilitated by a venturi or an eductor, which enhances the contact between the chlorine and water, maximizing the disinfection potential. The design of the injector is crucial, as it must be calibrated to deliver the correct dosage of chlorine based on the flow rate and the specific requirements of the water being treated.
This mixture then travels through the piping system, where it is subjected to a predetermined contact time, allowing sufficient chlorine to interact with any pathogens present. The piping system may include various valves and flow meters that help in monitoring and controlling the chlorine levels. Additionally, the system often incorporates safety features, such as automatic shut-off valves and alarms, to prevent over-injection, which can lead to harmful levels of chlorine in the water.
Chlorine Contact Time
Contact time is a crucial factor in the effectiveness of chlorine disinfection. It refers to the duration the chlorine remains in contact with the water before use. This time allows the chlorine to oxidize and neutralize contaminants, including bacteria, viruses, and organic matter. The effectiveness of chlorine as a disinfectant is influenced not only by contact time but also by factors such as water temperature, pH levels, and the presence of competing substances that can consume chlorine.
Inappropriate contact time can result in ineffective treatment. Thus, it is essential to design systems with adequate blending and retention time to achieve optimal disinfection results. Engineers often conduct detailed studies and simulations to determine the ideal contact time for different water sources and conditions. Furthermore, advancements in technology have led to the development of real-time monitoring systems that can adjust chlorine injection rates based on the water quality, ensuring that the disinfection process remains effective under varying circumstances. This adaptability is crucial for maintaining the safety and quality of drinking water in an ever-changing environment.
Types of Chlorine Used in Injection Systems
There are various forms of chlorine available for use in injection systems, each with its advantages and applications.
Liquid Chlorine
Liquid chlorine is one of the most commonly used types in injection systems. It is highly effective and provides a concentrated form of chlorine, which can be easily diluted into the water.
This form is suitable for large-scale applications but requires careful handling due to its hazardous nature. Facilities using liquid chlorine must implement robust safety protocols, including proper ventilation and protective equipment for staff. Additionally, regular training sessions on emergency response procedures are essential to mitigate the risks associated with chlorine exposure.
Chlorine Tablets
Chlorine tablets are often used for smaller systems or in situations where liquid chlorine may not be ideal. These tablets dissolve gradually, providing a controlled release of chlorine into the water.
Although they are easier to handle, they may require additional equipment to ensure proper dissolution and mixing. Many systems utilize floaters or tablet feeders to automate the process, allowing for consistent chlorine levels without manual intervention. This convenience makes chlorine tablets a popular choice for residential pools and smaller commercial applications, where ease of use and safety are paramount.
Chlorine Gas
Chlorine gas is another potent option used in industrial applications. It is delivered through specialized systems that manage the gas safely and effectively.
This method is highly efficient but poses significant safety risks, requiring stringent handling and monitoring protocols. Facilities must be equipped with gas detection systems and emergency scrubbers to neutralize any accidental releases. Moreover, operators must undergo specialized training to handle chlorine gas safely, ensuring they are well-prepared to respond to any potential leaks or emergencies. The use of chlorine gas is often justified in large-scale water treatment facilities due to its cost-effectiveness and ability to treat large volumes of water quickly.
Maintenance of Well Chlorine Injection Systems
Regular maintenance of chlorine injection systems is vital to ensure their longevity and effectiveness in treating water.
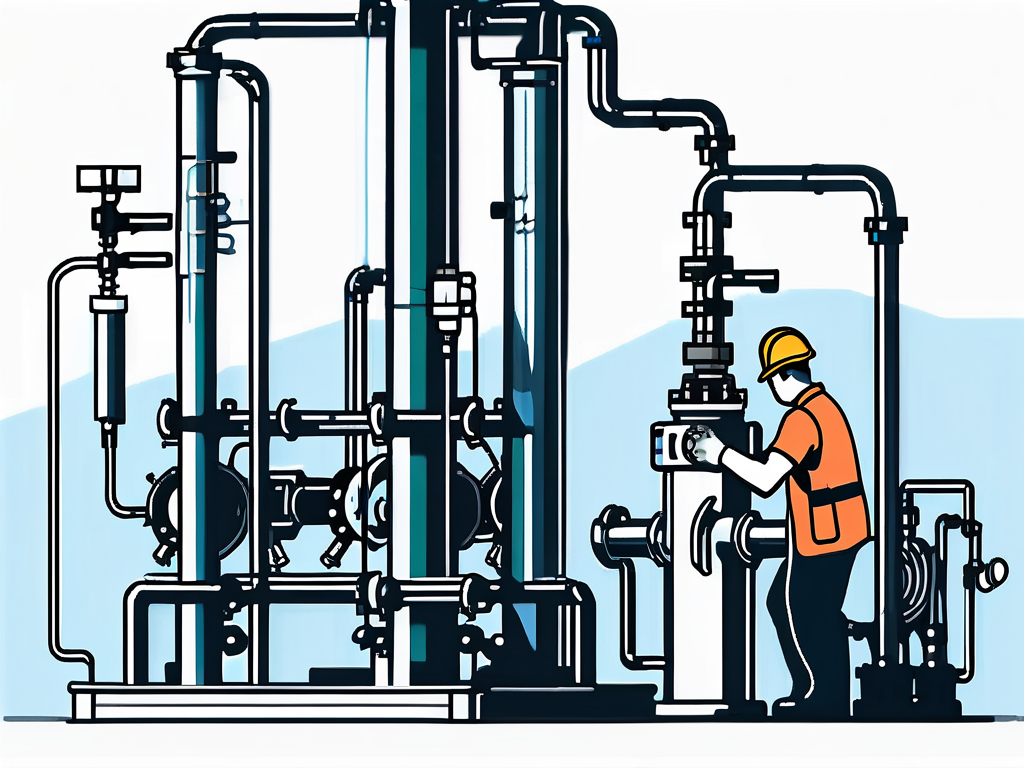
Regular System Checks
Conducting periodic inspections of the system components helps identify potential issues before they escalate. Users should monitor the chlorine levels, check for leaks, and ensure that all parts are functioning correctly.
Additionally, keeping detailed records of maintenance activities assists in tracking system performance and needs over time. This documentation can be invaluable for troubleshooting, as it provides insights into patterns of wear or recurring issues that may need addressing. Furthermore, it can aid in compliance with local regulations regarding water treatment, ensuring that the system operates within the required safety and health standards.
Cleaning and Replacing Components
Over time, certain components may require cleaning or replacement due to wear and tear. Regular cleaning of the chlorine solution tank and injector is necessary to prevent buildup and clogs, which can impair the system's function.
Replacement parts should be sourced from reputable suppliers to ensure compatibility and quality, thereby maintaining the system's efficiency. It is also advisable to establish a routine schedule for these tasks, as this can help mitigate the risk of unexpected breakdowns. Additionally, users should familiarize themselves with the manufacturer's guidelines for maintenance to ensure that all procedures are performed correctly and safely, thereby extending the lifespan of the system and optimizing its performance.
Safety Measures for Using Chlorine Injection Systems
The use of chlorine injection systems necessitates a strong focus on safety to prevent accidents and ensure the well-being of operators and users.
Handling Chlorine Safely
Chlorine is a hazardous substance, and proper handling procedures must be followed. Operators should wear appropriate personal protective equipment (PPE), including gloves and goggles, when working with chlorine solutions.
Moreover, clear signage indicating the presence of chlorine and proper storage protocols should be established to inform and protect individuals who may come into contact with the system. It is also crucial to ensure that all containers used for storing chlorine are clearly labeled and made from materials that are resistant to corrosion, as chlorine can react with certain substances, leading to dangerous situations. Regular inspections of storage areas should be conducted to check for leaks or deterioration of containers, ensuring that any potential hazards are addressed promptly.
Emergency Procedures
In the event of a chlorine leak or spill, having an emergency response plan is essential. This plan should include immediate evacuation procedures, contact information for emergency services, and detailed steps for containment and cleanup.
Regular training sessions for all personnel involved with the system will help ensure everyone is familiar with the emergency procedures and ready to act if needed. Additionally, conducting periodic drills can reinforce the training and help identify any gaps in the response plan. It is also advisable to have emergency equipment, such as spill kits and neutralizing agents, readily available and easily accessible in the vicinity of the chlorine injection system. This preparedness can significantly reduce response time and mitigate the impact of any accidental release of chlorine into the environment.
Choosing the Right Chlorine Injection System
When considering a well chlorine injection system, it is crucial to evaluate multiple factors to select the right system for your needs.
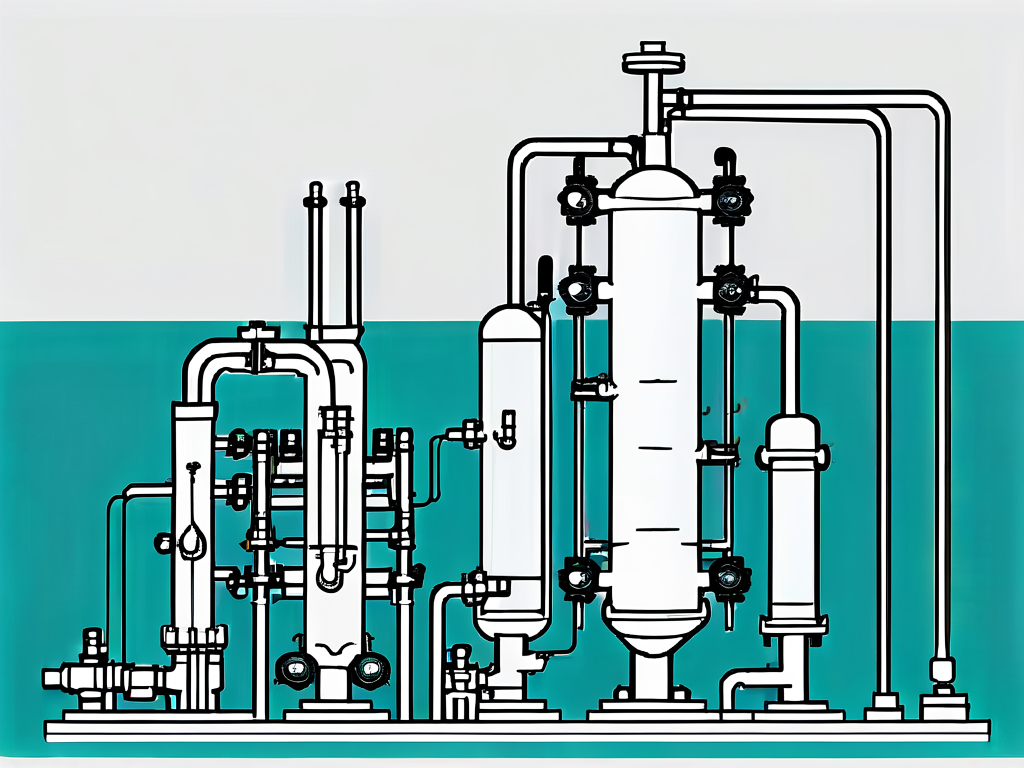
Factors to Consider
Several factors influence the choice of a chlorine injection system, including the volume of water to be treated, the contamination level, and the available space for equipment installation. Additionally, budget constraints must also be taken into account.
Conducting a thorough assessment of your specific water treatment requirements will assist in making an informed decision.
Understanding Your Water Needs
Assessing your water needs involves understanding the quality of the water source, potential contaminants, and usage requirements. Perform routine water testing to identify what specific issues your chlorine injection system must address.
This information will guide you in selecting the most suitable chlorine form and system specifications to ensure effective water treatment.
Moreover, it is essential to consider the long-term implications of your choice. Different chlorine injection systems may have varying maintenance needs, operational costs, and environmental impacts. For instance, some systems may require more frequent monitoring and adjustments, while others might be more automated and user-friendly. Understanding these aspects can help you avoid unexpected expenses and ensure that your system operates efficiently over time.
Additionally, it is beneficial to consult with water treatment professionals or suppliers who can provide insights based on their experience with different systems. They can help you navigate through the complexities of chlorine types, such as gas, liquid, or tablet forms, and their respective advantages and disadvantages. This collaborative approach can lead to a more tailored solution that meets both your immediate and future water treatment needs.
Troubleshooting Common Issues
Even the best-maintained systems can encounter issues, making troubleshooting knowledge essential for efficient operation.
Low Chlorine Levels
One common issue with chlorine injection systems is low chlorine levels in the treated water. This could be a result of inadequate injector performance or blockages in the system.
Regularly testing the chlorine concentration in the output water is essential for identifying any discrepancies and addressing them promptly. It is advisable to implement a routine schedule for testing, perhaps weekly or bi-weekly, depending on the system's usage and the volume of water being treated. Additionally, keeping a log of chlorine levels can help identify patterns or recurring issues, allowing for more informed troubleshooting and maintenance decisions.
Injector Malfunctions
Injector malfunctions can lead to improper dosing of chlorine, impacting overall water treatment effectiveness. If inconsistent dosing or fluctuation is noted, inspecting and servicing the injector should be priority actions.
Training operators on the common signs of injector issues can facilitate quicker troubleshooting and resolution. This training can include hands-on demonstrations and the use of diagnostic tools to assess injector performance. Moreover, establishing a clear communication protocol for reporting and documenting any injector-related concerns can help ensure that issues are addressed swiftly, minimizing downtime and maintaining water quality standards.
System Blockages
Another issue that can arise is system blockages, which may occur due to debris, sediment, or biofilm accumulation within the piping or injector components. These blockages can significantly hinder the flow of chlorine, leading to inadequate disinfection and potential health risks. Regular maintenance checks, including flushing the system and inspecting filters, can help prevent such blockages from developing.
Implementing a proactive maintenance schedule that includes cleaning and replacing filters as needed can greatly enhance the longevity and efficiency of the chlorine injection system. Additionally, educating staff on the importance of monitoring water clarity and odor can serve as an early warning system for potential blockages, allowing for timely interventions before they escalate into more significant issues.
The Future of Chlorine Injection Systems
As technology continues to evolve, the realm of well chlorine injection systems is also progressing to meet modern demands.
Technological Advancements
New innovations such as automated dosing systems and enhanced monitoring solutions are being integrated into chlorine injection systems. These advancements can improve efficiency and safety by providing real-time data and alerts to operators.
Embracing such technologies can facilitate better decision-making and ensure optimal water quality management.
Environmental Impact and Sustainability
The future of chlorine injection systems also involves a growing commitment to sustainability and minimizing environmental impacts. This includes exploring alternative disinfection methods and sustainable sourcing of materials used in system components.
Companies are beginning to invest in research and development to enhance the sustainability of water treatment processes, leading to environmentally friendly practices in the industry.
In conclusion, well chlorine injection systems are pivotal in ensuring safe and clean water for various applications. Understanding their components, mechanisms, maintenance, and safety measures are essential for effective operation. As technology and practices evolve, practitioners must stay informed to maximize these systems' benefits while addressing contemporary environmental challenges.